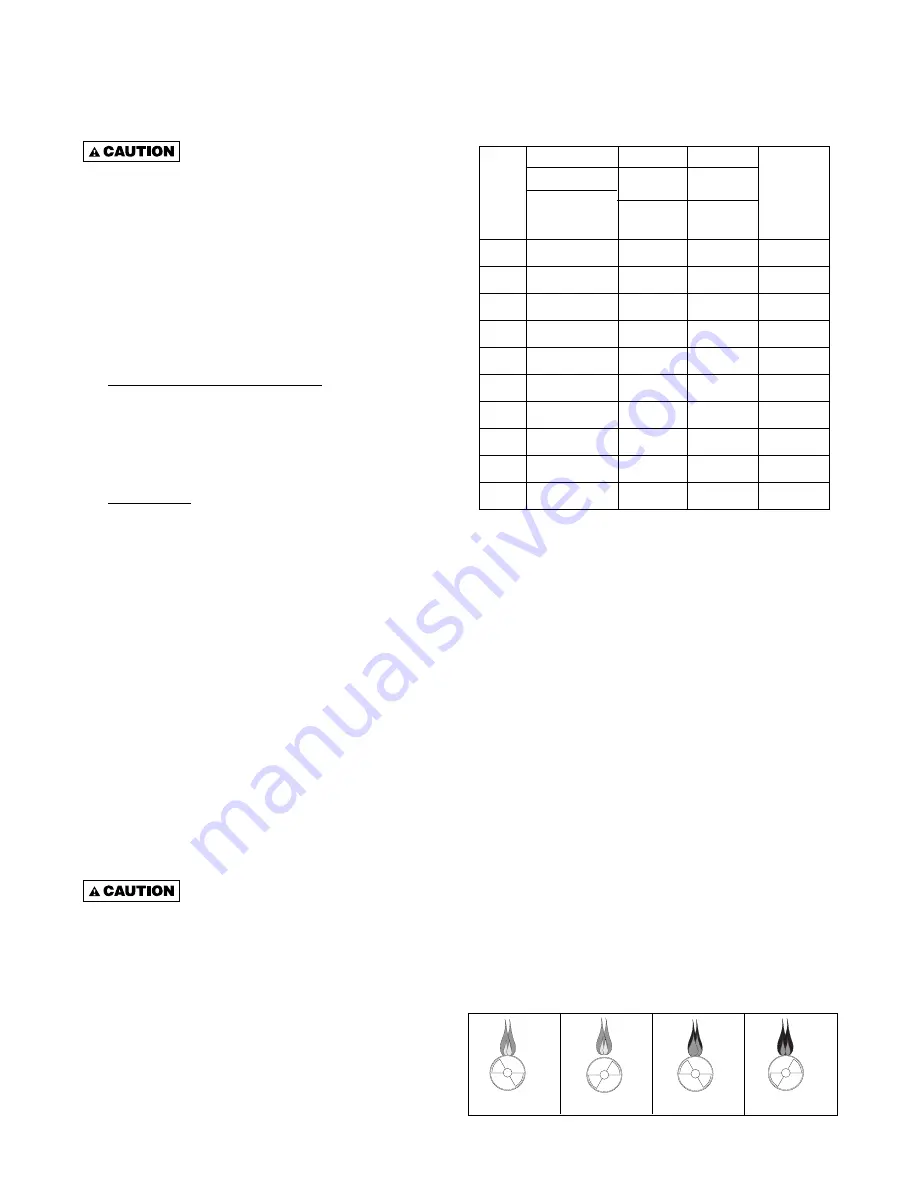
3. The adjusted manifold pressure should not vary
more than 10% from the pressure specified in
Table 7.
Table 7 - Main Burner Orifi ce Schedule*
PRIMARY AIR SHUTTER ADJUSTMENT
After the unit has been operating for at least 15
minutes, adjust the primary air flow to the burners.
Turn the friction-locked, manually-rotated air shutters
clockwise to close, or counterclockwise to open.
For correct air adjustment, close the air shutter until
yellow tips in the flame appear. Then open the air
shutter to the point just beyond the position where
yellow tipping disappears. Refer to Figure 18.
NOTICE: There may be momentary and spasmodic
orange flashes in the flame. This is caused by the
burning of airborne dust particles, and not to be
confused with the yellow tipping, which is a stable
or permanent situation when there is insufficient
primary air.
Figure 18 - Main Burner Flames
18
GAS INPUT RATE
Check the gas input rate as follows. To calculate
metric units, refer to general safety section for metric
conversions/SI units):
Never overfire the unit heater, as
this may cause unsatisfactory operation or shorten
the life of the heater.
the life of the heater.
1. Turn off all gas appliances that use gas through the
same meter as the unit heater.
2. Turn gas ON to the unit heater.
3. Clock the time in seconds required to burn one
cubic foot of gas by checking the gas meter.
4. Insert the time required to burn one cubic foot of
gas into the following formula and compute the
input rate.
3600 (Sec. Per Hr.) x Btu/Cu. Ft
= Input Rate
Time (Sec.)
For example, assume the Btu content of one cubic foot
of gas equalled 1000 and that it takes 18 seconds to
burn one cubic foot of gas.
3600 x 1000
= 200,000 Btu/Hr.
18
NOTICE: If the computation exceeds or is less
than 95 percent of the gas Btu/hr. input rating (see
Specifi cations), adjust the gas pressure.
Adjust the gas pressure as follows:
1. NATURAL GAS: Best results are obtained when
the unit heater is operating at its full input rating with
the manifold pressure of 3.5 inches W.C. (0.9 kPa).
Adjustment of the pressure regulator is not normally
necessary since it is preset at the factory. However,
fi eld adjustment may be made as follows:
a. Attach manometer at pressure tap plug adjacent
to control outlet.
b. Remove regulator adjustment screw cap,
located on combination gas valve.
c. With a small screwdriver, rotate the adjustment
screw counterclockwise to decrease or clock-
wise to increase pressure.
Do not force beyond stop limits.
d. Replace regulator adjustment screw cap.
2. PROPANE GAS: An exact manifold pressure of 10.0
inches W.C. (2.5 kPa) must be maintained for proper
operation of the unit heater. If the unit is equipped
with a pressure regulator on the combination gas
valve, follow steps “a” through “d” above. If the unit
is not so equipped, the propane gas supply system
pressure must be regulated to attain this manifold
operating pressure.
*
INPUT
IN
1000
BTU
2500 BTU/Ft
3
(93.1 MJ/m
3
)
PROPANE
TYPE OF GAS
NATURAL
HEATING VALUE
1075 BTU/Ft
3
(40.1 MJ/m
3
)
3.5" W.C.
(0.9 kPA)
1
0" W.C.
(2.5 kPA)
NO. OF
BURNER
ORIFICES
MANIFOLD
PRESSURE
4
5
6
7
8
9
10
12
14
16
100
125
150
175
200
225
250
300
350
400
FT
3
/HR
ORIFICE DRILL
FT
3
/HR
ORIFICE DRILL
FT
3
/HR
ORIFICE DRILL
FT
3
/HR
ORIFICE DRILL
FT
3
/HR
ORIFICE DRILL
FT
3
/HR
ORIFICE DRILL
FT
3
/HR
ORIFICE DRILL
FT
3
/HR
ORIFICE DRILL
FT
3
/HR
ORIFICE DRILL
FT
3
/HR
ORIFICE DRILL
96
42
120
42
140
42
163
42
186
42
210
42
233
42
280
42
326
42
372
42
40
54
50
54
60
54
70
54
80
54
90
54
100
54
120
54
140
54
160
54
* This schedule is for units operating at normal altitudes of 2000 ft. (610m) or
less. For operation at elevations above 2000 feet (610m), input ratings must
be reduced at the rate of 4 percent for each 1000 feet (305m) above sea level.
SPECIAL ORIFICES ARE REQUIRED FOR INSTALLATIONS ABOVE 2000
FEET (610M).
When installed in Canada, any references to deration at altitudes in excess of
2000 feet (610m) are to be ignored. At altitudes of 2000 to 4500 feet (610 to
1372m), the unit heaters must be orifi ced to 90% of the normal altitude rating,
and be so marked in accordance with the ETL certifi cation.
NORMAL
(HARD FLAME)
LIFTING
TOO MUCH AIR)
YELLOW TIPPING
(MARGINAL)
YELLOW FLAME
(TOO LITTLE AIR)
Summary of Contents for IIEB-11
Page 14: ...14 Figure 13 Figure 14...
Page 15: ...15 Figure 15 Figure 16...
Page 30: ...NOTES 30...
Page 31: ...NOTES 31...
Page 32: ...260 NORTH ELM ST WESTFIELD MA 01085 TEL 413 568 9571 FAX 413 562 8437 www mestek com...