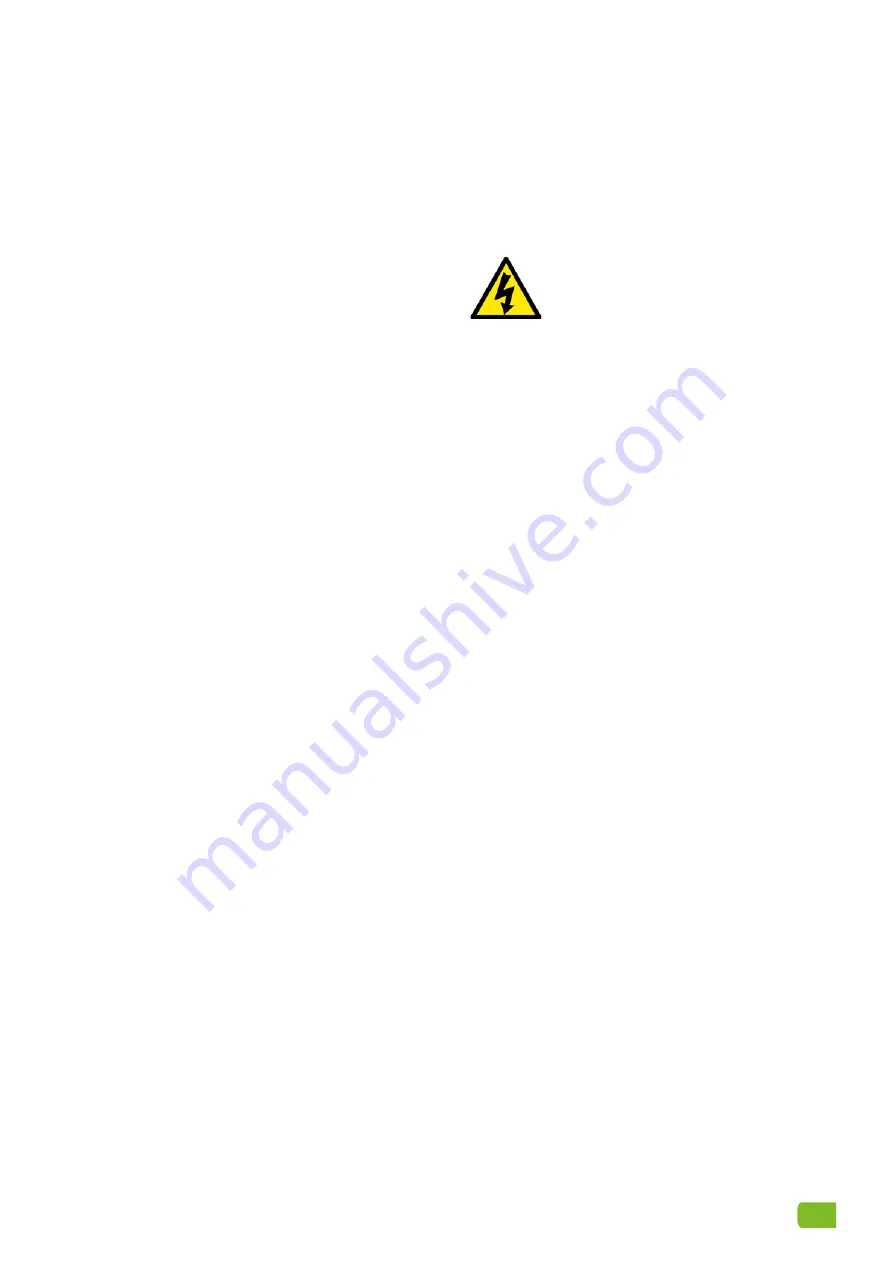
97 DEALING WITH FAULTS
Establish a secure state
If the control unit has detected a fault, operation is
stopped and the machine is set to a secure state. Some
failures or defects, however, cannot be detected by
the control unit, or it may not be possible to establish
a completely secure state.
If you detect a fault or a dangerous situation in the
machine, you must immediately:
• press the emergency stop button,
• turn off the main switch,
• if necessary, prevent it from being turned on again
• attach a warning sign to the machine.
Determine the cause
Depending of the version of the machine, detected
faults are displayed at the main control panel
• as text information (T-CODE option)
• with indicator lights
Read the description of the fault and the instructions
for troubleshooting in this manual. If necessary, contact
• trained personnel who are authorised to deal with
faults, or
• Magnaflux GmbH customer service
Current flow malfunction magnetisation/
demagnetisation
Description:
No current flow during the magnetising process; target
value of the magnetising current was not reached.
Consequence:
No magnetising of the workpiece; no cracks are visible.
Possible causes:
• Incorrect setting of the sleeve distance.
• Bad contact at the workpiece.
• Fault in the current regulation or power supply.
Possible solutions:
• Press the Push-button (current flow control) RESET.
• Check the sleeve distance and correct if
necessary.
• Clean contact points on the sleeves and on the
workpiece to bare metal.
• Check current regulation by repeating the
magnetisation process with an already-tested)
workpiece.
• Call Magnaflux GmbH customer service.
10. MAINTENANCE
Maintenance of your Universal SW includes all tech-
nical measures required to maintain the machine in
proper working condition, or to repair it, if necessary.
10.1 SAFETY INFORMATION
DANGER: High voltages can cause
lethal electric shock and burns.
Power terminals of the drive control-
lers can carry dangerous voltage for
up to 3 minutes after disconnection.
Work on the electrics must only be carried out:
• in compliance with the applicable standards in your
country.
• by a qualified electrician.
10.2 INSPECTION AND MAINTENANCE SCHEDULE
The tasks described here must be carried out regularly
at the intervals specified.
Interval: 8 hours
• Check the detection capability of the test liquid. If
necessary, empty the tank, clean it and refill with
new test liquid.
• Check the copper pads on the clamping heads (if
installed) and replace the pads if they are worn out.
Interval: 40 hours
• Clean the machine with a mild industrial cleaning
agent - no solvent, acids or alkalis.
• Check the magnetisation strength.
• Clean the magnetisation contacts with steel wool
until they are shiny and apply a thin layer of contact
grease.
• Check the intensity of your UV lighting.
• Visually inspect the condition of the filter in your
UV lamp and replace if damaged.
• Empty the compressed air/water separator on the
pneumatic maintenance unit.
• Fill the proportional oiler (if installed) with oil.
Interval: 160 hours
• Check the safety clutch on the magnetising coil
drive.
• Clean the guides of the coil and lubricate the drive
chain.
Interval: 400 hours
Disconnect the high current conducting cables. Clean
the contact points until they are shiny and apply a thin
layer of contact grease.
29