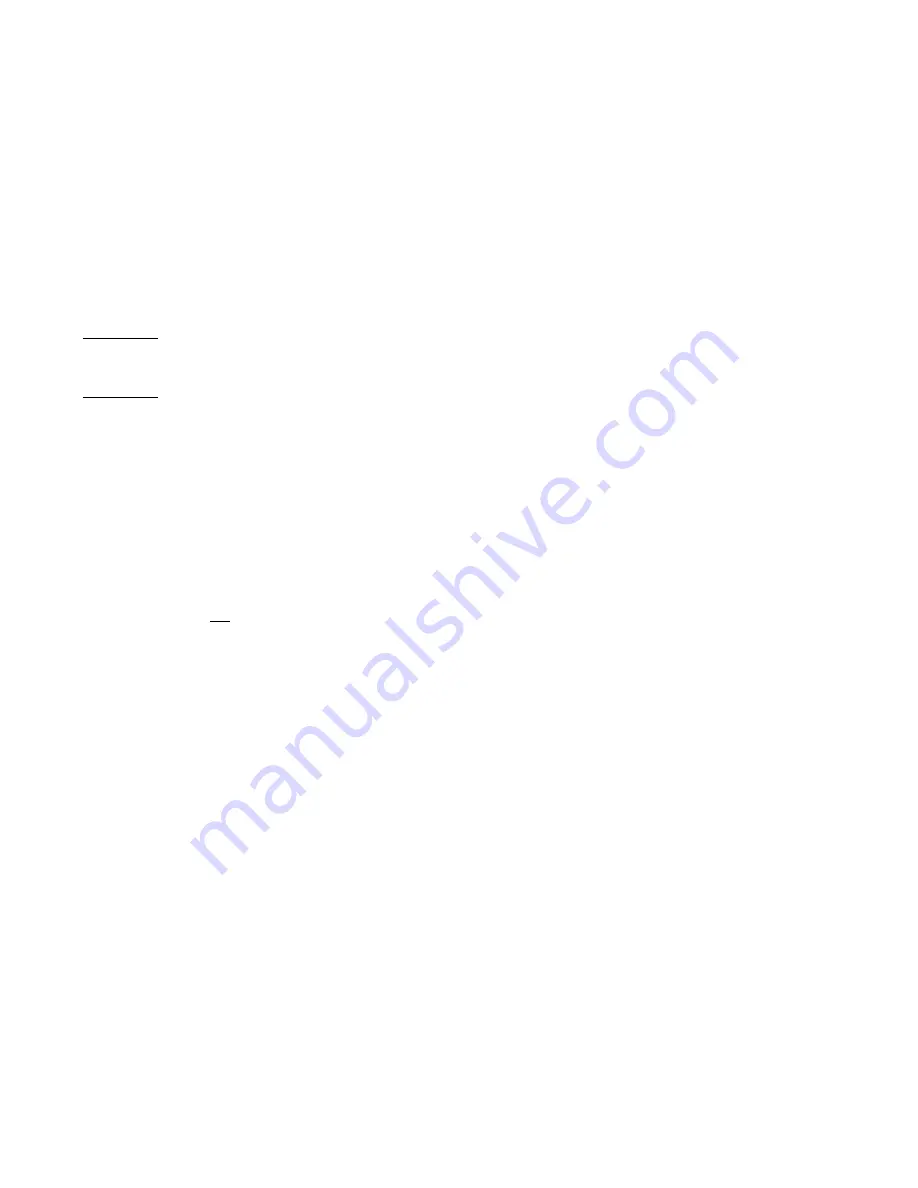
BROILER WARRANTY PROCEDURES
RETURN GOODS AUTHORIZATION FOR PARTS - FACTORY DIRECT
For prompt warranty parts replacement and RGA processing, please call Marshall's Customer Service
Department at 800-722-3474 or 704-525-6230 for assistance. In all cases, a Return Goods
Authorization (RGA) number must be issued by Marshall Air Systems, Inc. Unauthorized returns will
not be processed.
Option #1:
Purchaser to return part prepaid to Factory, Marshall to repair or replace at own
expense if defective, and ship part back to Purchaser prepaid.
Option
#2:
Marshall to furnish replacement part freight prepaid with or without requesting return of
the defective part.
WARRANTY LABOR REIMBURSEMENT AND/OR PARTS REPLACEMENT THROUGH
RECOGNIZED MAINTENANCE & REPAIR CENTERS
Normally, labor will be covered under the start up fee. In the unlikely event this does not apply, consult Marshall
Air Systems, Inc. To be reimbursed for warranty labor costs, authorization must be given by Marshall Air
Systems, Inc. Unauthorized work will not be reimbursed. Work must be performed by a Marshall Air Systems
Recognized Service Agency within the service time allowance guidelines and must be submitted along with failed
parts (if applicable) to Marshall Air Systems (freight prepaid) within 30 days of the work being performed. Travel is
covered, but must not exceed 50 miles or 1 hour, whichever is greater. Call Marshall's Service Department at
800-722-3474 or 704-525-6230 with any questions. Service is to be performed by recognized service agencies
during normal working hours. Owner to pay for all other charges including excessive travel or overtime charges.
DIAGNOSTIC LABOR CHARGES ARE INCLUDED IN SERVICE TIME ALLOWANCE GUIDELINES.
All
portable equipment (under 90 pounds) shall be delivered by Purchaser, at his/her expense, to the nearest
authorized service agency for in-shop repair or at purchaser's discretion he/she will pay all travel time and
mileage expenses for portable equipment.
NON-WARRANTY RETURNS:
All items returned for customer convenience are subject to a 20% restocking fee. In the event of an error by
Marshall Air Systems, Inc., a Returned Goods Authorization will be issued for full credit.
FOR INTERNATIONAL INSTALLATIONS -- PLEASE CONTACT YOUR
LOCAL MARSHALL AIR SYSTEMS RECOGNIZED DISTRIBUTOR.
PROCEDUR.BRL.DOC