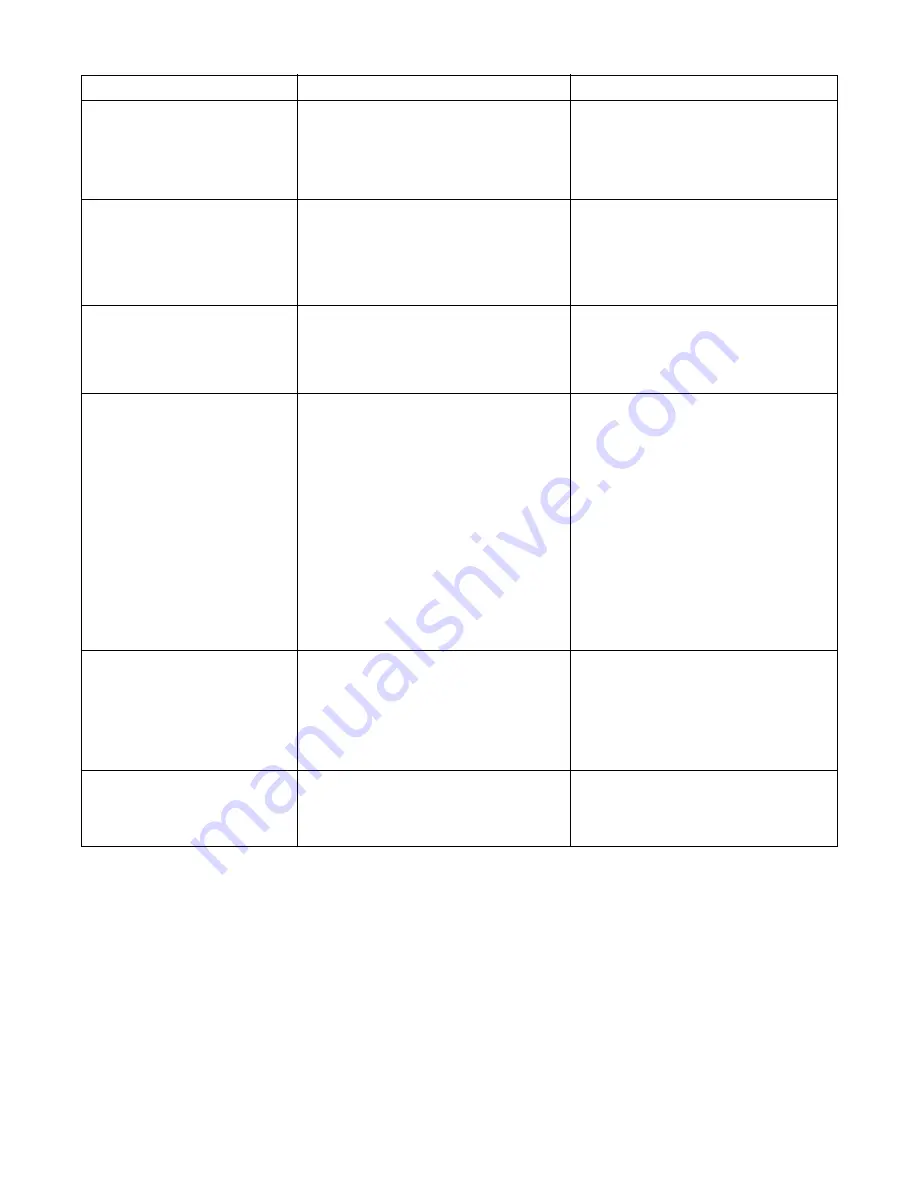
1. Check connections-term. MV feeds main
valve.
2. Replace pilot assembly.
3. Replace if needed.
4. If present, replace main valve; if not,
replace S8600 Igniter.
1. Manifold pressure is too high; adjust.
Burner orifi ces may be too large:
verify/replace if req'd.
2. Increase air fl ow; check fan size.
Check for proper voltage.
3.
Replace.
1. Replace or tighten.
2. Clean power venter wheel.
3. Realign power venter wheel.
4. Oil bearings on power venter motor.
(Refer to label on motor).
1. Replace fuse or turn on power.
2. Check and tighten all wiring connections
per diagrams. Thermostat wires tagged
"W" and "G" must be connected together
(unless special thermostats are used; if so,
see thermostat wiring diagram). See
electrical connections.
3.
Replace
motor.
4. Check for 24V across 1 and 3 terminals on
fan relay. If 24V is present, jumper terminals
numbered 2 and 4. If motor runs, the relay
is defective and must be replaced. If 24V is
not present, check wiring per diagrams.
5. Turn up thermostat.
6. Replace defective hi-limit switch.
1. Be sure venter relay terminals are
connected per diagrams.
2. Replace venter relay.
3. Check motor amps against motor name
plate rating, check voltage, replace power
venter motor if defective.
4. Refer to label on motor.
1. Check all wiring.
2. Refer to H & N symptoms.
3. Replace venter relay.
X. Pilot lights — Main valve does not
energize.
Y. Hi-Limit switch tripping.
Z. Noisy power venter.
AA. Power venter will not run.
BB. Power venter motor turns on
and off while burner is
operating.
CC. Power ventor motor will not
stop.
Power Vented Blowers Troubleshooting Guide
SYMPTOMS
POSSIBLE CAUSE(S)
CORRECTIVE ACTION
23
1. Loose S8600 connections.
2. Cracked or broken sensor ceramic.
3. Check sensor/spark lead for continuity.
4. Measure 24 volts from term. MV to term.
MV/PV.
1. Unit is overfi ring.
2. Air fl ow too low
3.
Defective
switch.
1. Power venter wheel loose.
2. Power venter wheel dirty.
3. Power venter wheel rubbing housing.
4. Bearings are dry.
1. Lack of power at unit.
2.
Loose
wiring.
3. Defective motor overload protector or
defective motor.
4. Defective power venter relay.
5. Thermostat not calling for heat.
6. Defective hi-limit switch.
1. Power venter relay improperly wired.
2. Defective venter relay switch.
3. Motor overload protector cycling on and off.
4. Motor not properly oiled.
1. Improperly wired venter relay.
2. Main burners not lighting while
thermostat calls for heat.
3. Defective venter relay.
Summary of Contents for IIEB-11
Page 14: ...14 Figure 13 Figure 14...
Page 15: ...15 Figure 15 Figure 16...
Page 30: ...NOTES 30...
Page 31: ...NOTES 31...
Page 32: ...260 NORTH ELM ST WESTFIELD MA 01085 TEL 413 568 9571 FAX 413 562 8437 www mestek com...