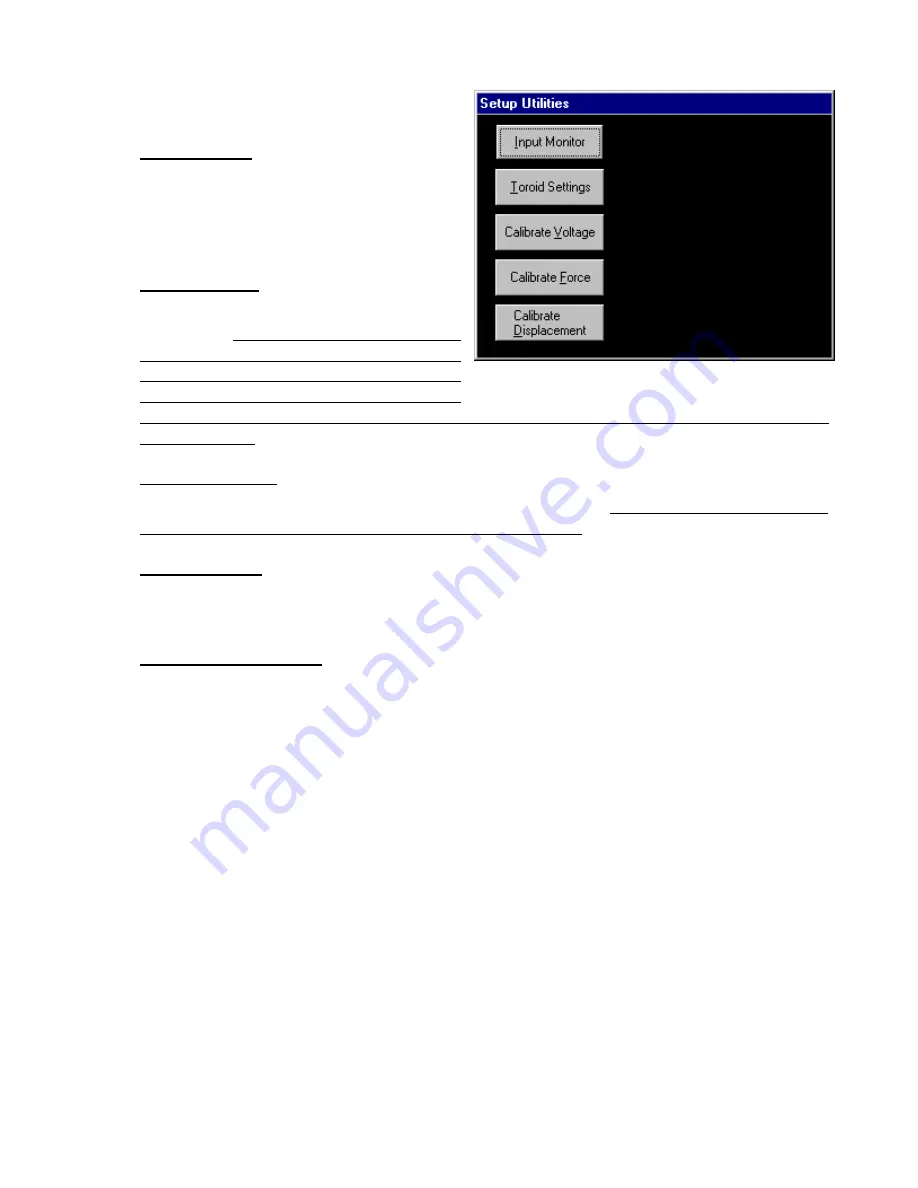
0433-INS-400 Rev. E
6-38
Setup Utilities
•
Input Monitor
This option displays the input monitor
screen, which shows the data values from
external sensors and inputs. A
Zero
Displacement
utility is also provided.
•
Toroid Settings
This utility is used adjust the toroid
calibration. The calibration is set at the
factory for use with a toroid that has a CF of
0.400 (calibration factor of 400). When
installing a toroid, the CF setting labeled on
the toroid should be entered as a whole number in this screen (Example CF of 0.354 should be
entered as 354).
•
Calibrate Voltage
This utility is used to calibrate the voltage sensor input channel. The voltage calibration values
are set at the factory, and therefore do not require calibration.
•
Calibrate Force
This utility is used to calibrate the force sensor input channel. The Force channel must be
calibrated when a new force or pressure sensor is installed.
•
Calibrate Displacement
This utility is used to calibrate the displacement sensor input channel. This channel should be
calibrated when a new displacement sensor is installed.
Figure
6-51
Setup Utilities
Summary of Contents for WELDWISE 2400
Page 1: ...Revision C 001 User s Manual WeldWise 2400 THE WELD MONITORING SPECIALISTS TM...
Page 2: ......
Page 34: ...4 6...
Page 46: ...5 12...
Page 94: ...6 48...
Page 104: ...7 10...
Page 116: ...9 4...
Page 146: ...10 30...
Page 164: ...0340 DWG 400 Rev C 11 18...
Page 165: ...0308 DWG 400 Rev D 11 19...
Page 168: ...11 22...
Page 176: ...0454 APP 118 Rev A 12 6...
Page 194: ...13 2...