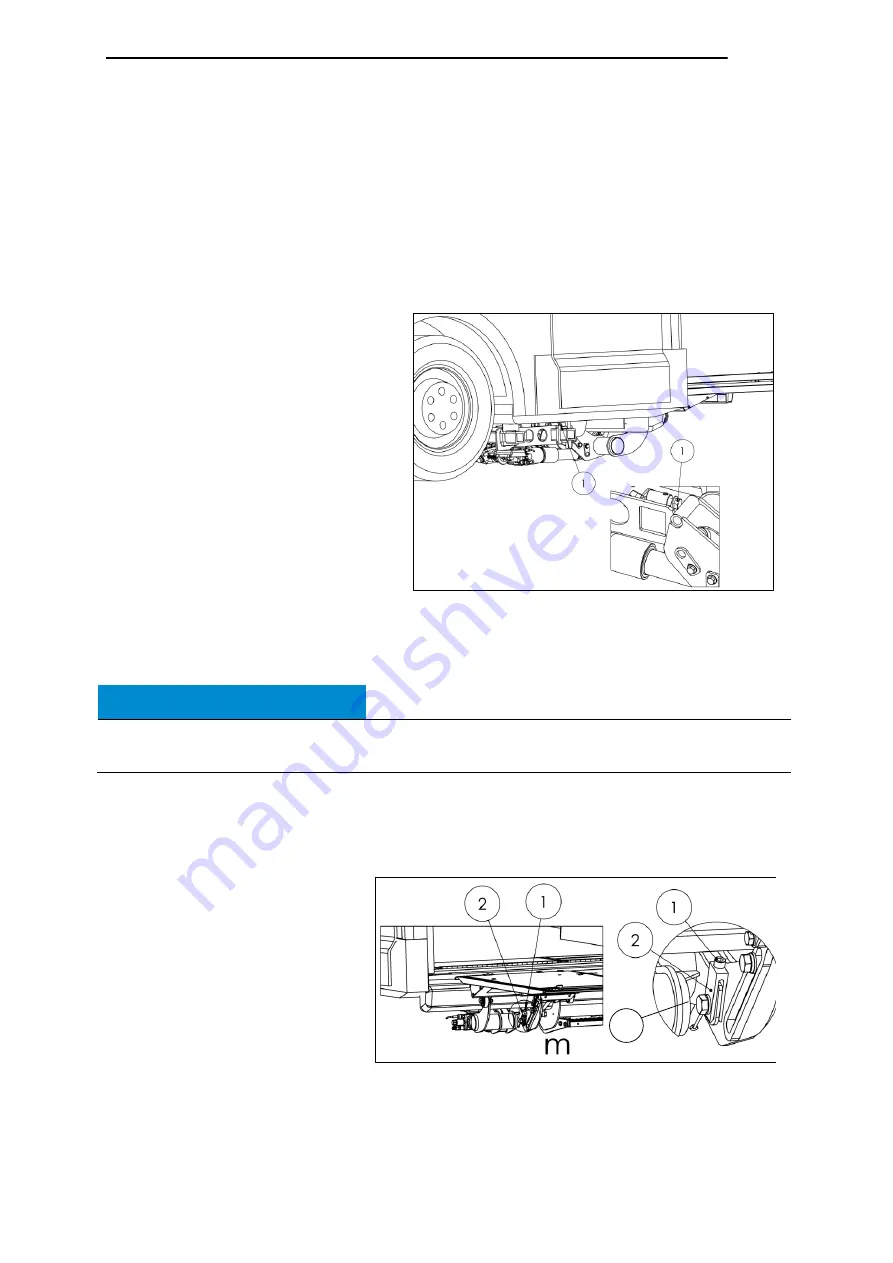
Adjusting the liftgate
49
5
Adjusting the liftgate
5.1 Setting the lift height to the vehicle floor level using the
adjustable stop on the axle assembly
Use the adjustment screw (1) pre-mounted on the axle assembly of the X1A
600F/GPC X1 and an appropriate tool (e.g. a ring wrench) to set the lifting gear to the
desired height with relation to the vehicle floor.
Use the adjustment screw (1)
to set the lift height
(see Fig. 74).
Rotate to left:
lower lift height
Rotate to right:
higher lift height
Legend:
Item 1
Adjustment screw
5.2
Aligning the platform parallel to the vehicle floor
To align the platform parallel to the vehicle floor, adjust the lifting gear using the
left-hand adjustment fork (adjustment screw accessible from above) (see
Fig. 75).
With the platform open,
operate the lifting gear
to the height of the
vehicle floor (not
against the stop).
Legend:
Item 1
Adjustment screw
Item 2
Adjustment fork
Item 3
Hex bolt
NOTICE
If no readjustment is necessary, make sure that the screws (1 and 3) are securely
tightened.
Fig. 74
Fig. 75
3
Summary of Contents for GPC X1-LDF
Page 1: ...GPC X1 LDF liftgate Installation Manual for Mercedes Benz Sprinter...
Page 11: ...Introduction 5 2 1 4 Accessories kit Fig 4...
Page 13: ...Introduction 7 2 1 5 Installation adapter kit 22 911 216 Fig 5...
Page 71: ...Useful information 65 8 2 Assembly drawings of installation adapters...
Page 72: ...Useful information 66 8 3 Electrical circuit diagram...
Page 73: ...Useful information 67 8 4 Hydraulic circuit diagram...