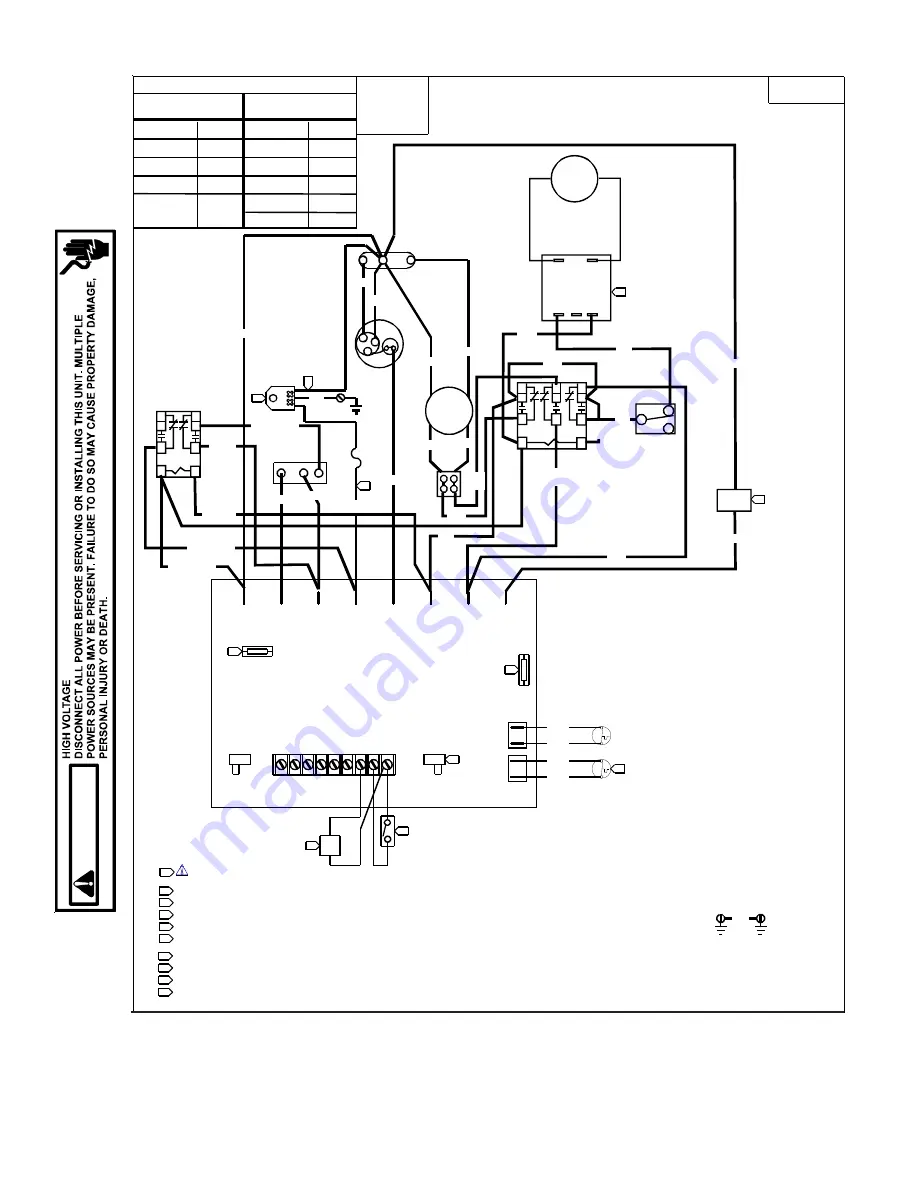
70
PTC and PTH
(Power Door - Two Stage Heat)
SCHEMATICS
Wiring is subject to change, always refer to the wiring diagram on the unit for the most up-to-date wiring.
WA
R
N
IN
G
R
C
S
RD13
YL10
F
C
H
BR35
BR34
RD33
RIBBED
WIRE
GN
2
RIBBED WIRE MUST BE CONNECTED AS SHOWN
NOTES:
WARNING: DISCONNECT POWER BEFORE SERVICING. WIRING
TO UNIT MUST BE PROPERLY POLARIZED (FOR 265V) AND GROUNDED.
REV
VALVE
SOLENOID
RD17
BK19
WIRING DIAGRAM
11179501
GN1
CONTROL
PANEL
CHASSIS
3
BR14
WH15
ON HEAT PUMP MODELS ONLY.
ON UNITS WITH REMOTE WALL MOUNTED TEMPERATURE SENSOR.
ON UNITS WITH FRONT DESK CONTROL SWITCH.
3
COMP
OD
FAN/COMP
CAP
REMOTE
TEMPERATURE
SENSOR
FRONT
DESK
SWITCH
4
HEAT PUMP W/AUXILLARY
ELECTRIC HEAT
CONNECT
R TO:
-----
G, Y/W1
G,B,Y/W1
G, W2
FUNCTION
OFF
COOL
1ST STAGE
HEAT
2ND STAGE
HEAT
COOLING UNIT
W/ELECTRIC HEAT
CONNECT
R TO:
G, Y/W1
G,B,Y/W1*
OR
G, W2
FUNCTION
COOL
1ST STAGE
ANTICIPATOR
CURRENT: .1
2ND STAGE
ANTICIPATOR
CURRENT: .2
ELECTRIC
HEATER
BK20
OFF
-----
5
REMOTE THERMOSTAT OPERATION
1
SWITCHOVER
FLOODBACK
PROTECTOR
FAN
MOTOR
LINE 1
INDOOR
SWITCH
OD TUBE
OUTDOOR
SWITCH
REMOTE/STANDARD
THERMOSTAT
CONTROL
ON OFF
MASTER
SWITCH
24 VAC
ID TUBE
24 VAC
C R G W2Y/
W1 B RS FD RC
HEATER HEATER LINE 2
COMP FAN HIGH FAN LOWR-VALVE
BK30
BK30
BK40
BK40
BK18
6
VT12
BK18 ON LINE 2 WITH FUSE SHOWN CONNECTED FOR 265V. FOR 230V, CONNECTB
POWER CORD TO LINE 2.
REMOVE FOR 265V APPLICATIONS.
REMOVE FOR NON-HEAT PUMP APPLICATIONS.
HEAT
8
7
9
FOR REMOTE OPERATION, SET SWITCH TO REMOTE POSITION
FUSE
1
2
3
4
5
6
7
8
9
10
IF SUPPLY VOLTAGE IS 208V MOVE 240V LEAD TO 208V TAP ON TRANSFORMER.
265V TRANSFORMER IS NOT SHOWN.
A
1
3
5
B
2
4
6
V T 1 9
2 S T G H T
V T 2 0
2 S T G H T
V T 1 8
2 STG HT
V T 1 7
2
S T G
H T
B R 3 6
2 S T G H T
A
1
3
5
B
2
4
6
7
8
9
TRANSFORMER
Line
240
208
CO
M
Lo
ad
POWER
VENT
MOTOR
2
3
1
BU2
(PV)
BK12
(PV)
BK11
(PV)
BK16
BK17
(PV)
BU4
(PV)
RD14
(PV)
BU15
(PV)
BU10
(PV)
WH8
(PV)
BU9
(PV)
ON/OFF
SWITCH
TERMINAL
BOARD
POWER VENT
RELAY
10
G
FAN
FAN
G