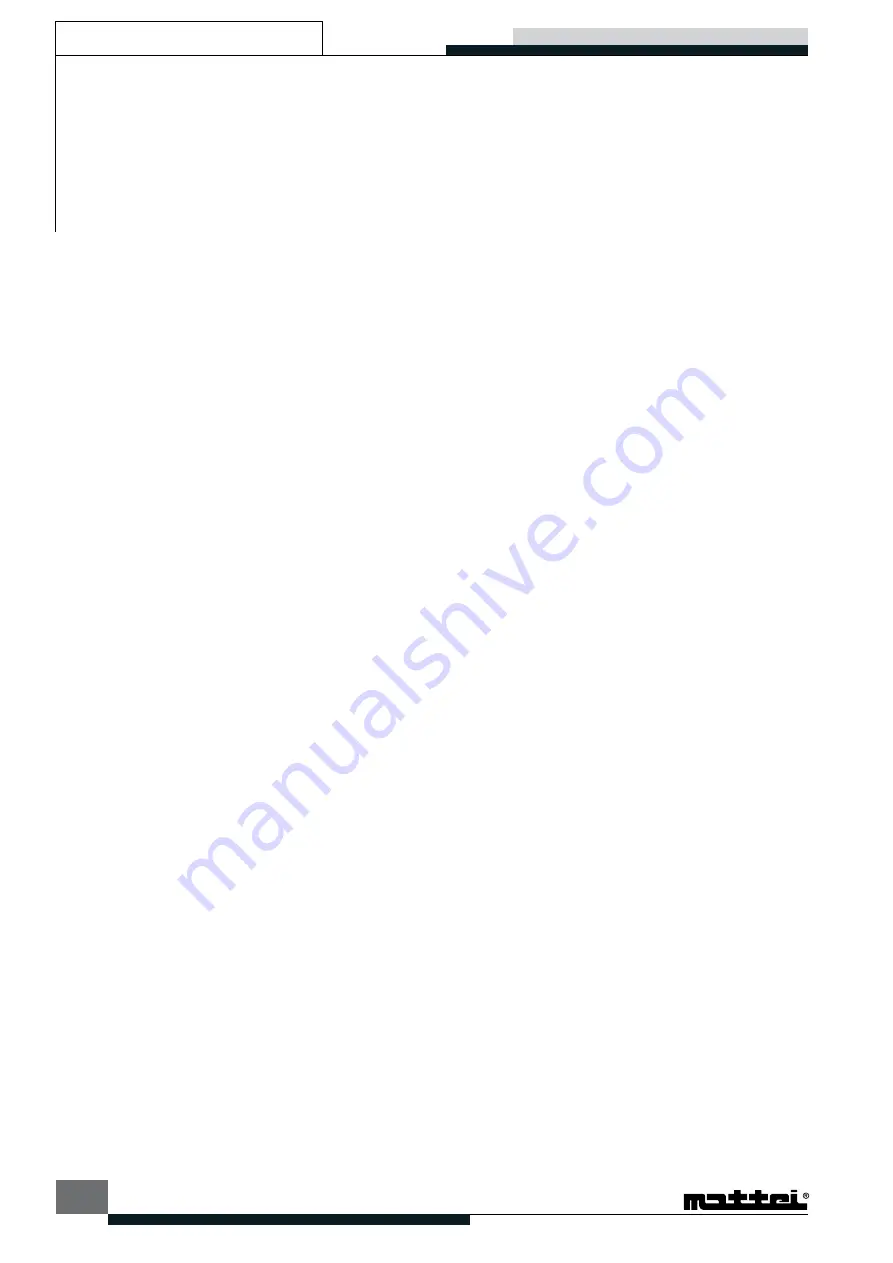
BLADE
1-7
TI215G0010
between the instructions given in this manual and those
set out by the law in force concerning safety, it is highly
recommended to apply the more restrictive ones.
Maintenance and repair
Only authorized staff is allow to carry out maintenance,
troubleshooting, and repairs. Any maintenance and
repair in progress should be indicated with a specific
sign stating the maintenance condition, and placed on
the control panel of the control unit until completion
of the operation even if temporarily interrupted. All
operations concerning its installation, maintenance or
replacement of components on either the machine or
the control unit should be performed with the system
turned off. Hence, the main switch should be on OFF
(OPEN) and blocked with the safety lock to prevent any
movement in the ON position.
For compressors equipped with INvERTER, before
performing any maintenance job, wait at least 5
minutes after you have disconnected the electricity
supply.
The staff in charge of maintenance, before intervening,
should first check that the following conditions exist:
– possible tanks under pressure have been discharged.
The staff in charge of maintenance, before intervening
on pneumatic or lubricating systems and specifically
on piping, tanks, hoses, and other components under
pressure should correctly reduce the inner pressure
value of the equipment to be investigated to the room
pressure value. Dysfunctional components should be
replaced with others with the same code. If, during
troubleshooting, it should be necessary to carry out the
interventions with the control unit and the machine
supplied, all precautions should be taken as required
by the safety standards to operate under dangerous
voltages and with moving parts. At the end of the
maintenance and troubleshooting interventions, all
disconnected safety devices must be reset. Maintenance,
repair, and troubleshooting should be completed with
the verification of the correct operation of the machine
and of all of its safety devices.
SETTING AT THE CUSTOMER’S EXpENSE
Except in the case of possible different contractual
agreements, the following items are normally at the
customer’s expense:
– room preparation (including building work such as
the laying of foundations or canalizations, if required,
etc.);
– anti-slip, leveled flooring;
– preparation of both the place of installation and
the machine installation itself whilst observing the
dimensions set out in the layout;
– preparation of auxiliary services appropriate to the
equipment requirements (such as electrical network,
pneumatic network, etc.);
– preparation of electrical equipment in compliance to
Directive CE;
– adequate lighting complying with standard EN
60204-1;
– any safety devices before and after the energy supply
lines (such as differential switches, ground systems,
safety valves, etc.) as may be required by the laws in
force in country of installation;
– ground equipment complying with standard CEI 64-
8.
INSTRUCTIONS ON HOw TO REqUEST
INTERvENTIONS
For any type of information on the use, the maintenance,
the installation etc. Ing. ENEA MATTEI S.p.A. is always
available to meet the Purchaser’s requests. However,
any enquiries be made in clear terms, with references to
this manual and always stating the data on the machine
id plate. For any communication with the service center,
always indicate the type of machine, its serial number,
and the year of manufacture, which help identify every
machine and, whenever possible, specify the nature of
the detected problem or the defect indicated by the
machine such as: of an electrical, mechanical kind or
in terms of work quality, while describing the problem
on a copy of the “FORM FOR TECHNICAL SERvICE
REqUEST” attached to this manual.
Contact our local service department closest to you or
the central Italian office.
INSTRUCTIONS ON HOw TO ORDER SpARE pARTS
The machine may over a period of time require the
replacement of those parts subject to wear. To this
purpose, the purchaser can order the parts to be
replaced. It is compulsory to always buy original spare
parts. To order spare parts always indicate with the
maximum accuracy the following:
– Type and model of machine
– Serial number
– Exact name of the part in question
– Code and/or reference (if available)
– Required quantity
To simplify and speed up the delivery of spare parts, it
is recommended to forward orders by filling in a copy
of the “FORM FOR SpARE pART REqUEST” attached
to this manual and forwarding it to Ing. ENEA MATTEI
S.p.A. or to the closest distributor.
Kits with components for preliminary maintenance
are available.
please apply to MATTEI for further details.
General information