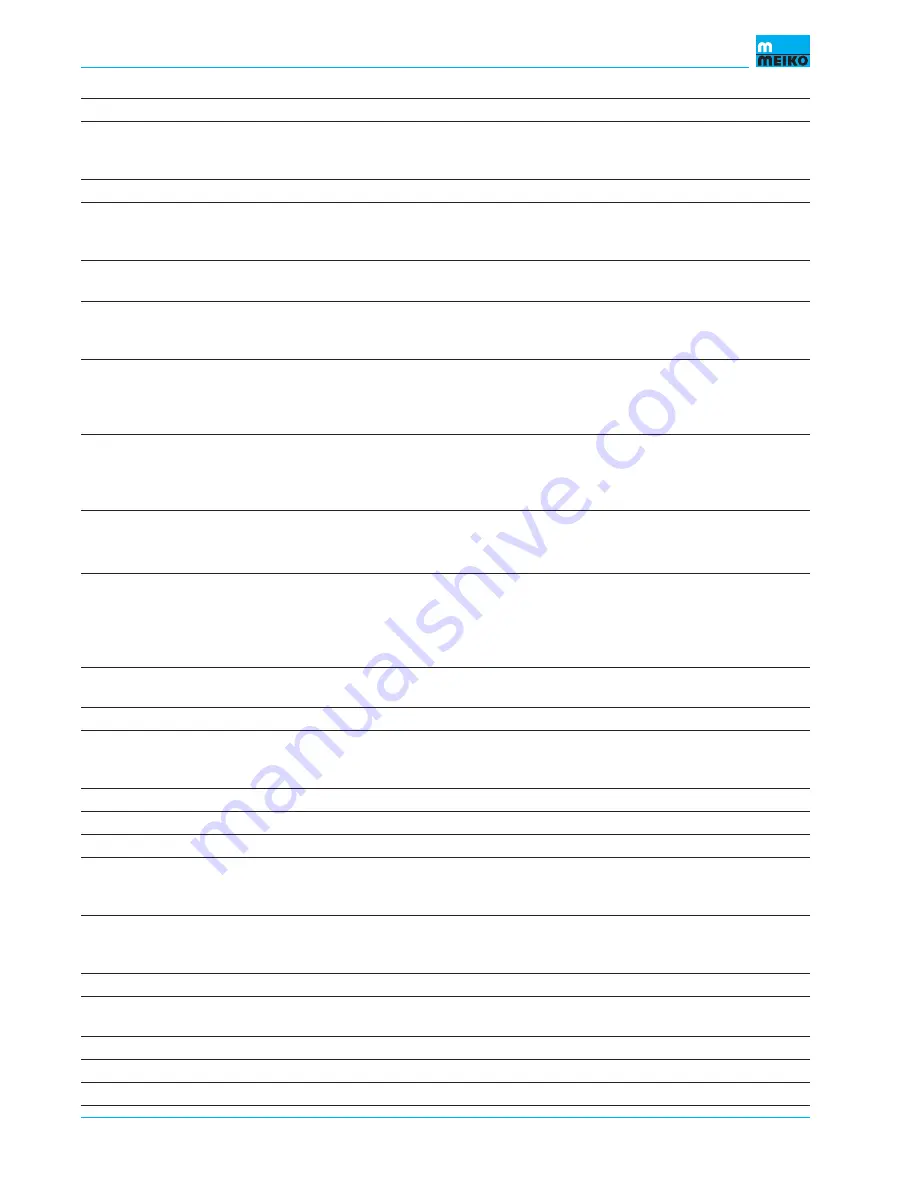
Page 14
#
Message (in display)
Problem
Action
111
Water loss in wash tank
•
Clear the message (see above).
112
Daily water change, due to
The machine had not been drained
•
At the end of the day, always shut down the
wash tank being full for too
in some time, and automatically
machine using the automatic drain/shutdown cycle.
long.
activated a drain/shutdown cycle.
113
Wash tank water level too high.
114
Pump intake screen missing
The scrap screen, M-iQ Filter and/
•
Check for correct installation of the components.
or inserted incorrectly.
or pump filter are not present, or
See Section 5.1,
Daily Cleaning
.
have been reinstalled incorrectly.
115
Wash tank overfill.
•
Clear the message (see above).
Drain pump activated.
116
Wash/rinse arms blocked/
One or both wash arms are not
•
Check for correct installation of the components.
missing.
present, or have been reinstalled
See Section 5.1,
Daily Cleaning
.
incorrectly.
117
Check top wash/rinse arm.
The upper wash arm is not present,
•
Check for correct installation of the components.
was reinstalled incorrectly, or water
See Section 5.1,
Daily Cleaning
.
is not flowing through it properly.
•
Check that the pump filter is not clogged. See
Section 5.1,
Daily Cleaning
.
118
Check bottom wash/rinse arm. The lower wash arm is not present,
•
Check for correct installation of the components.
was reinstalled incorrectly, or water
See Section 5.1,
Daily Cleaning
.
is not flowing through it properly.
•
Check that the pump filter is not clogged. See
Section 5.1,
Daily Cleaning
.
200
Booster tank level during fill
Water supply to machine is not
•
Check that the water shutoff valve to the machine is
not reached early enough
flowing properly
open.
•
Check that the Y-strainer/dirt trap is not clogged.
205
Final rinse level low. Check
Water may be accumulating in ware,
•
Check that hollow items are loaded properly and
for inverted ware.
or failing to drain out of the machine
do not retain water. See Section 4.3,
Loading
properly.
Guidelines.
•
Check that the pump filter is not clogged. See
Section 5.1,
Daily Cleaning
.
206
Wash time extended. Final
•
Clear the message (see above).
rinse temperature too low.
211
Final rinse booster water loss
•
Clear the message (see above).
212
Forced draindue to booster
The machine had not been drained
•
At the end of the day, always shut down the
tank being full for too long.
in some time, and automatically
machine using the automatic drain/shutdown cycle.
activated a drain/shutdow n cycle.
301
Low rinse aid.
Rinse aid dispenser is low or empty.
•
Refill rinse aid (and prime if necessary).
311
Low detergent.
Detergent dispenser is low or empty.
•
Refill detergent (and prime if necessary).
961
Real time clock error.
•
Clear the message (see above).
962
Ethernet access fault.
Loss of Ethernet connectivity
•
If a LAN connection is used with the machine, and
is necessary, check the connection and restart
the machine.
964
USB access fault.
Loss of USB connectivity
•
If a LAN connection is used with the machine, and
is necessary, check the connection and restart
the machine.
965
Audio-Codec access fault.
•
Clear the message (see above).
967
Emergency factory parameters
•
Clear the message (see above).
reset
968
Display communication fault.
•
Clear the message (see above).
969
Low battery
.
•
Clear the message (see above).
972
Language memory fault.
•
Clear the message (see above).
S
ECTION
6 - T
ROUBLESHOOTING