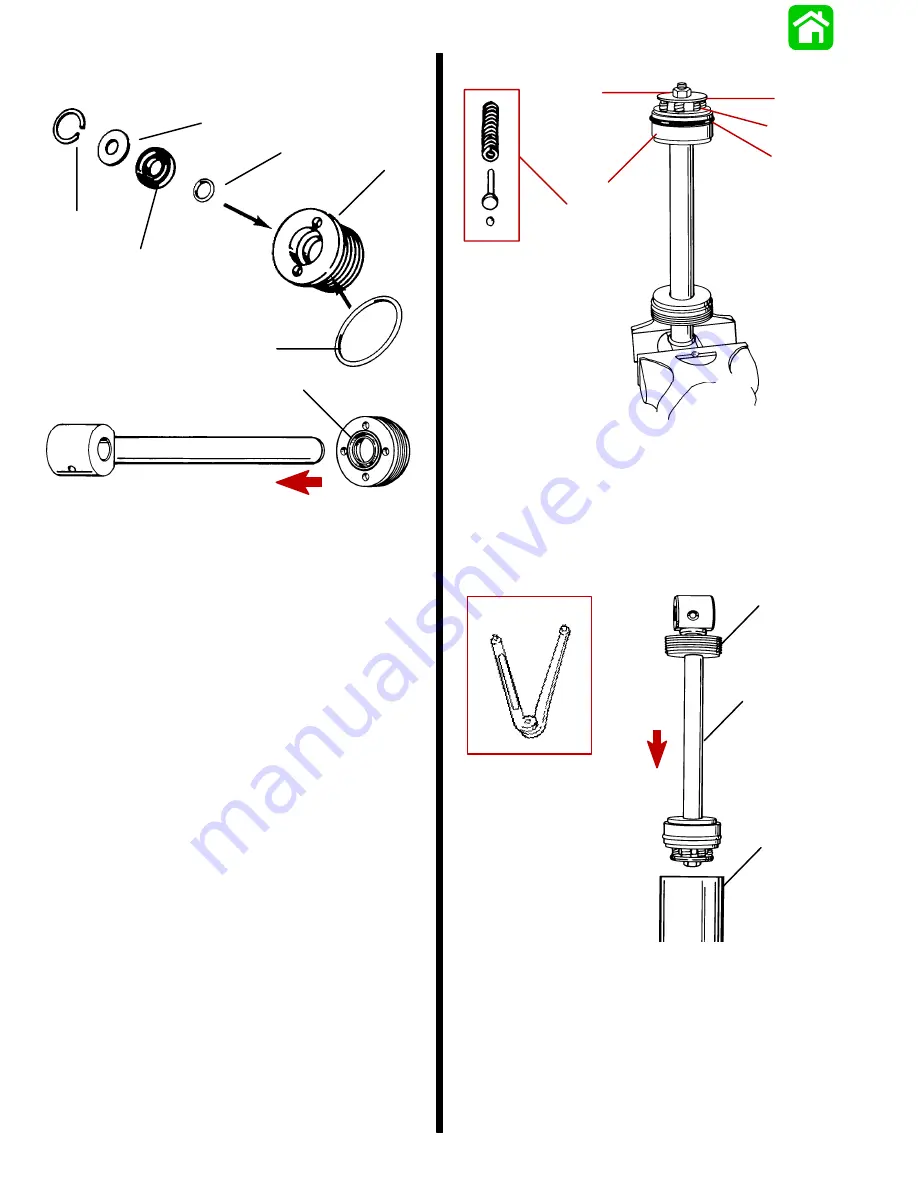
5B-26 - MID-SECTION
90-824052R3 JUNE 2002
3. Assemble end cap.
4. Install end cap.
51376
f
d
c
a
b
a
b
e
a - End Cap
b - O-ring (2)
c - Scraper seal
d - Washer
e - Retaining Ring
f - End Cap
5. Install components on rod.
51340
51363
e
a
d
c
b
c
a - Piston
b - O-ring
c - Check Valve Assembly (7)
d - Washer
e - Bolt or Locknut. (Tighten securely)
6. Clamp cylinder in a soft jawed vise and install tilt
rod assembly. Use spanner wrench and tighten
end cap securely.
51341
51337
91-74951
c
b
a
c
a - Cylinder
b - Tilt Rod Assembly
c - End Cap (Tighten Securely.) Use Spanner Wrench.
Summary of Contents for 105/140 JET
Page 5: ...1 A IMPORTANT INFORMATION SPECIFICATIONS...
Page 14: ...1 B IMPORTANT INFORMATION MAINTENANCE...
Page 25: ...C 1 IMPORTANT INFORMATION GENERAL INFORMATION...
Page 34: ...D 1 B A D C IMPORTANT INFORMATION OUTBOARD MOTOR INSTALLATION...
Page 50: ...A 2 ELECTRICAL IGNITION SYSTEM...
Page 79: ...2A 28 ELECTRICAL 90 824052R3 JUNE 2002 SPARK PLUG WIRE ROUTING HIGH PERFORMANCE OUTBOARDS...
Page 80: ...B 2 51797 ELECTRICAL BATTERY CHARGING SYSTEM AND STARTING SYSTEM...
Page 101: ...C 2 ELECTRICAL TIMING SYNCHRONIZING ADJUSTING...
Page 117: ...D 2 ELECTRICAL WIRING...
Page 133: ...90 824052R3 JUNE 2002 ELECTRICAL 2D 15 Notes...
Page 149: ...A 3 FUEL SYSTEMS FUEL PUMP...
Page 159: ...B 3 54350 FUEL SYSTEMS CARBURETORS...
Page 161: ...90 824052R3 JUNE 2002 FUEL SYSTEMS 3B 1 Notes...
Page 206: ...C 3 FUEL SYSTEMS FUEL INJECTION SN 0G303045 AND BELOW...
Page 213: ...1 2 3 4 5 6 7 8 3C 6 FUEL SYSTEMS 90 824052R3 JUNE 2002 Fuel Management System...
Page 272: ...D 3 55173 FUEL SYSTEMS FUEL INJECTION SN 0G303046 AND ABOVE...
Page 344: ...E 3 FUEL SYSTEMS OIL INJECTION...
Page 370: ...4 51804 A POWERHEAD...
Page 418: ...90 824052R3 JUNE 2002 POWERHEAD 4A 47 Notes...
Page 429: ...4 51804 B POWERHEAD COOLING...
Page 434: ...4B 4 POWERHEAD 90 824052R3 JUNE 2002 Notes...
Page 436: ...90 824052R3 JUNE 2002 4B 6 POWERHEAD...
Page 441: ...A 5 MID SECTION CLAMP SWIVEL BRACKET AND DRIVESHAFT HOUSING...
Page 443: ...90 824052R3 JUNE 2002 MID SECTION 5A 1 Notes...
Page 457: ...B 5 MID SECTION POWER TRIM SQUARE MOTOR AND ROUND MOTOR DESIGN...
Page 495: ...A 6 LOWER UNIT E Z SHIFT GEAR HOUSING STANDARD ROTATION...
Page 554: ......
Page 555: ...B 6 LOWER UNIT COUNTER ROTATING LEFT HAND GEAR CASE...
Page 616: ...C 6 LOWER UNIT MERCURY XR6 MARINER MAGNUM III GEAR HOUSING...
Page 651: ...D 6 LOWER UNIT E Z SHIFT GEAR HOUSING NON RATCHETING STANDARD ROTATION STARTING S N 0G438000...
Page 657: ...90 824052R3 JUNE 2002 LOWER UNIT 6D 5 Notes...
Page 697: ...90 824052R3 JUNE 2002 LOWER UNIT 6E 5 Notes...
Page 740: ...6 F JET OUTBOARDS...
Page 742: ...90 824052R3 JUNE 2002 JET OUTBOARDS 6F 1 Notes...
Page 759: ...7 ATTACHMENTS CONTROL LINKAGE...