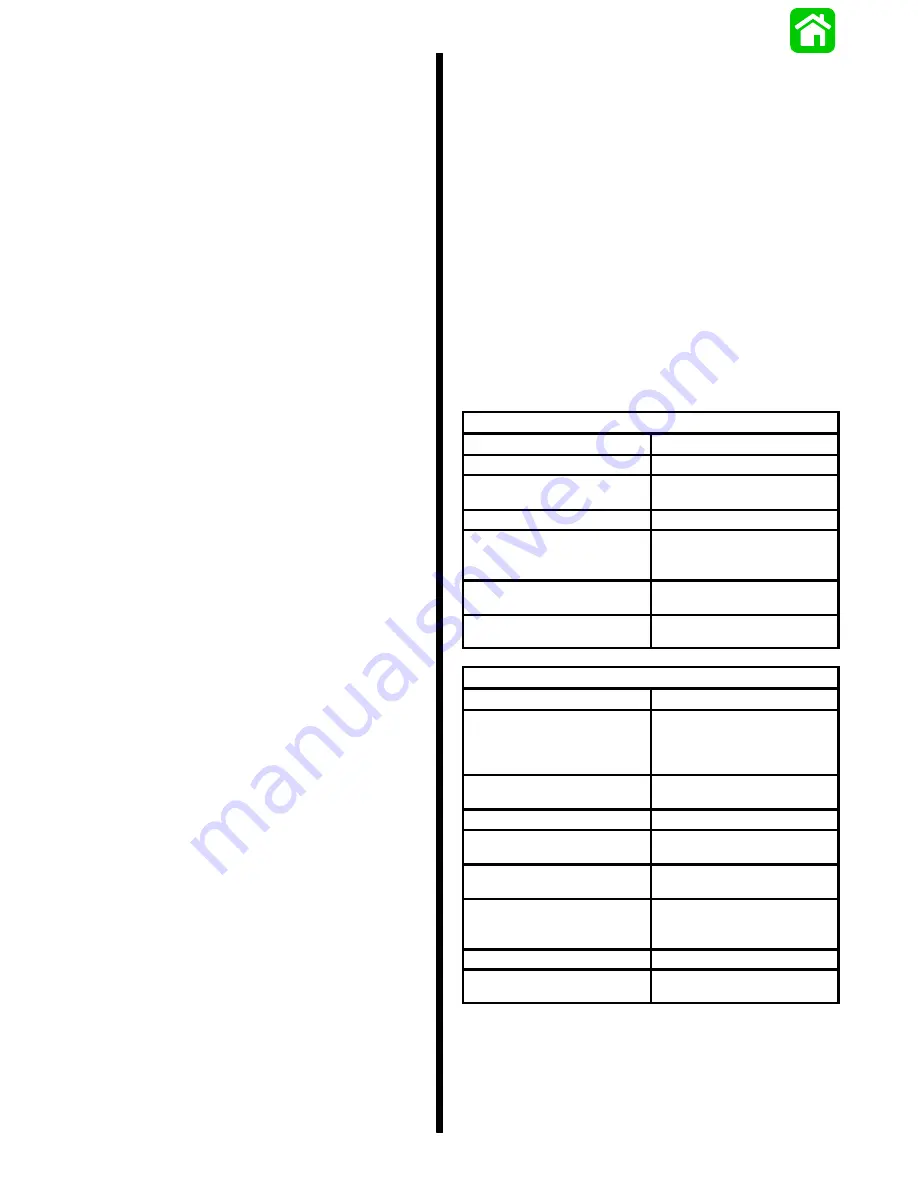
3A-10 - FUEL SYSTEM
90-830234R3
DECEMBER 1997
Theory Of Operation
The fuel pump is a crankcase-pressure-operated, di-
aphragm-type pump. Crankcase pulsating pressure
(created by the up-and-down movement of piston) is
transferred to fuel pump by way of a passage (hole)
between crankcase and fuel pump.
When piston is in an upward motion, a vacuum is
created in the crankcase, thus pulling in a fuel/air
mixture (from carburetor) into crankcase. This vacu-
um also pulls in on the fuel pump diaphragm, thus the
inlet check valve (in fuel pump) is opened and fuel
(from fuel tank) is drawn into fuel pump.
Downward motion of the piston forces the fuel/air
mixture out of the crankcase into the cylinder. This
motion also forces out on the fuel pump diaphragm,
which, in turn, closes the inlet check valve (to keep
fuel from returning to fuel tank) and opens the outlet
check valve, thus forcing fuel to the carburetors.
CHECKING FOR RESTRICTED FUEL FLOW
CAUSED BY ANTI-SIPHON VALVES
While anti-siphon valves may be helpful from a safety
stand-point, they clog with debris, they may be too
small, or they may have too heavy a spring. Summa-
rizing, the pressure drop across these valves can,
and often does, create operational problems and/or
powerhead damage by restricting fuel to the fuel
pump and carburetor(s). Some symptoms of re-
stricted (lean) fuel flow, which could be caused by
use of an anti-siphon valve, are:
•
Loss of fuel pump pressure
•
Loss of power
•
High speed surging
•
Preignition/detonation (piston dome erosion)
•
Outboard cuts out or hesitates upon acceleration
•
Outboard runs rough
•
Outboard quits and cannot be restarted
•
Outboard will not start
•
Vapor lock
Since any type of anti-siphon device must be located
between the outboard fuel inlet and fuel tank outlet,
a simple method of checking [if such a device (or bad
fuel) is a problem source] is to operate the outboard
with a separate fuel supply which is known to be
good, such as a remote fuel tank.
If, after using a separate fuel supply, it is found that
the anti-siphon valve is the cause of the problem,
there are 2 solutions to the problem; either (1) re-
move the anti-siphon valve or (2) replace it with a so-
lenoid-operated fuel shutoff valve.
Testing
Install clear fuel hose(s) between fuel pump and car-
buretor(s). Run engine, and inspect fuel passing thru
hose(s) for air bubbles. If air bubbles are found, see
“Air Bubbles in Fuel Line,” below. If air bubbles are
NOT found, see “Lack of Fuel Pump Pressure,” con-
tinued on next page.
Troubleshooting Fuel Pump
PROBLEM: Air BUBBLES IN FUEL LINE
Possible Cause
Corrective Action
Low fuel in fuel tank.
Fill tank with fuel.
Loose fuel line connection.
Check and tighten all
connections.
Fuel pump fitting loose.
Tighten fitting.
A hole or cut in fuel line.
Check condition of all fuel
lines and replace any found
to be bad.
Fuel pump anchor screw(s)
loose.
Tighten all screws evenly
and securely.
Fuel pump gasket(s)
worn out.
Rebuild fuel pump.
PROBLEM: Lack of Fuel Pump Pressure
Possible Cause
Corrective Action
An anti-siphon valve.
Read “Checking for
Restricted Fuel Flow,
Caused by Anti-Siphon
Valves” preceding.
Air in fuel line.
“Air Bubbles in Fuel Line”,
preceding.
A dirty or clogged fuel filter.
Clean or replace fuel filter.
The fuel pickup in fuel tank
clogged or dirty.
Clean or replace pickup.
Worn out fuel pump
diaphragm.
Rebuild fuel pump.
Defective (hole or crack)
check valve(s) in fuel pump
(unlikely).
Rebuild fuel pump.
Broken check valve retainer.
Rebuild fuel pump.
Pulse hole plugged.
Remove fuel pump and clean
out hole.
Summary of Contents for 100 FourStroke
Page 5: ...1 A 52485 IMPORTANT INFORMATION SPECIFICATIONS ...
Page 13: ...1 C IMPORTANT INFORMATION GENERAL INFORMATION ...
Page 23: ...1 D IMPORTANT INFORMATION OUTBOARD INSTALLATION ...
Page 37: ...A 2 53970 ELECTRICAL IGNITION ...
Page 81: ...B 2 11669 ELECTRICAL CHARGING AND STARTING SYSTEM ...
Page 108: ...C 2 22480 ELECTRICAL TIMING SYNCHRONIZING ADJUSTING ...
Page 119: ...D 2 ELECTRICAL WIRING DIAGRAMS ...
Page 146: ...A 3 53992 FUEL SYSTEM FUEL PUMP ...
Page 148: ...90 830234R3 DECEMBER 1997 FUEL SYSTEM 3A 1 Notes ...
Page 161: ...B 3 FUEL SYSTEM CARBURETOR ...
Page 190: ...C 3 FUEL SYSTEM OIL INJECTION ...
Page 192: ...90 830234R3 DECEMBER 1997 FUEL SYSTEM 3C 1 Notes ...
Page 211: ...4 20032 POWERHEAD ...
Page 215: ...90 830234R3 DECEMBER 1997 POWERHEAD 4 3 Notes ...
Page 292: ...A 5 MID SECTION CLAMP SWIVEL BRACKETS DRIVE SHAFT HOUSING ...
Page 294: ...90 830234R3 DECEMBER 1997 MID SECTION 5A 1 Notes ...
Page 317: ...5 51485 B MID SECTION POWER TRIM S N USA 0G360002 BEL 9934136 BELOW ...
Page 359: ...C 5 55331 MID SECTION POWER TRIM S N USA 0G360003 BEL 9934137 UP ...
Page 364: ...5C 4 MID SECTION 90 830234R3 DECEMBER 1997 Notes ...
Page 408: ...5 D MID SECTION SHOCK ABSORBER ...
Page 413: ...5 E MID SECTION MANUAL TILT ...
Page 451: ...A 6 791 H LOWER UNIT GEAR HOUSING ...
Page 489: ...6 B LOWER UNIT JET DRIVE ...
Page 491: ...90 830234R3 DECEMBER 1997 LOWER UNIT 6B 1 Notes ...
Page 513: ...A 7 50099 ATTACHMENTS CONTROL LINKAGE THROTTLE SHIFT LINKAGE ...
Page 543: ...7 B ATTACHMENTS CONTROL LINKAGE TILLER HANDLE ...
Page 545: ...90 830234R3 DECEMBER 1997 ATTACHMENTS CONTROL LINKAGE 7B 1 Notes ...
Page 567: ...51605 8 MANUAL STARTER ...
Page 569: ...90 830234R3 DECEMBER 1997 MANUAL STARTER 8A 1 Notes ...