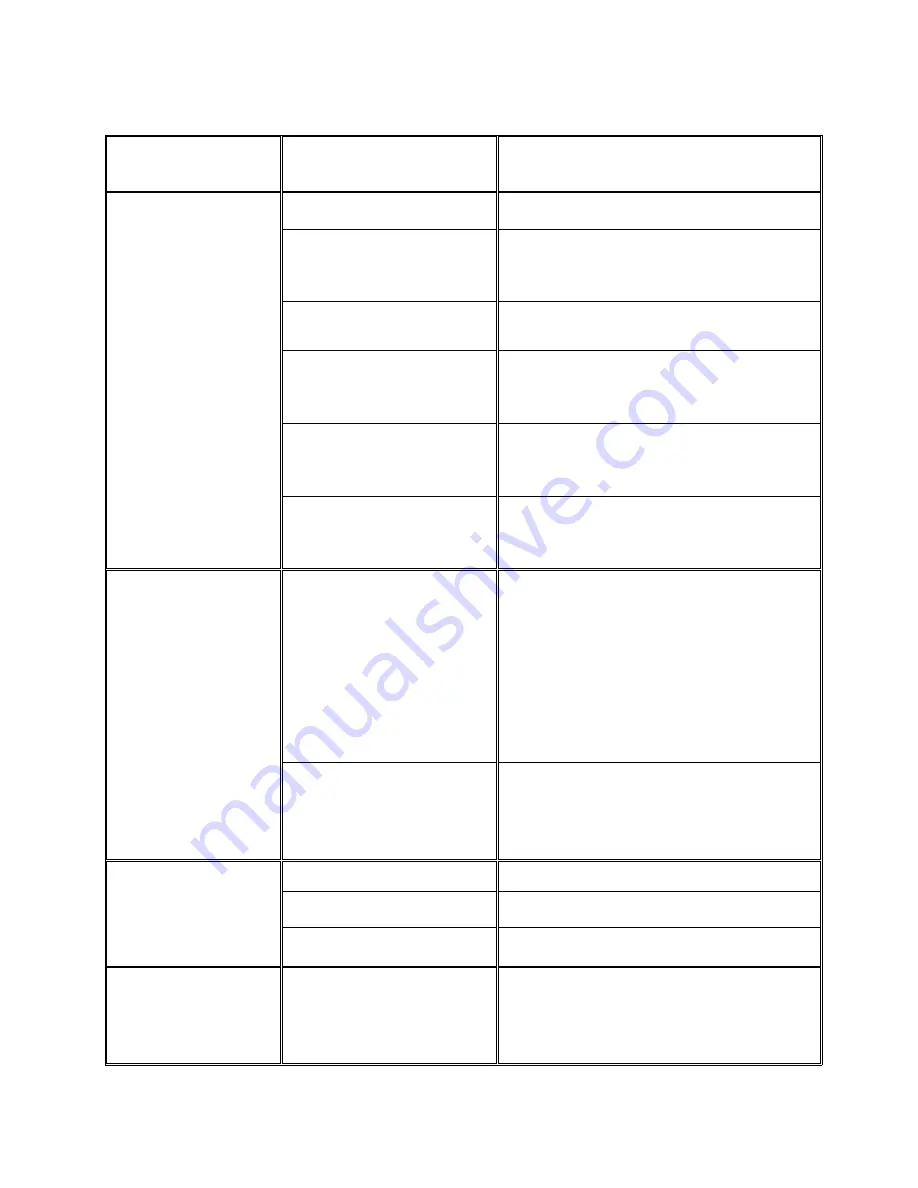
Flex 8EX EU System Instruction Manual
March 2012
35 of 37
C. Troubleshooting Tips
Problems Possible
Reasons
Suggestions
No response when
transmitter push
button is pressed
(Improper startup &
settings)
Transmitter low battery power
Check the transmitter battery level.
Emergency stop button
activated prior to startup
Prior to turning on the transmitter power switch
make sure that the red emergency stop button
is elevated.
Transmitter push button
functions locked
Initiate the Start command by rotating the
power key-switch to START position.
Incorrect system RF channel
Check and make sure that the transmitter
handset and receiver unit both have the same
channel.
Incorrect system serial
number/ID code
Check and make sure that the transmitter
handset and receiver unit both have the same
serial number/ID code.
System out of range
Make sure that the startup procedure is
initiated within 100 meters (300 feet) from the
receiver location.
No response when
transmitter push
button is pressed
(Damaged hardware)
Defective transmitting and
receiving module
Check the SQ display on the face of the
receiver unit. If it does not light up when the
push button is pressed then either the
transmitting or receiving module is defective.
First replace the transmitting module. If SQ
display is still not lit when the push button is
pressed then go ahead and replace the
receiving module.
Defective encoder
board or decoder module
If still no response, then replace the transmitter
encoder board. If still
doesn’t work then the decoder module
is defective.
No AC power to
the receiver
Incorrect input voltage
Make sure the source voltage is set correctly.
Blown fuse
Check for any blown fuse.
Incorrect wiring
Check input voltage connection.
Outputs do not
correspond to
transmitter
Incorrect output connection
Check the system wiring again. Please refer to
the output contact diagram inside this manual
or on the receiver cover.