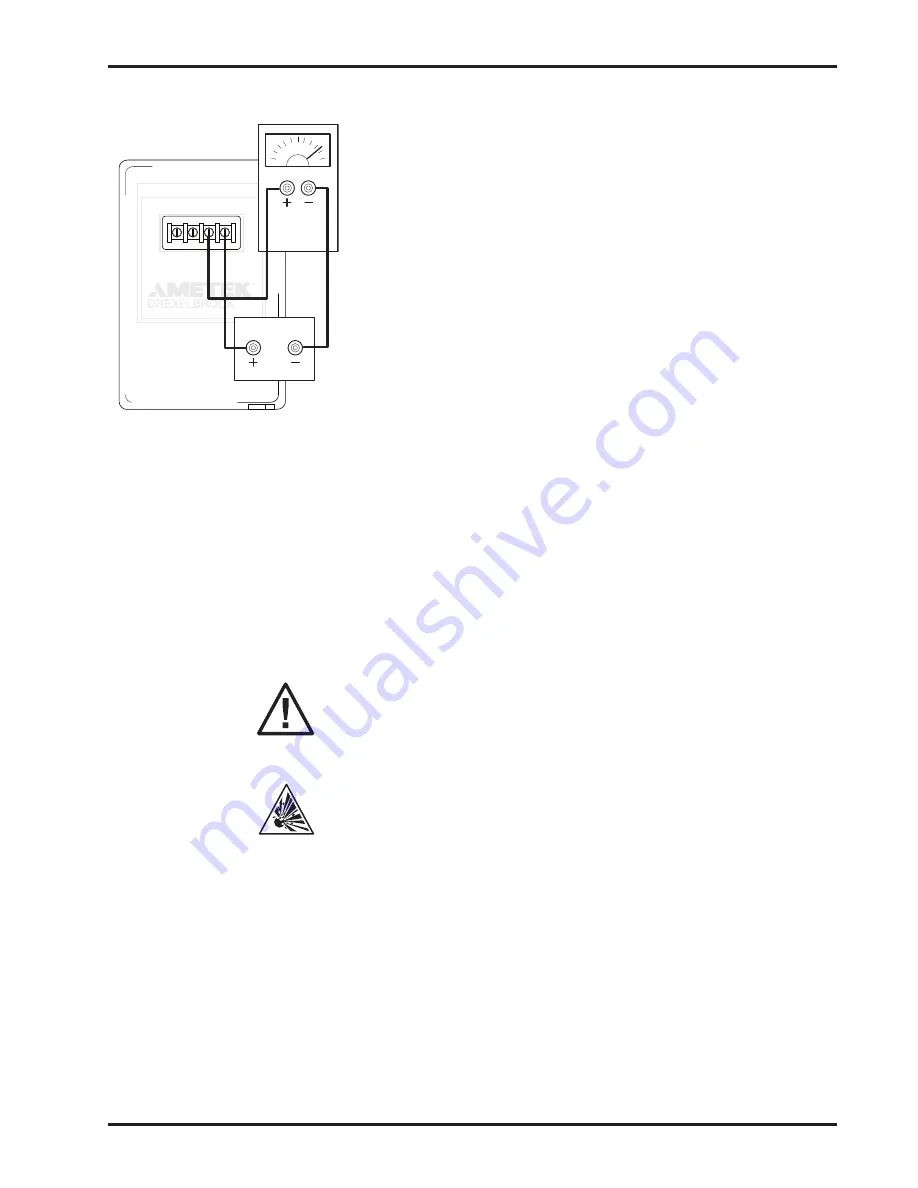
Troubleshooting
65
1. Remove coaxial cable from the transmitter
terminals.
2. Without changing any data stored in the
transmitter, connect a Drexelbrook capacitance
substitution box (401-6-8) or an NPO test capacitor
from the probe terminal to the GND terminal on
the transmitter. (Select a capacitance value that
produces between 4 and 20 mA of loop current.)
3. Observe the loop current over a 12-hour period to
confirm the stability of the unit. If the readings
remain stable for this period, then the problem
is not in the transmitter. If the loop current has
changed more than 1% during the test period, then
the unit is defective. Please contact the Service
department for further instructions regarding
repair or replacement.
6.7 Troubleshooting Sensing Element
Troubleshooting sensing element requires use of
an analog ohmmeter
. Digital meters do not properly
measure resistance for the purpose of this test. An
analog ohmmeter typically provides more current when
measuring resistance, which is required to detect a
pinhole or crack in the sensing element insulation. In
addition, digital meters frequently give erroneous results
due to a battery-like effect when dissimilar metals contact
conductive liquids.
CAUTION: Sensing element is intrinsically
safe. Therefore, when using this product, it is
recommended that all service activity comply with
appropriate guidelines.
Remove sensing element from vessel to a safe area.
Test outlined in steps 1 and 2 can be performed
in a metal test vessel filled with high conductivity
water. Depending on locality, tap water may not be
suitable. If not, a spoonful of table salt may work.
In the following tests, if it is not possible to raise or lower
level in vessel, sensing element may be suspended in a
metal pipe or other container that is filled with conductive
water (see above note) and connected to grounded sensing
element condulet. If container is not metallic, then a
ground wire or rod is needed to be placed into the water
and referenced to sensing element condulet or mounting
devices.
6.6.1 Transmitter Drift Test (Continued)
GND
V -
V +
M -
SERIAL NO.
MODEL NO.
YEAR OF MANUFACTURE
24 VDC
Transmitter
mA Meter
on Record
Figure 6-4
Summary of Contents for RCT 10 series
Page 4: ......
Page 8: ...SECTION 1...
Page 26: ...SECTION 3...
Page 46: ...SECTION 4...
Page 57: ...Configuration Calibration 49 5 4 Set Up Procedures...
Page 58: ...RCT 10 11 12 13 Series 50 5 4 Set Up Procedures Continued...
Page 59: ...Configuration Calibration 51 5 4 Set Up Procedures Continued...
Page 66: ...SECTION 6...
Page 80: ...SECTION 7...
Page 86: ...APPENDIX A...
Page 87: ...Appendix A A 1 APPENDIX A APPROVAL DRAWINGS A 1 ATEX APPROVAL DRAWINGS...
Page 88: ...RCT 10 11 12 13 Series A 2 A 1 ATEX APPROVAL DRAWINGS Continued...
Page 89: ...Appendix A A 3 A 1 ATEX APPROVAL DRAWINGS Continued...
Page 90: ...RCT 10 11 12 13 Series A 4 A 1 ATEX APPROVAL DRAWINGS Continued...
Page 91: ...Appendix A A 5 A 1 ATEX APPROVAL DRAWINGS Continued...
Page 92: ...RCT 10 11 12 13 Series A 6 A 1 ATEX APPROVAL DRAWINGS Continued...
Page 93: ...Appendix A A 7 A 1 ATEX APPROVAL DRAWINGS Continued...
Page 94: ...RCT 10 11 12 13 Series A 8 A 1 ATEX APPROVAL DRAWINGS Continued...
Page 95: ...Appendix A A 9 A 1 ATEX APPROVAL DRAWINGS Continued...
Page 96: ...RCT 10 11 12 13 Series A 10 A 1 ATEX APPROVAL DRAWINGS Continued...
Page 97: ...Appendix A A 11 A 1 ATEX APPROVAL DRAWINGS Continued...
Page 98: ...RCT 10 11 12 13 Series A 12 A 2 CSA APPROVAL DRAWINGS...
Page 99: ...Appendix A A 13 A 2 CSA APPROVAL DRAWINGS Continued...
Page 100: ...RCT 10 11 12 13 Series A 14 A 2 CSA APPROVAL DRAWINGS Continued...
Page 101: ...Appendix A A 15 A 2 CSA APPROVAL DRAWINGS Continued...
Page 102: ...RCT 10 11 12 13 Series A 16 A 2 CSA APPROVAL DRAWINGS Continued...
Page 103: ...Appendix A A 17 A 2 CSA APPROVAL DRAWINGS Continued...
Page 104: ...RCT 10 11 12 13 Series A 18 A 2 CSA APPROVAL DRAWINGS Continued...
Page 105: ...Appendix A A 19 A 2 CSA APPROVAL DRAWINGS Continued...
Page 106: ...RCT 10 11 12 13 Series A 20 A 2 CSA APPROVAL DRAWINGS Continued...
Page 107: ...Appendix A A 21 A 2 CSA APPROVAL DRAWINGS Continued...
Page 108: ...RCT 10 11 12 13 Series A 22 A 2 CSA APPROVAL DRAWINGS Continued...
Page 109: ...Appendix A A 23 A 2 CSA APPROVAL DRAWINGS Continued...
Page 110: ...RCT 10 11 12 13 Series A 24 A 2 CSA APPROVAL DRAWINGS Continued...
Page 111: ...Appendix A A 25 A 2 CSA APPROVAL DRAWINGS Continued...
Page 112: ...RCT 10 11 12 13 Series A 26 A 2 CSA APPROVAL DRAWINGS Continued...
Page 113: ...Appendix A A 27 A 2 CSA APPROVAL DRAWINGS Continued...
Page 114: ...RCT 10 11 12 13 Series A 28 A 2 CSA APPROVAL DRAWINGS Continued...
Page 115: ...Appendix A A 29 A 3 FM APPROVAL DRAWINGS Continued...
Page 116: ...RCT 10 11 12 13 Series A 30 A 3 FM APPROVAL DRAWINGS Continued...
Page 117: ...Appendix A A 31 A 3 FM APPROVAL DRAWINGS Continued...
Page 118: ...RCT 10 11 12 13 Series A 32 A 3 FM APPROVAL DRAWINGS Continued...
Page 119: ...Appendix A A 33 A 3 FM APPROVAL DRAWINGS Continued...
Page 120: ...RCT 10 11 12 13 Series A 34 A 3 FM APPROVAL DRAWINGS Continued...
Page 121: ...Appendix A A 35 A 3 FM APPROVAL DRAWINGS Continued...
Page 122: ...RCT 10 11 12 13 Series A 36 A 3 FM APPROVAL DRAWINGS Continued...
Page 123: ...Appendix A A 37 A 3 FM APPROVAL DRAWINGS Continued...
Page 124: ...RCT 10 11 12 13 Series A 38 A 3 FM APPROVAL DRAWINGS Continued...
Page 125: ...Appendix A A 39 A 3 FM APPROVAL DRAWINGS Continued...
Page 126: ...RCT 10 11 12 13 Series A 40 A 3 FM APPROVAL DRAWINGS Continued...
Page 127: ...Appendix A A 41 A 3 FM APPROVAL DRAWINGS Continued...
Page 128: ...RCT 10 11 12 13 Series A 42 A 3 FM APPROVAL DRAWINGS Continued...
Page 129: ...Appendix A A 43 A 3 FM APPROVAL DRAWINGS Continued...
Page 130: ...RCT 10 11 12 13 Series A 44 A 3 FM APPROVAL DRAWINGS Continued...
Page 131: ...A 3 FM APPROVAL DRAWINGS Continued...
Page 133: ......