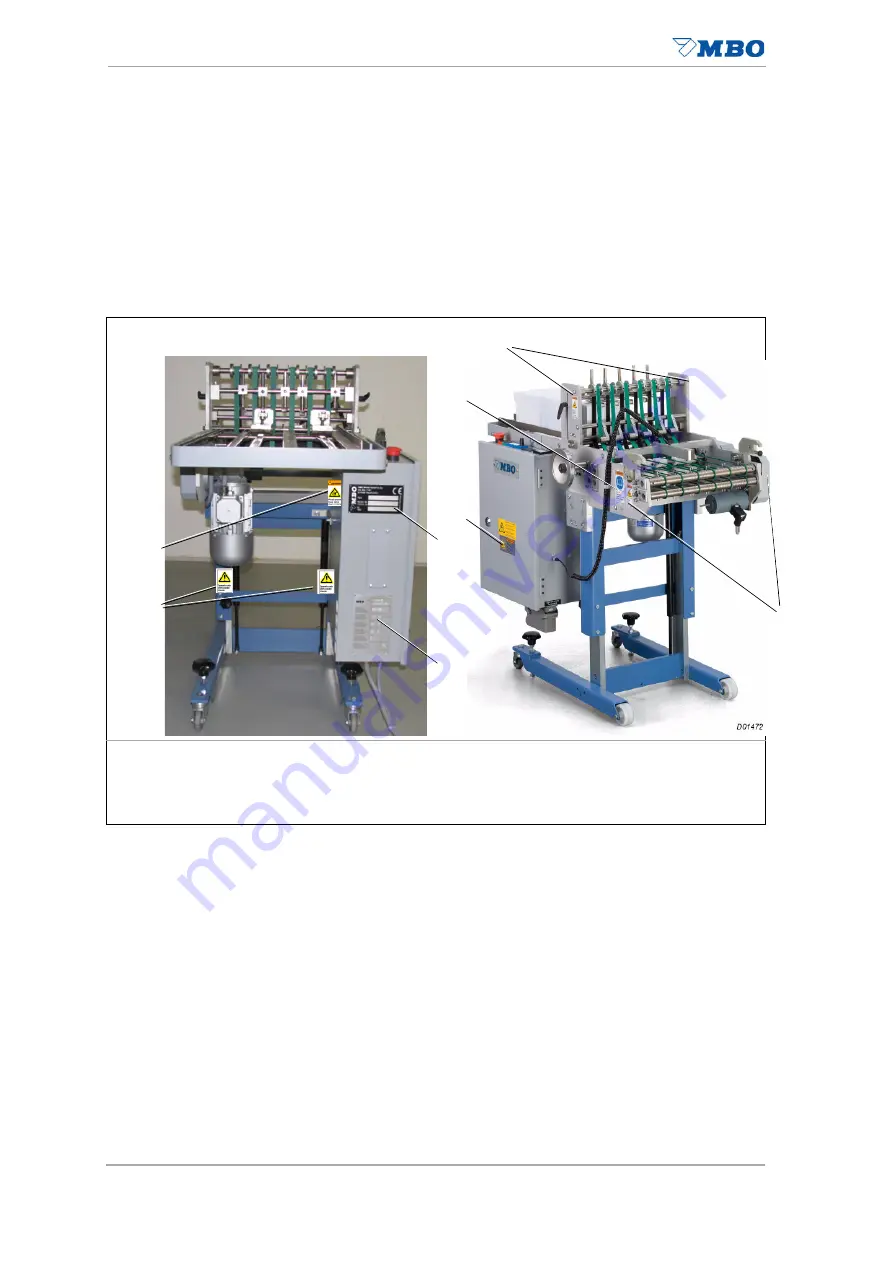
30
Delivery KAS 30ME MC-Control
Basic safety instructions
Markings on the machine
2.11
Markings on the machine
These markings must be on the machine and in an easily legible condition.
If the markings are damaged or illegible, they must be replaced.
For the corresponding MBO part number, please see the chapter “2.11.2
Position and meaning”.
2.11.1
Overview
1
Note <Drawing-in point>
2
Note <Drawing-in point>
3
Electrical type plate
4
Label
5
Note <Dangerous electrical voltage>
6
Note <Read operating manual>
7
Note < Clamping>
8
Note <Draw-in point>
Figure 3: Overview
5
1
6
2
4
3
8
7
Summary of Contents for Delivery KAS 30ME
Page 1: ...Delivery Translation of the original operating manual Keep for future use KAS 30ME MC Control...
Page 9: ...Delivery KAS 30ME MC Control 5 List of contents 10 2 Disposal recycling 88...
Page 10: ...6 Delivery KAS 30ME MC Control List of contents...
Page 50: ...46 Delivery KAS 30ME MC Control Operating and display elements operating modes Operating modes...