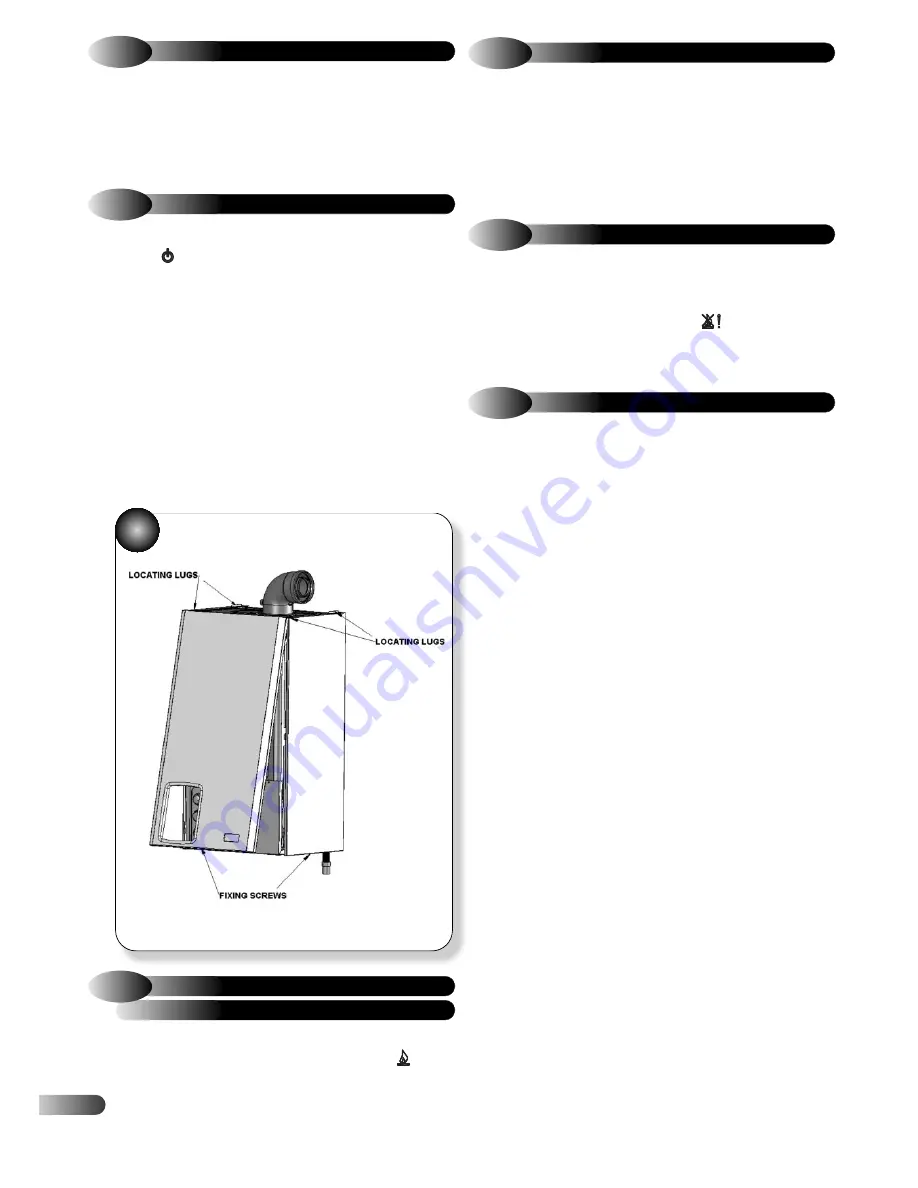
18
5.3
DHW FLOW RATE
Should the mains flow rate be consider
ed to be too high, a flow
regulator is available as a spare part which will limit the flow.
Refer to section 9.12.
The nominal pre-adjusted flow rate may vary by ± 5% due to
factory tolerances and mains water pressure fluctuation.
THE APPLIANCE
5.5
LOCKOUT INDICATION AND RESET
In the event of failur
e during an ignition sequence, (5 attempts),
the digital display displays error code ‘
4
’ and the er
ror light
will be lit. In order to reset, press the reset button (Fig. 19).
5.4
FINAL CHECKS
a)
T
urn both control knobs fully anti-clockwise to the standby
position .
b)
Remove the manometer and tighten the appliance inlet
pressure test point screw. Re-light the burner and test for gas
tightness.
c)
Fit the appliance casing as illustrated in Fig. 21. Fit the side
panels by hooking over at the top and securing with the screws at
the bottom. Fit the front panel in position using locating lugs at
the top and sides and screws underneath.
d)
Set the CH and DHW contr
ol knobs to the required
temperature setting. Ensure that the clock override switch is in the
timed position and check that the time clock is set at the desired
time periods. Set the room thermostat (if fitted) to the required
setting.
5.7
OVERHEAT PROTECTION
The appliance incorporates an over
heat thermostat, which
monitors the appliance’s operating temperature. Abnormal
temperatures will cause the appliance to go to lockout, the digital
display will show code ‘
1
’ and the er
ror light will be lit.
Allow the appliance to cool and press the reset button to clear
(Fig. 19).
5.8
OTHER FEATURES
The following additional featur
es are included in the appliance
specification:
ANTI-CYCLE DEVICE:
When the appliance cycles on its central heating contr
ol
thermostat, a slow cycle device operates. The timer (set to 3
mins) is activated after the end of each burn cycle to prevent
rapid cycling of the burner.
ANTI PUMP SEIZURE DEVICE:
Pr
oviding that a power supply is maintained and the appliance
ON/OFF switch is ON, the pump will operate for at least 20
seconds every 24 hours (regardless of heat demand) to prevent
pump seizure during periods where the appliance is not used.
W
ATER FLOW SWITCH:
This device pr
events the burner from firing if there is inadequate
water flow through the main heat exchanger.
DHW PRE-HEA
T: (ECO light OFF)
DHW
Comfor
t (Pre-heat)
selected: W
ith no demand for
DHW the boiler will fire periodically for a few seconds to
maintain the DHW plate heat exchanger in a heated condition.
This feature will automatically adjust to the user’s habitual
requirements. Thus during long periods of no DHW draw-off,
e.g. overnight, no pre-heat is provided. DHW
Economy
selected: No pr
e-heat is provided.
(ECO light lit)
KEEP-HOT FACILITY:
This featur
e is designed to provide hot water very quickly without
wasting too much water. Therefore you may notice that after
EVERY hot water draw-off the burner may stay on for a short
period of a few seconds. This is to pre-heat the hot water circuit
and prepare the appliance for the next hot water draw-off.
SUMMER MODE:
T
o avoid resetting the control knob temperature to O in summer
when CH is not required, switch the clock override switch to the
OFF
position.
5.6
FROST PROTECTION
The appliance is fitted with a fr
ost protection device which
operates the boiler when the temperature is below 5°C. In the
event of very cold conditions, the pump may operate and the
appliance light for a few minutes to protect the appliance and
system from potential frost damage. This can only function if the
gas and electricity supplies are maintained and the appliance is
left ON. The time clock can be switched to the OFF setting.
21