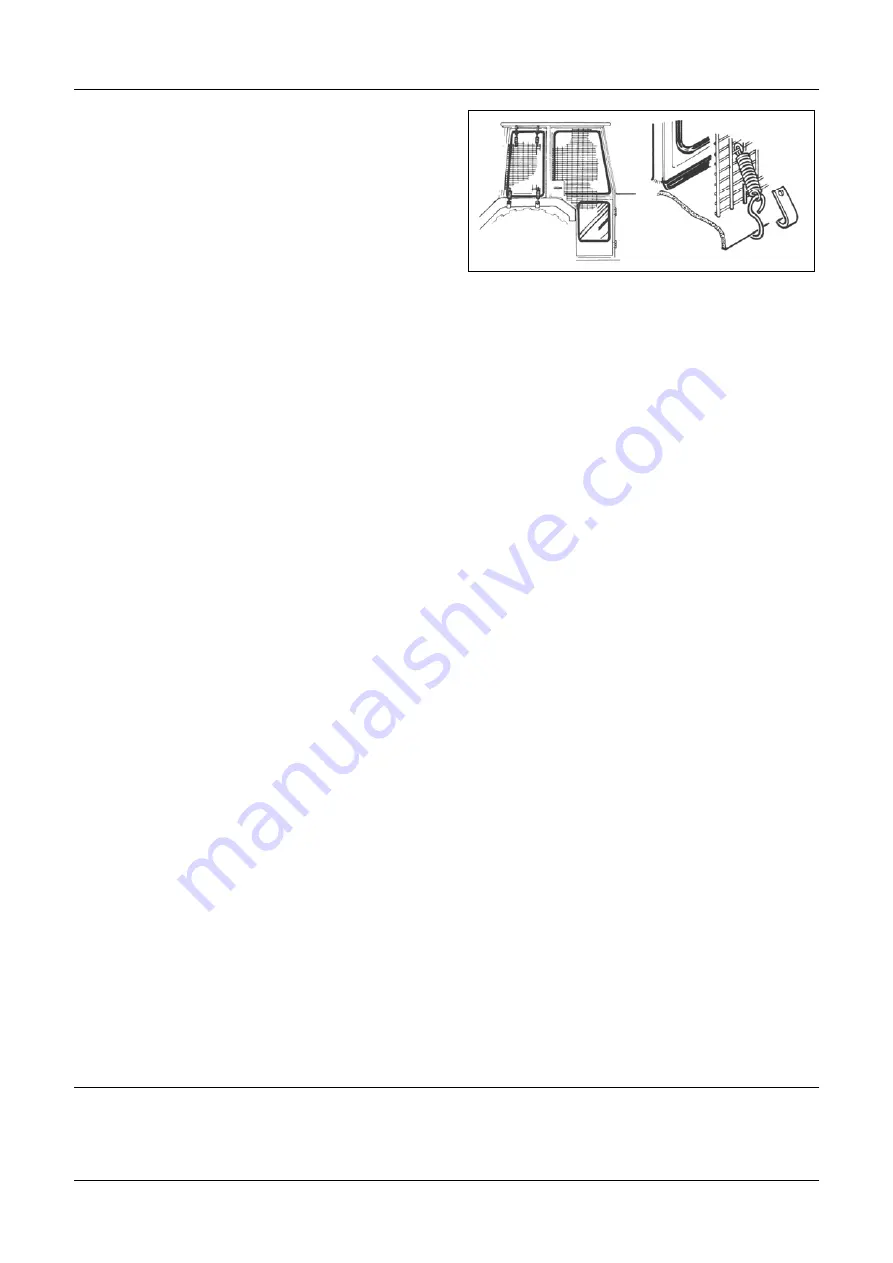
8
VEHICLE / TRACTOR PREPARATION
We recommend vehicles are fitted with cabs
using ‘safety glass’ windows and protective
guarding when used with our machines.
Fit Operator Guard (Part No. 7313324) using
the hooks provided. Shape the mesh to cover
all vulnerable areas. The driver must be
looking through mesh and/or polycarbonate
glazing when viewing the flail head in any
working position - unless the vehicle/ cab
manufacturer can demonstrate that the penetration resistance is equivalent to, or higher
than, that provided by mesh/polycarbonate glazing. If the tractor has a roll bar only, a frame
must be made to carry both mesh and polycarbonate glazing. The operator should also use
personal protective equipment to reduce the risk of serious injury such as; eye protection
(mesh visor to EN1731 or safety glasses to EN166), hearing protection to EN352, safety
helmet to EN297, gloves, filter mask and high visibility clothing.
Vehicle Ballast:
It is imperative when attaching ‘third-party’ equipment to a vehicle that the
maximum possible stability of the machine and vehicle combination is achieved – this can be
accomplished by the utilisation of ‘ballast’ in order to counter-balance the additional
equipment added.
Front weights
may be required for rear mounted machines to place 15% of total outfit
weight on the front axle for stable transport on the road and to reduce ‘crabbing’ due to the
drag of the cutting unit when working on the ground.
Rear weights
may be required to maintain a reasonable amount of rear axle load on the
opposite wheel from the arms when in work; for normal off-ground work i.e. hedge cutting
this should be 20% of rear axle weight or more for adequate control, and for ground work i.e.
verge mowing with experienced operators, this can be reduced to 10%.
All factors must be addressed in order to match the type and nature of the equipment added
to the circumstances under which it will be used – in the instance of Power Arm hedgecutters
it must be remembered that the machines centre of gravity during work will be constantly
moving and will differ from that during transport mode, therefore balance becomes critical.
Factors that affect stability:
Centre of gravity of the tractor/machine combination.
Geometric conditions, e.g. position of the cutting head and ballast.
Weight, track width and wheelbase of the tractor.
Acceleration, braking, turning and the relative position of the cutting head during these operations.
Ground conditions, e.g. slope, grip, load capability of the soil/surface.
Rigidity of implement mounting.
Suggestions to increase stability:
Increasing rear wheel track; a vehicle with a wider wheel track is more stable.
Ballasting the wheel; it is preferable to use external weights but liquid can be added to around 75%
of the tyre volume – water with anti-freeze or the heavier Calcium Chloride alternative can be used.
Addition of weights – care should be taken in selecting the location of the weights to ensure they are
added to a position that offers the greatest advantage.
Front axle locking (check with tractor manufacturer).
NOTE: The advice above is offered as a guide for stability only and is not a guide to vehicle strength. It is
recommended that you consult your vehicle manufacturer or local dealer to obtain specific advice on
this subject, additionally advice should be sought from a tyre specialist with regard to tyre pressures and
ratings suitable for the type and nature of the machine you intend to fit.