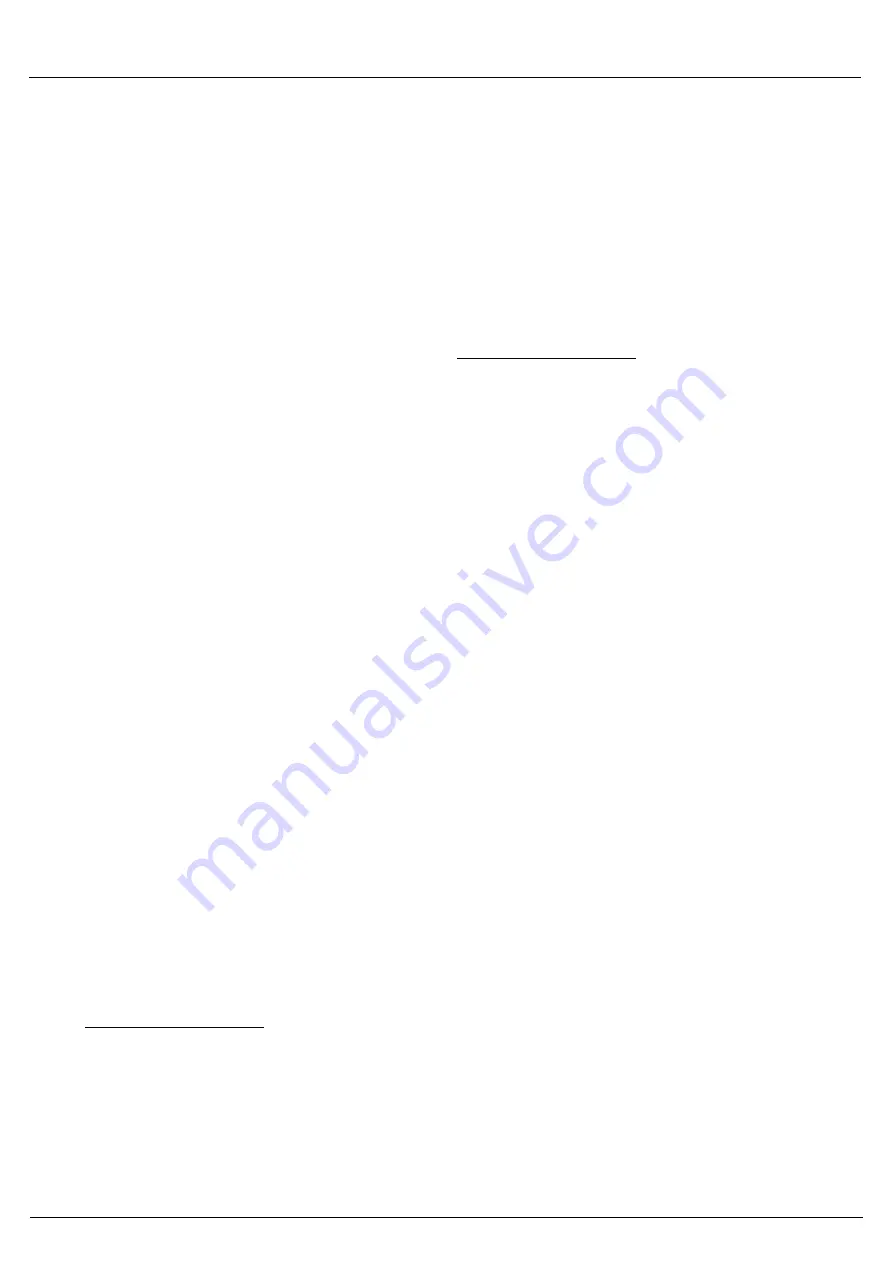
Operation Manual
MELA
quick
®
12
Page 20
8.2
Fault No. 4 ______________________________________________________________
Cause of fault:
The autoclave did not achieve its parameter for
pressure and/or temperature within the supervision
time of 5.5 minutes.
Time of fault:
After program start, during pressure generation
(lamp "READY" blinks).
The following reasons can be given:
8.2.1 Autoclave insufficiently ventilated _________________________________________________
In this case, the feed water pump runs only once
after the start of the program.
For proper function of the autoclave (death of
germs), it is necessary to extract air, respectively
air/steam-mixture, out of the chamber. After a
program start or during pressure generation, air is
extracted through a current channel which branches
off in the rear part of the chamber, leads to the
measuring block and then thron a fine filter to the
inside flow nozzle (43). In this channel the steam-
temperature sensor for the electronic system (35)
(visable from above in the rear opening of the
chamber bottom, under the sieve insert for the
chamber), as well as the temperature sensor of the
thermometer (39), are contacted by the flowing
steam. In front of the hose connection to the
measuring block is an additional steam filter
screwed inside the chamber block (44).
Fault diagnosis:
The autoclave will not properly vent if any of the
following components are clogged: the sieve insert
for the pressure chamber, the fine filter installed
upstream of the nozzle (43), or the steam filter (44).
The autoclave does achieve a pressure of approx.
2.2
bar (for sterilization), or 0.3--0.4
bar for
disinfection within a period of 1.5...3 min. after the
start of the program. Although it maintains this
pressure, an excessively
low temperature (or no temperature at all) is
indicated on the thermometer. The autoclave then
switches over to fault no. 4 after program start, since
the partial pressure of the air is added to that of the
steam, which prevents the saturated-steam
temperature from being achieved at the prescribed
pressure.
Call for a service engineer.
Beyond, every blockage in this area can be
recognised with the transparent Teflon hose which
leads from the measuring block to a T-junction. In
this hose (and thus in the water discharge hose),
you can normally see small amounts of flowing
steam/condensat. The presence of prescribed
temperature (134°C or 105°C) will additionally be
indicated by a LED on the electronic CPU-board.
Fault correction:
Remove the sieve insert. Optical control of
ventilation hole in the chamber (bottom of chamber
at rear rim). This hole should not be covered or
blocked. Check whether somebody has worked
without sieve insert so that instruments have
covered the ventilation hole.
Check flow nozzle (43) and filters (40) and (44), if
necessary also steam filter (34), probably clean or
replace them. Before complete re-assembly it might
be useful to run the autoclave once without fine filter
(40) and flow nozzle (43) to flush the tubing system
and remove any residues.
8.2.2 Pressure switch is wrongly adjusted/defective _______________________________________
In this case, the feed water pump runs only once
after the start of the program.
Diagnosis of fault:
If the autoclave achieves a pressure for sterilization
of less than 2.1 bar (or 0.2 bar for disinfection) within
1.5 ... 3
min., if it remains at this insufficient
pressure, and if the thermometer reaches the
corresponding saturated-steam temperature, then
the pressure switch for sterilization (53) or for
disinfection (54) is not properly set -- or, it is
defective.
The autoclave indicates fault no. 4 without a
repeated start of the pump because the prescribed
supervision temperature cannot be achieved.
Call for a service engineer.
Fault correction:
Adjust the respective pressure switch by turning the
justification screw clockwise so that during pressure
generation, a pressure of 2.25...2.3
bar
(0.3...0.4 bar) will be reached. If the adjustment has
no success, replace the pressure switch.
The autoclave must be placed in the pure pressure-
control mode in order to adjust the pressure switch.
To make this adjustment, first switch off the power
switch (4). Then hook in the two upper wire-clasp
switches (A and B) of the 4 wire-clasp buttons /
switches (32) on the electronic circuit board, at the
lower left on the circuit board (on a blue plastic
base). The second switch from the top has already
been hooked in at the factory. After adjustment work
is completed, make sure that the power switch is off,
and unhook the upper wire-clasp switch (A). If
adjustment is not possible, the pressure switch must
be replaced, and the new switch must be properly
adjusted.