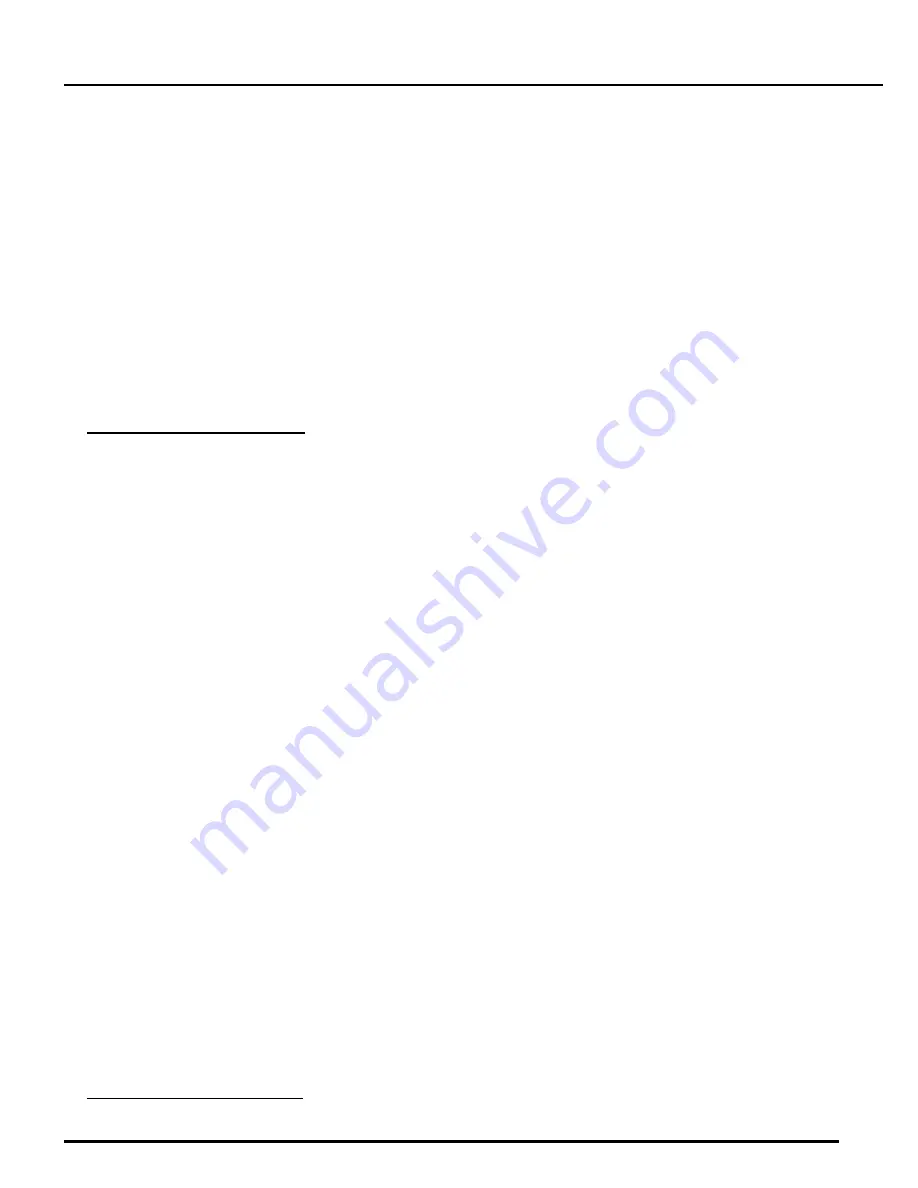
Logosol Multifunctional Servo Drive LS-231SE
Doc # 712231004 / Rev. A, 05/05/2011
Logosol, Inc.
•
1155 Tasman Drive
•
Sunnyvale, CA 94089 Tel: (408) 744-0974
•
www.logosolinc.com
35
Power-up and Reset Conditions
After Power-up or reset, the following state is established:
Motor position is reset to zero
Velocity and acceleration values are set to zero
All gain parameters and limit values are set to zero
The servo rate divisor is set to 1 (51.2 µSec servo rate)
The PWM value is set to zero
The controller is in PWM mode
The default status data is the status byte only
The individual address is set to 0x00 and the group address to 0xFF (group leader not set)
Communications are disables pending a low value of A in
The baud rate is set to 19.2 Kb/S
In the status byte, the move_done and pos_error flags will be set and home_in_progress flag will be cleared.
In the auxiliary status byte, the pos_wrap, servo_on, accel_done, slew_done and servo_overrun flags will be
cleared
.
Coordinated motion control – Theory of operation
LS-231SE contains a path point buffer with room for 256 entries. Each entry is a goal position for the
motor. When the
Servo Drive
enters its special path mode, it will automatically move from one point to
the next at a user selectable rate in steps of 51.2 µSec. The Servo Drive moves the motor between goal
points at a constant velocity such that it always arrives at the next path point in exactly the pre-
calculated time. When sets of path points are downloaded into multiple controllers, and then the paths
started simultaneously, the individual axes will execute their paths with exact
synchronization.
If, for example, the time between the points is set to 5.12 mSec, the path point buffer has room for about
1.3 seconds worth of motion. Typically, the host computer downloads the first part of a path to the LS-
231SE buffers and then starts the path mode. As the buffers becomes depleted, additional path points
are dynamically added while the axes are still in motion, until the path is complete. The timing
requirements for the host require that it be able to dynamically download new path points before the
path point buffers empties completely. With a path point buffer size of 1.3 seconds or even more with
lower frequency, even a non-real time host, such as a PC running Windows, can easily keep up with the
task of re-filling the path point buffers as needed.
The actual multi-axis paths, which are downloaded into the LS-231SE path point buffers, are calculated
by the host computer. In addition to creating the geometry desired (arcs, lines, etc.), the path should be
smooth, adhering to the physical acceleration and velocity limits of the motors being controlled. Because
the host computer actually creates the paths, any path the user can create can be executed, and paths
can involve up to 31 axes. Most typically, coordinated straight-line motions, 2-axis circular motions, or S-
curve profiling motions are created.
Note that motions created with the path mode are independent of any acceleration or velocity values
loaded using the Load Trajectory command.
Path Accuracy
The path accuracy of the LS-231SE Servo Drive is more than adequate for most CNC machine control
or robot control applications. For very high speed or very high accuracy applications, however, there are
two types of path errors to consider: absolute path errors and timing errors.
Absolute Path Errors
Absolute path accuracy is the accuracy with which a series of calculated path points with straight line
segments between them matches the actual curved path desired. For example, a circle, which is
approximated by only 5 path points, will form a pentagon rather than a circle. The maximum error
between the side of the pentagon and the circle may be quite large. A larger number of path points will
*
The exactness of the synchronization is subject to crystal frequency accuracy and other timing factors discussed
later.