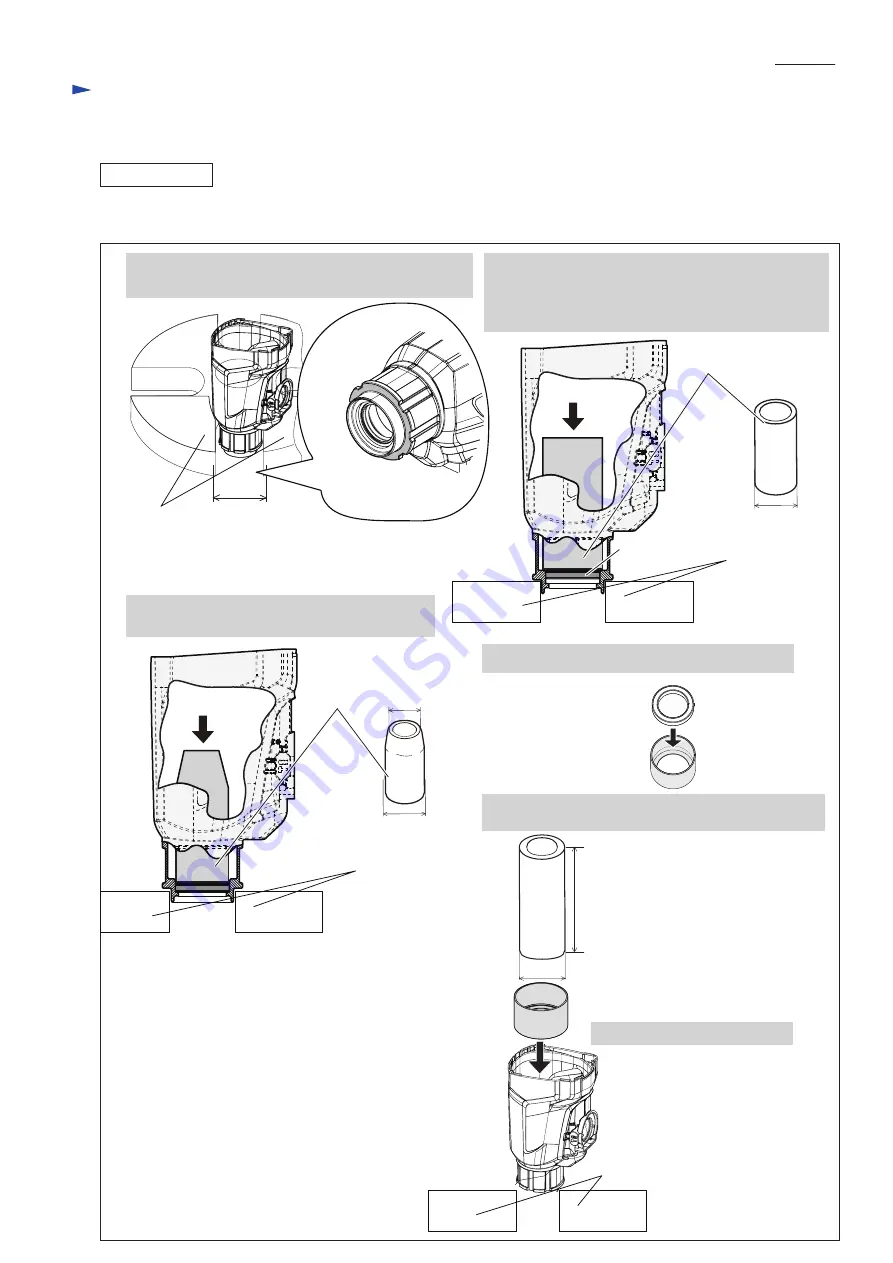
ASSEMBLING
Oil seal 25, Cup sleeve, Ball bearing 6806LLB can be assembled to Inner housing complete as drawn in
Fig. 33.
Fig. 33
40mm
[3] DISASSEMBLY/ASSEMBLY
[3]-7. The components for Gear housing complete (cont.)
P 21/ 25
R
epair
Ball bearing
6806LLU
Cup sleeve
4. Pressfit Ball bearing 6806LLU into Cup sleeve.
2. Pressfit Oil seal 25 carefully with 1R232 until it stops.
Oil seal 25 is not yet inserted completely because
the outer diameter of 1R232 is larger than that of
Oil seal setting hole.
1. Receive the stepped collar of Gear housing complete
on U shaped base of Arbor press.
3. Pressfit Oil seal 25 to the original position with
1R164 until it stops.
37mm
37mm
1R164
30mm
34mm
the stepped collar
(gray color portion)
to be put on 1R258
Gear housing
complete
Cup sleeve with Ball bearing 6806LLU
5. Pressfit Cup sleeve with Ball bearing 6806LLU into
Gear housing complete with 1R273.
Note
: Be careful to the direction.
1R273
100mm
1R232
36mm
Oil seal 25
U shaped base of
Arbor press
U shaped base of
Arbor press
U shaped base of Arbor press
U shaped base of
Arbor press