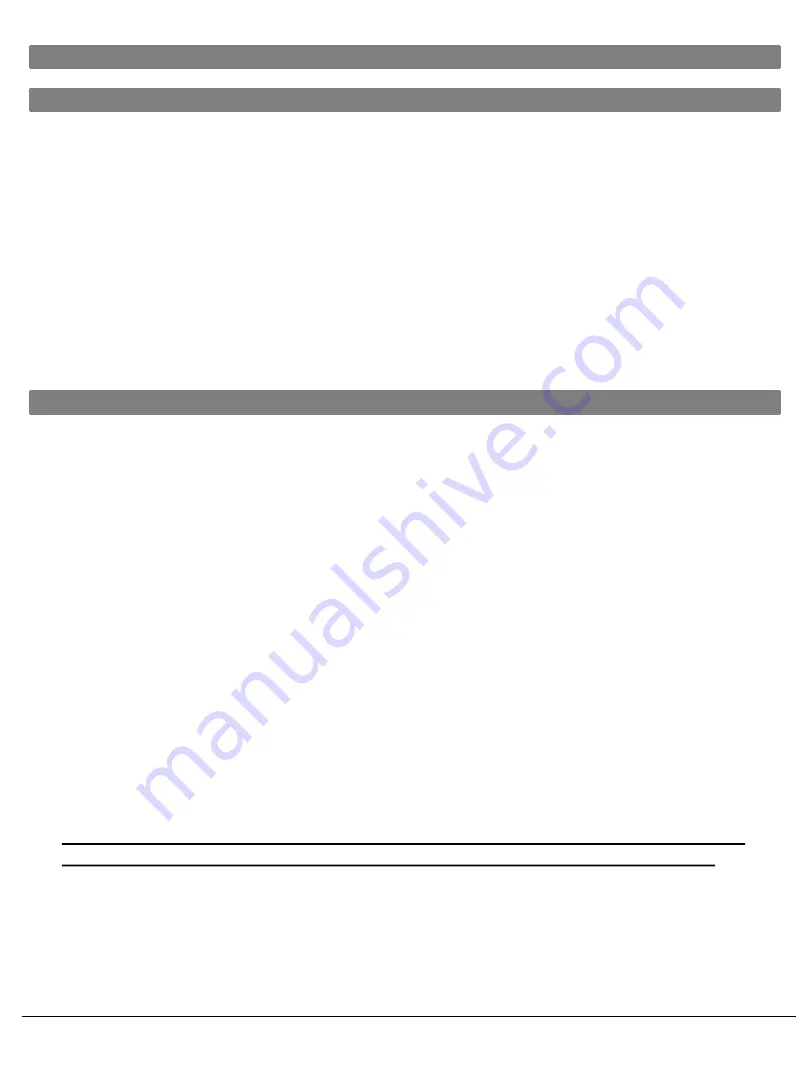
What is R290?
• Common name for high purity propane (C3H8) suitable for use in the refrigeration and air
conditioning industry.
• Hydrocarbon (HC) refrigerant.
• Proven safe, not an environmental threat – has been used in international markets for
10+ years.
• Already used in coolers, display cases, and chill cabinets.
Why not R134A?
• EPA and UE plans ban on R134A, effective between 2019 and 2022.
• Most beverage cooler manufacturers moving to R290 as the alternative to R134A
refrigerant.
5.3. R290 REFRIGERATING CIRCUIT:
FRIIA Service manual
Page 18
5.3.1. Overview:
5.3.2 Servicing R290 Equipment:
R290 Service Overview
• It is propane, so it is flammable. You MUST observe caution and proper safety practices
when servicing R290 refrigeration systems.
• Servicing refers to making repairs to the hermetically sealed system and any part of the
electrical system. The EPA and UE set a limit, 150 grams/ 5.29 ounces, on the amount of
R290 charge for commercial applications.
• Repair on R290 systems must always be done in a well ventilated area.
• Because R290 is highly flammable, a combustible gas leak detector is required when
servicing R290 systems.
Servicing R290 vs. R134A
• Operationally very similar systems.
• Operating pressure of R290 system slightly higher than an equivalent R134A system.
Example:
• At 38°C/100°F, evaporating pressure in an R290 system is approx. 46 psig/4,2 Bar.
• At 38°C/100°F, evaporating pressure in an R134A system is 26.6 psig/2.84 Bar.
• (See pressure chart in upper right column.).
• Refrigerant charge in an R290 system is 40 – 60% less than an equivalent R134A
system.
•
Only Marco technicians or service providers trained on procedures for handling
R290 refrigerant gas can carry out repairs on the chillers charged with R290.
Summary of Contents for FRIIA 1000860 Series
Page 33: ...8 WIRING DIAGRAM FRIIA Service manual Page 33...
Page 34: ...9 HYDRAULIC DIAGRAM FRIIA Service manual Page 34...
Page 35: ...FRIIA Service manual Page 35 Functional Hydraulic Schematic...
Page 37: ...11 2 Outer frame FRIIA Service manual Page 37...
Page 38: ...11 3 Top bracket FRIIA Service manual Page 38...
Page 39: ...11 4 Front electronic bracket FRIIA Service manual Page 39...
Page 40: ...11 5 Pump and Electrovalve brackets FRIIA Service manual Page 40...
Page 41: ...11 6 Base FRIIA Service manual Page 41...
Page 42: ...CABLES AND HARNESSES FRIIA Service manual Page 42 620 UK 115Vac 621 622 623...
Page 43: ...FRIIA Service manual Page 43...
Page 44: ...FRIIA Service manual Page 44...
Page 45: ...FRIIA Service manual Page 45...
Page 46: ...FRIIA Service manual Page 46...