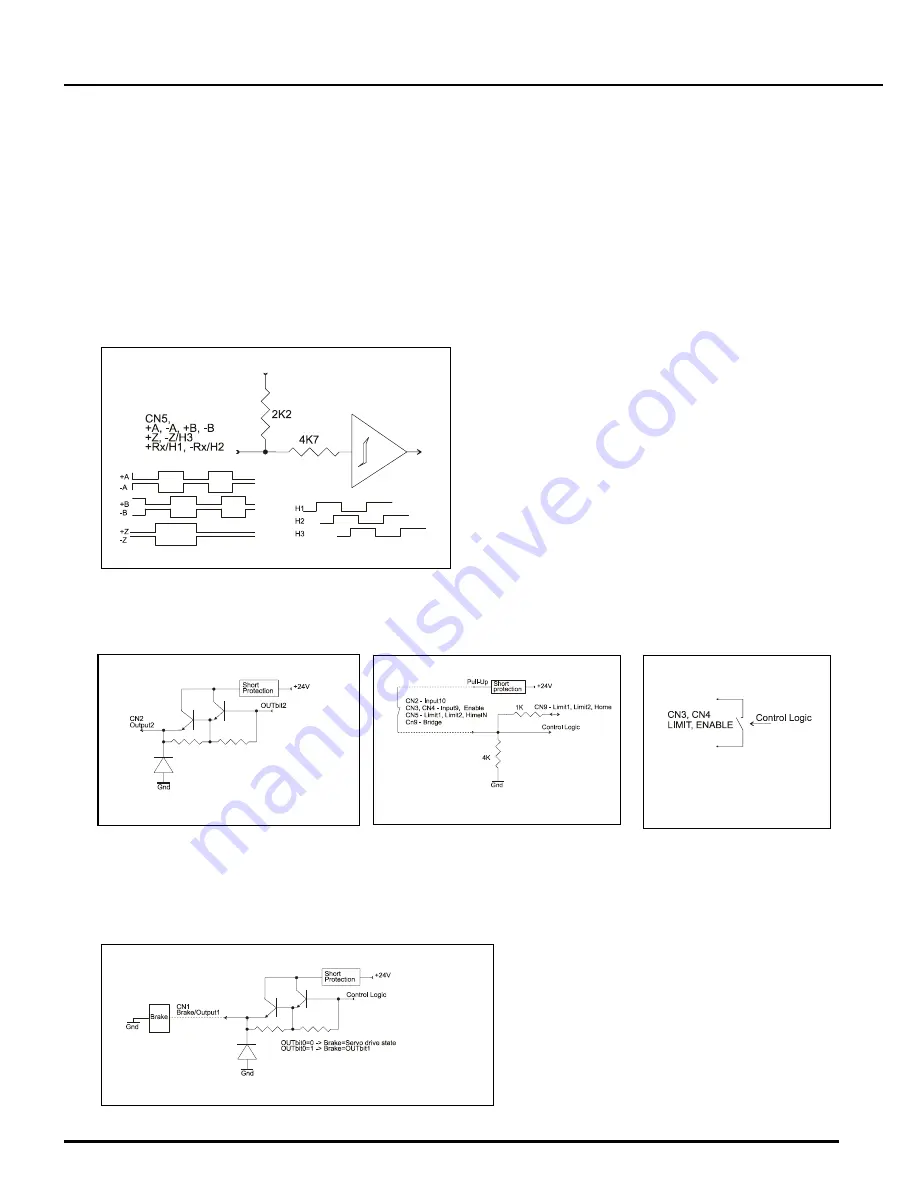
Logosol Multifunctional Servo Drive LS-231SE
Doc # 712231004 / Rev. A, 05/05/2011
Logosol, Inc.
•
1155 Tasman Drive
•
Sunnyvale, CA 94089 Tel: (408) 744-0974
•
www.logosolinc.com
26
Encoder and Commutator interface
The Encoder interface accepts two square wave inputs – +A, +B (+A, -A, +B, and -B for differential
encoders) from an incremental encoder. Ideally these square waves are 50% duty cycle and +/-90
degrees out of phase. The time between encoder state transitions is limited and should not be less than
0.1uS when encoder filter is off and 0.2uS when encoder filter is on. With ideally formed encoder pulses,
this would correspond to a 2500 line encoder (10000 counts/rev) rotating at 60,000/30,000 rpm. Refer to
Logosol Quick start guide / Motor initialization to select the encoder mode.
Encoder Index +Z (+Z and –Z for differential encoders) is used by Servo control module to capture
Home position.
Hall sensors provide the motor position. They are used by motor control module to determine motor
position after power up and during the motor initialization procedure.
Besides the position control, encoder phases, index and hall sensors are used to determine the motor
commutation synchronizing the output PWM every motor rotation according to hall and encoder data.
Control interface
Refer to
Safety Features - LS-231SE diagnostic and I/O
section for inputs/outputs descriptions.
Brake/Output1
When OUTbit0=1 Brake/Output1 follows the state of OUTbit1.
When OUTbit0=0 Brake/Output1 follows the Servo drive state described in
LS-231SE Diagnostic and
I/O
. Brake current must not exceed 0.3A
Encoder and Commutator interface
Brake/Output1
Outputs - Safety bus
Input interface
Output interface