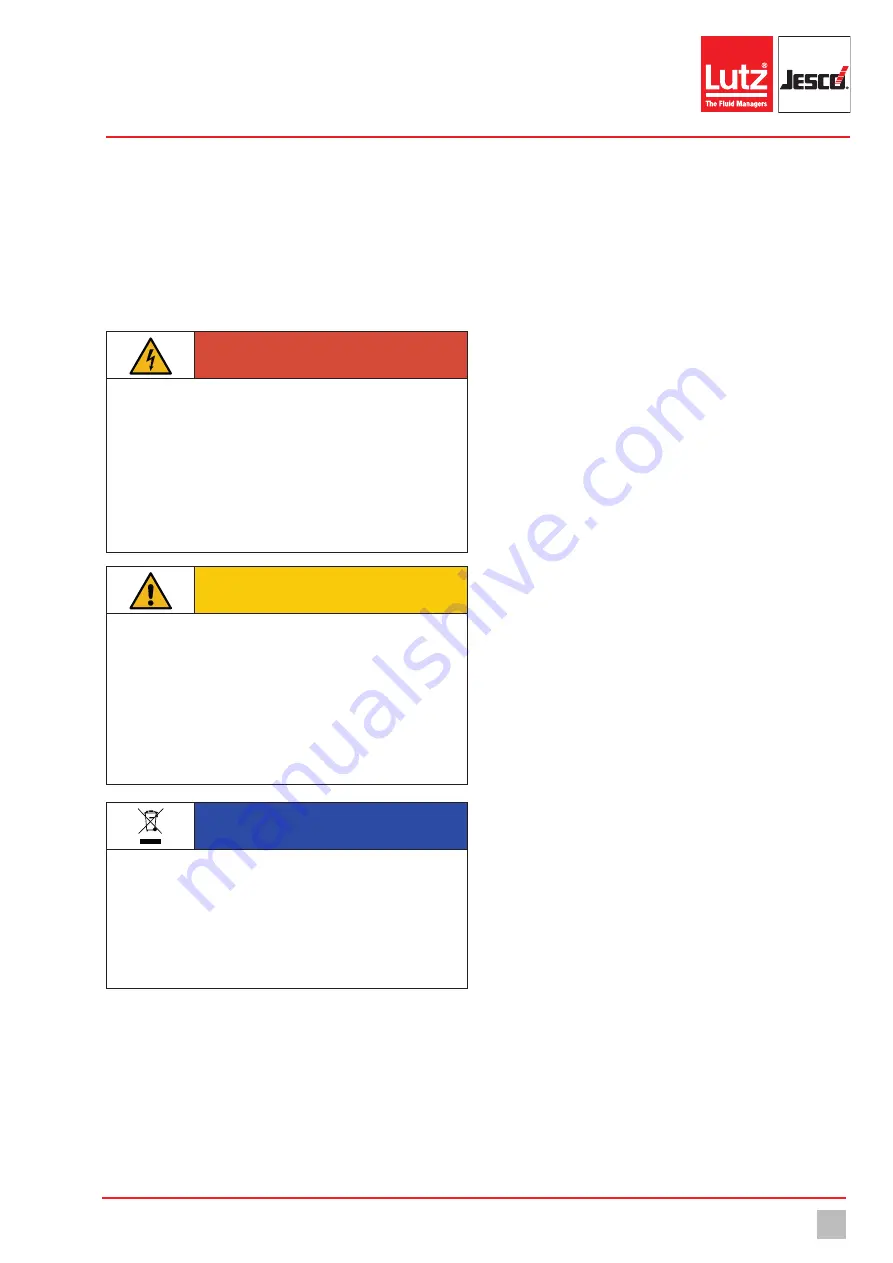
Safety
5
© Lutz-Jesco GmbH 2020
Subject to technical changes.
200123
BA-46020-02-V04
Multi-Channel Controller
TOPAX
®
MC
Operating instructions
2 Safety
2.1 General warnings
The following warnings are intended to help you eliminate the dangers
that can arise while handling the device. Risk prevention measures al-
ways apply regardless of any specific action.
Safety instructions warning against risks arising from specific activities
or situations can be found in the respective sub-chapters.
DANGER!
Mortal danger from electric shock!
Wrongly connected or located cables or damaged ones can injure you.
ð
Replace damaged cables without delay.
ð
Do not use extension cables.
ð
Do not bury cables.
ð
Secure cables to avoid being damaged by other equipment.
WARNING!
Increased risk of accidents due to insufficient qualifica-
tion of personnel!
The device may only be installed, operated and maintained by person-
nel with sufficient qualifications. Insufficient qualification will increase
the risk of accidents.
ð
Ensure that all action is taken only by personnel with sufficient and
corresponding qualifications.
ð
Prevent access to the system for unauthorised persons.
PLEASE NOTE
Do not dispose of the device in the domestic waste!
Do not dispose of electric devices via the domestic waste.
ð
The device and its packaging must be disposed of in accordance
with locally-valid laws and regulations.
ð
Dispose of different materials separately and ensure that they are
recycled.
2.2 Hazards due to non-compliance with the safety
instructions
Failure to follow the safety instructions may endanger not only persons,
but also the environment and the device.
The specific consequences can be:
n
Failure of major unit und system functions.
n
Failure of required maintenance and repair methods
n
Risk to persons when working on the device
n
Danger to the environment from overdosing
2.3 Working in a safety-conscious manner
Besides the safety instructions specified in this operating manual, further
safety rules may apply. Always observe all safety-related regulations and
guidelines applicable at the product's location of use. Note in particular
the following items:
n
safety regulations on handling electricity and live components,
n
safety regulations on handling hazardous substances,
n
accident prevention regulations
n
Safety and operating provisions,
n
Environmental protection provisions,
n
other applicable directives and laws.
2.4 Personnel qualification
Any personnel who work on the device must have appropriate special
knowledge and skills.
Anybody who works on the device must meet the conditions below:
n
Attendance at all the training courses offered by the owner,
n
Personal suitability for the respective activity,
n
sufficient qualification for the respective activity,
n
training in how to handle the device,
n
knowledge of safety equipment and the way this equipment functions,
n
knowledge of this operating manual, particularly of safety instructions
and sections relevant for the activity,
n
Knowledge of fundamental regulations regarding health and safety
and accident prevention.
All persons must generally have the following minimum qualification:
n
Training as specialists to carry out work on the device unsupervised,
n
sufficient training that they can work on the device under the supervi-
sion and guidance of a trained specialist.
2.4.1 Specialist staff
Thanks to their professional training, knowledge, experience and knowl-
edge of the relevant specifications, specialist staff are able to perform the
job allocated to them and recognise and/or eliminate any possible dan-
gers by themselves.