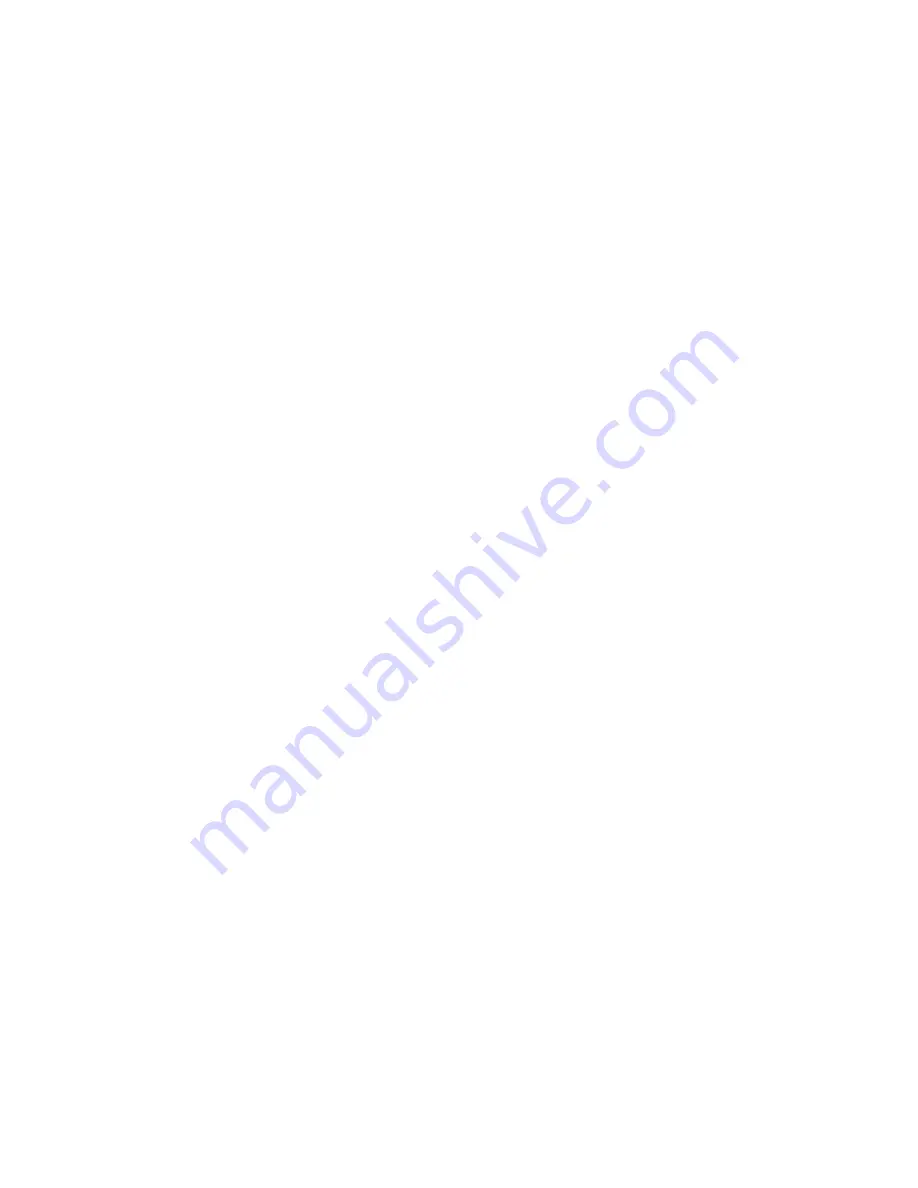
Operating and Technical Descriptions
- 12 -
8.8.
Motor Control (Scan Board)
The shutter motor blade completes one revolution for one frame of
video. The dc motor is locked in phase with the scanning beam by
comparing field drive (divided by two) with a pulse from a light sensor
and creating a feedback loop using a phase locked loop circuit.
When the operating mode is switched from chopped to panned the
phase locked loop is immobilised and the circuit seeks the point at
which the shutter blade obscures part of the sensor such that the
sensor output when smoothed is held at half its peak value, producing
zero voltage across the motor, thus holding the shutter in the fully open
position.
8.9.
Scans, HT and Auxiliary Supplies
Field Scan
A field ramp is generated by an operational integrator controlled by
field drive. This is converted to a
current ramp by sensing the voltage
across a resistor (R151) in series with the field coil. Field shift is
obtained by providing a dc offset across the field coil, a virtual earth
being established at pin 9 of connector P103.
Line Scan
A 10µs pulse is produced from the line blanking waveform. This is used
to switch a standard television choke-coupled line output stage. Since
the charge produced by the pedestal pulse has to be dispersed
uniformly with respect to the scanning beam, the line flyback has to be
linearised. The half sine wave voltage is truncated by coupling, using a
secondary winding, to the supply via a diode. The current waveform is
hence a linear sawtooth during flyback.
The shift control varies the dc bias through the scan coil.
A saturable reactor is connected in series with the line coil to improve
linearity.
HT Supplies
All HT voltages are derived from an overwind on the line scan
transformer.
8.10. Power Control
The main 8.7V camera supply is stabilised remotely in the voltage
stabiliser unit by amplifier V400 [V1] operating on the series transistor
Q402 [V1, Q3]. A foldback current limit circuit senses excess currents
in R406 [R22] to protect against surge and fault conditions. The battery
voltage level indicator senses the voltage across the series regulator
and varying numbers of illuminated LEDs show the battery condition.
Excess voltage is prevented from reaching the camera under fault
conditions by the protection circuit Q407 [Q2]. Battery life is extended
by a circuit V401 [V2] which detects a minimum voltage, greater than
the saturation voltage, across Q403 [Q3] and maintains this voltage by
reducing the reference voltage appearing on V400 pin 2 [V1]. Thus the
supply rail is maintained in regulation as it collapses.