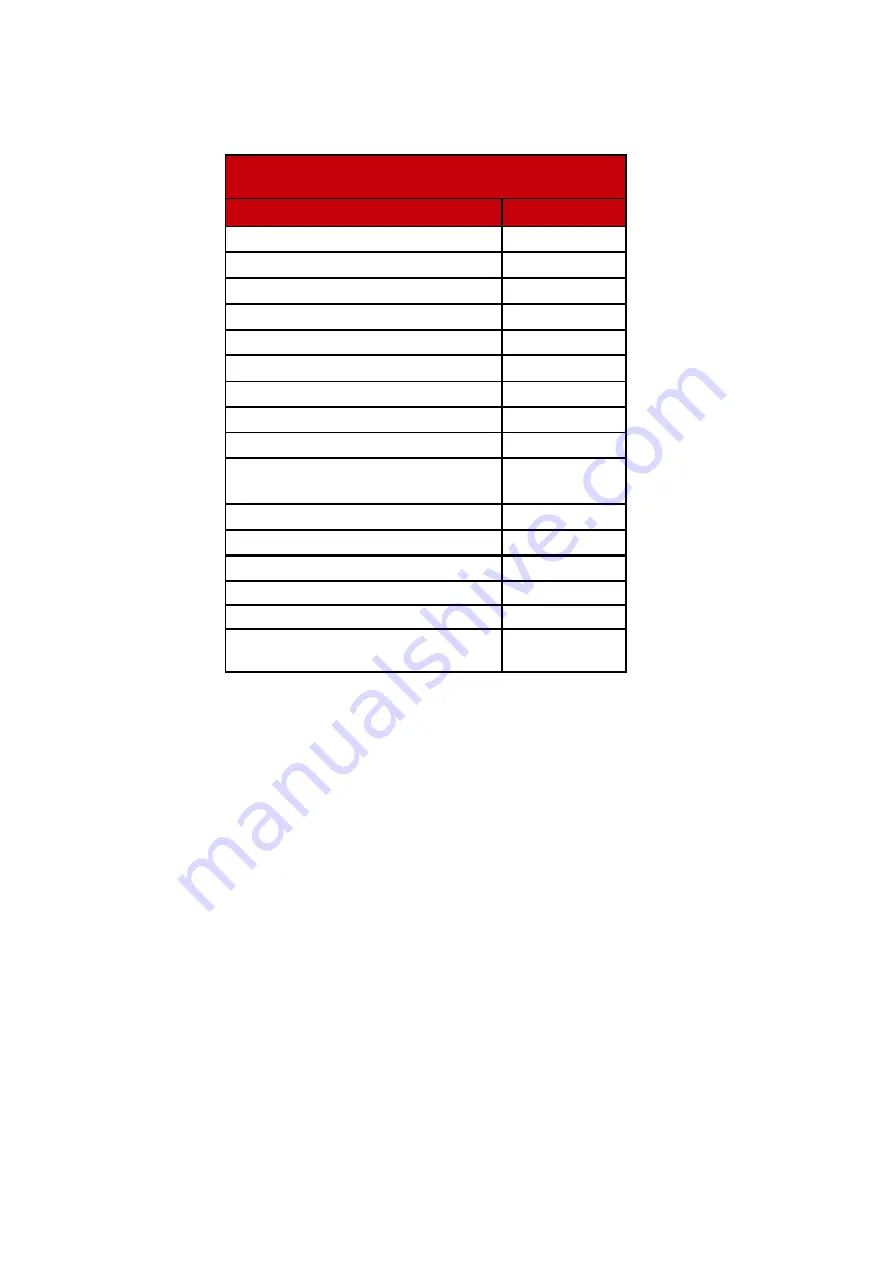
14
5.TECHNICAL SPECIFICATIONS
TECHNICAL SPECTS
Boiler Type
25 MKP
Capacity (kcal/h)
25000
Heat Power ( kW )
29
Weight ( kg )
245
Working Pressure ( bar )
3
Test Pressure ( bar )
4,5
Circulation Inlet-Outlet
1”
Security Inlet
1”
Security Outlet
1”
Filling - Draining
1/2”
Boiler Setting Range
(Min – Max) ( °C)
35/90
Boiler Water Volume ( lt )
46
Fuel Tank Volume ( kg)
210
Closed Expansion ( lt )
8
Voltage ( V / Hz )
230/50
Power Max. ( W )
700
Electricity Isolation Degree ( IP )
14A
Summary of Contents for 25MKP
Page 1: ...1...
Page 7: ...7 3 APPEARANCE OF THE BOILER AND EXTERNAL DIMENSIONS...
Page 11: ...11 4 2 BOILER INSTALLATION MOUNTING SCHEMA 1 1...
Page 16: ...16 When no setting is done the value shown at the screen is the boiler water temperature...
Page 19: ...19 USING SETTING RECOMMENDED BY THE FACTORY FAN LEVEL 3 LOADING 9 sec WAITING 29 sec...
Page 28: ...28...