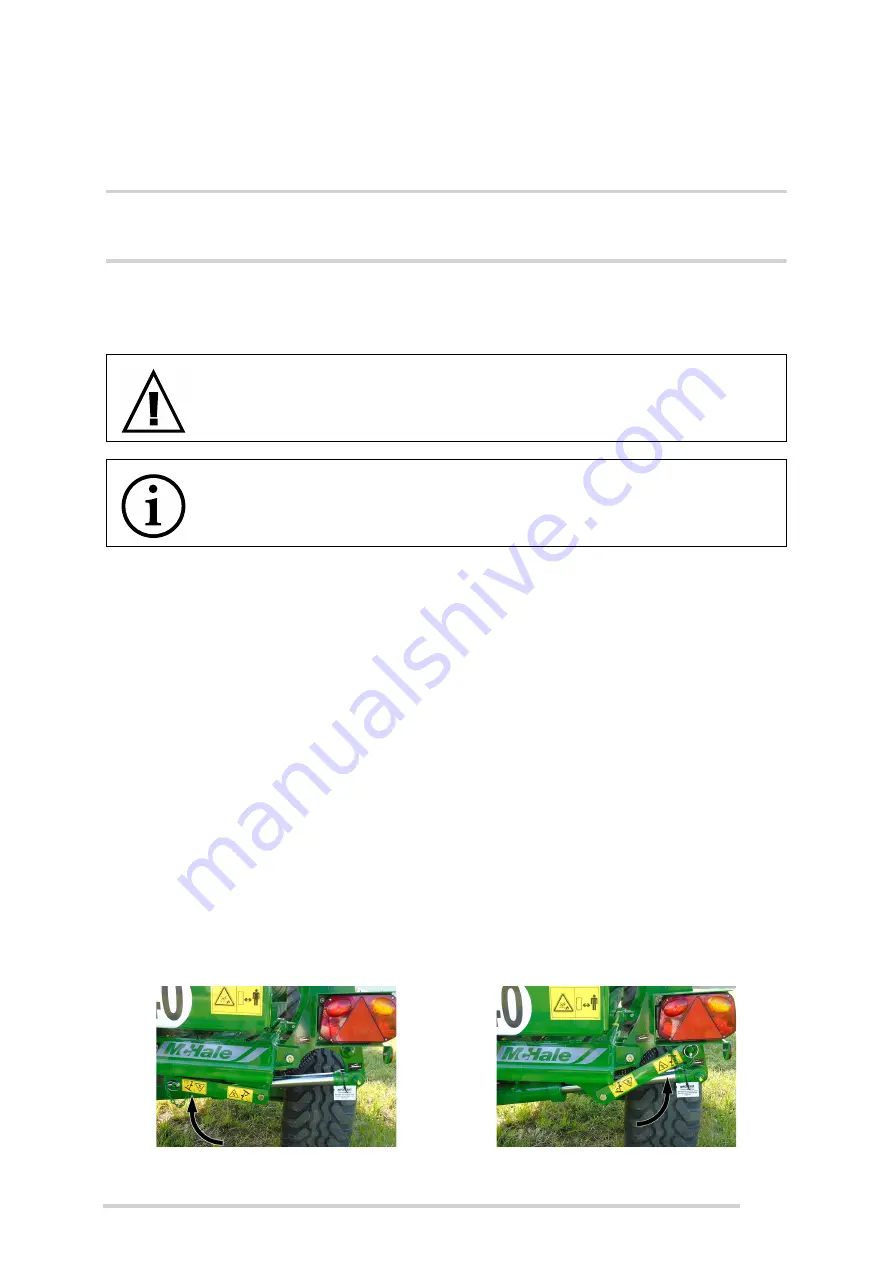
McHale
991 High Speed
Round Bale Wrapper
57
9
Road traffic safety & operation
9.1 Before travelling on any public roadway
The following must be checked, as a minimum requirement, before moving the
machine on a public road.
1.
Bale lift arm must be in the fully raised position. The transport lock must be in
the locked position while travelling on the road.
2.
The hydraulic supply must be turned off and protected from accidental
activation by disconnecting the hydraulic feed line. Support all loose lines in a
safe manner.
3.
Ensure the lights are connected and working correctly. The bale damper must
be raised to comply with lighting regulations.
4.
Ensure the electronic control box is switched off.
5.
If plastic film is to be transported on the machine it must only be done so on the
holders provided and secured, if necessary.
6.
Ensure that the knife guard is closed on the cut and hold, to prevent injury.
7.
Ensure that the tyres are set to the correct pressure as per safety decal and
according to the specifications.
(See ‘General specifications’)
8.
Attention must be paid to the maximum travel speed-limit of 40 km/h.
9.
Ensure that all the national road traffic regulations relating to the country are
fulfilled i.e. the use of safety chains may be mandatory in certain countries.
WARNING: Complete a full inspection before travelling on the road
Ensure that a full inspection is completed every time before attempting
to go on to a public roadway, always think and practice safety!
NOTE: Check lighting system before travelling on the road
Before travelling on a public road, the operator must ensure that the complete
(tractor and machine) lighting system is in a fully functioning condition.
Transport lock, unlocked
Transport lock in the locked position