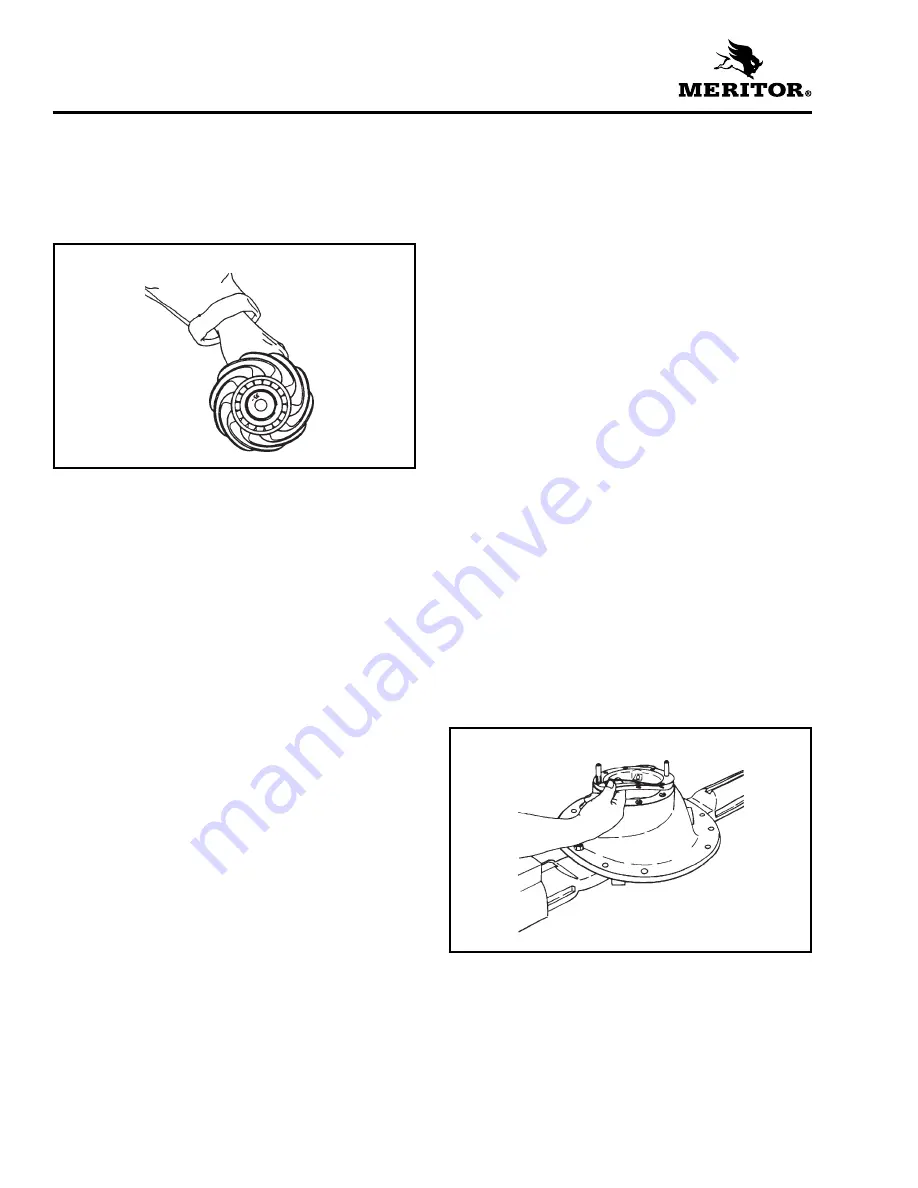
34
18. Check and write down the number engraved
on the end of the pinion. This value indicates
how many hundredths of a millimeter have to
be added or subtracted from the corrected
nominal dimension.
Figure 5.30
.
19. Subtract the corrected specific nominal
dimension (Csnd) from the differential
nominal dimension maximum value (Mv).
The result will be the thickness of the shim
pack(s) to be added to obtain proper drive
pinion/ring gear tooth contact.
Csnd = SND – engraved number
Shim pack thickness = Mv – Csnd
Example:
The following are the values for a 220 differential:
1.
Differential nominal dimension maximum
value (Mv) is determined using a special tool:
Mv = 200.70
2.
Number engraved on the top of the drive
pinion:
– .06
3.
Specific nominal dimension (SND) of this
differential model:
SND = 200.00
From these values we can determine the corrected
specific nominal dimension (Csnd):
Number –6 engraved on the end of the drive
pinion signifies that the variation in the height of
the pinion in relation to the differential nominal
dimension is 0.06 mm lower than the specific
nominal dimension (SND), so:
SND – engraved number = Csnd
200.00 – 0.06 = 199.94
Therefore, 199.94 is the corrected specific nominal
dimension (Csnd) for the differential.
To determine the thickness of the shim pack(s)
needed to obtain a proper drive pinion/ring gear
tooth contact, we subtract Csnd (corrected specific
nominal dimension) from Mv (maximum value).
Mv – Csnd = Thickness of the shim pack
200.70 – 199.94 = 0.76 mm
We therefore have to insert 0.76 mm of shims
between the carrier and the drive pinion assembly
to obtain proper drive pinion/ring gear tooth
contact.
Install the Drive Pinion, Bearing Cage and
Shim Pack into the Carrier
1.
Select and install the adjustment shims for
the pinion case using guide studs (refer to
Section 8) and apply FAG-3 sealant gasket
on the differential case before installing the
shims.
Figure 5.31
.
Figure 5.30
Figure 5.31