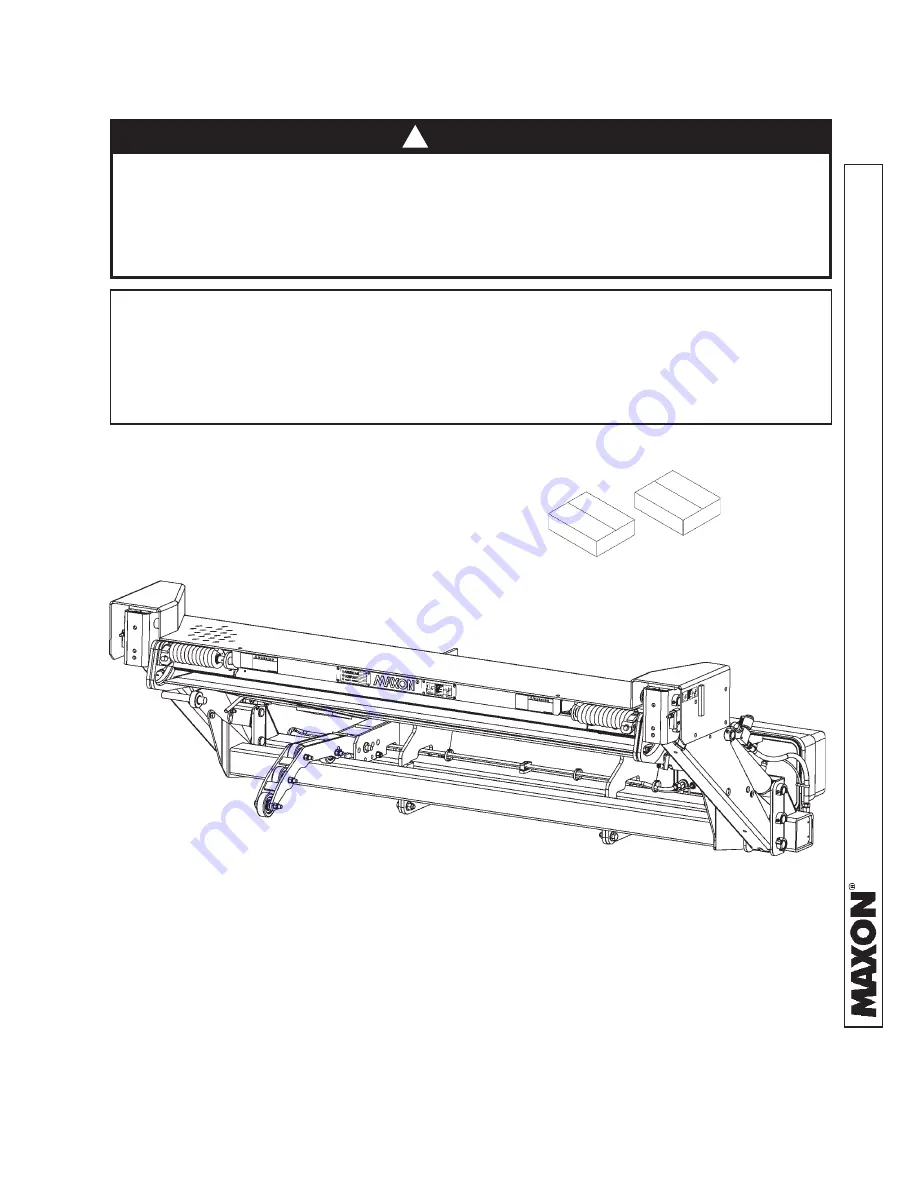
1
1921 Slauson
A
ve. Santa Fe Springs, CA. 90670 (800) 227-41
16 F
AX (888) 771-7713
6
GPTLR LIFTGATE COMPONENTS
NOTE:
Make sure you have all components and parts before you start installing Liftgate.
Compare parts in the part box and each kit box with packing list enclosed in each
box. If parts and components are missing or incorrect call:
Maxon Customer Service
Call (800) 227-4116 or
Send e-mail to [email protected]
GPTLR COMPONENTS
FIG. 6-1
LIFTGATE
!
CAUTION
Unpacking the Liftgate on unlevel surface may allow heavy components to slide
off when shipping bands are cut. Injury and equipment damage could result.
Before the shipping bands are cut, put Liftgate on level surface that will support
1500 lbs. When unpacking the Liftgate, remove heavy components carefully to
avoid injury and damage.
PARTS
BOXES
Summary of Contents for GPTLR-25
Page 90: ......