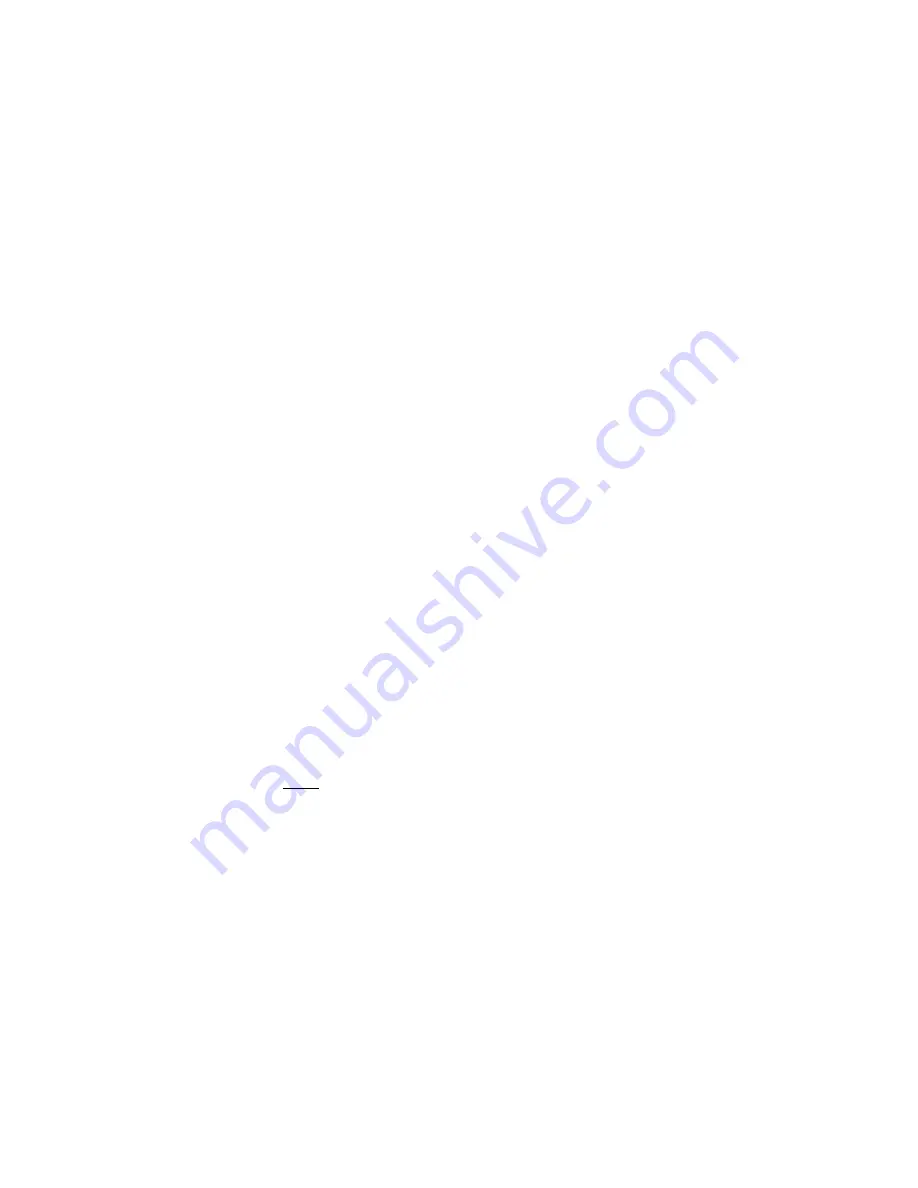
Troubleshooting Guide
Before You Begin
A little common sense will go a long way in troubleshooting a Livingston system. Check for obvious
problems first, such as loose sensors or cables and/or physically damaged components. Pay attention to
the system settings, especially calibrations and zeroing. A sensor that is not properly calibrated can
cause all kinds of problems, including inaccurate master data and tolerances. Examining weld data can
also provide a good indication of something not functioning properly. For example, a
Setdown
of
0.000" for a projection nut weld does not make much sense. However, if the displacement sensor was
not properly zeroed and the data being measured is outside of the displacement window, the
Setdown
parameter will be zero.
The following chart is not intended to be a comprehensive problem-solver for every possible situation;
rather, it is designed to provide the user with a starting point from which to diagnose possible causes of
system problems. If you are unsure about or are having serious problems with a Livingston system,
contact Livingston Service for assistance.
Notes:
•
It is OK if a force sensor does not read zero when the electrodes are open. The tooling itself has
weight and the amount supported by cabling, shunts, etc. is not repeatable.
•
When troubleshooting displacement, be sure to check the rigidity of the displacement bracket.
While observing the displacement channel on the
Input Monitor
, with the gun closed @ force
attempt to move one end of the displacement sensor. If the readings jump, the bracket or rod
ends may be loose. To avoid inaccurate readings it is important that the displacement sensor-
mounting brackets have no mechanical slop, are rigid and do not move.
•
If the displacement reading saturates in the
Input Monitor
(+/- 32767
,
channel input range has
been exceeded) while attempting to calibrate with a gauge block, the gauge block is too thick.
Refer to Chapter 9, FAQ for more information about using a gauge blocks to zero and calibrate
the displacement.
Understanding A/D Readings
This chapter utilizes the Input Monitor screen for troubleshooting the various sensors.
There are two different values reported for each sensor; calibrated values (not reported for
current) and A/D values.
The A/D values represent the analog sensor signals that have been converted to digital
readings.
The calibrated values displayed are the incoming readings after the sensor has been calibrated.
The A/D values can help determine the electrical integrity of the sensor and/or sensor cable.
Always take note of the A/D readings if a sensor does not calibrate properly. If a sensor and/or
0455-INS-400 Rev. C
10-3
Summary of Contents for WELDWISE 2400
Page 1: ...Revision C 001 User s Manual WeldWise 2400 THE WELD MONITORING SPECIALISTS TM...
Page 2: ......
Page 34: ...4 6...
Page 46: ...5 12...
Page 94: ...6 48...
Page 104: ...7 10...
Page 116: ...9 4...
Page 146: ...10 30...
Page 164: ...0340 DWG 400 Rev C 11 18...
Page 165: ...0308 DWG 400 Rev D 11 19...
Page 168: ...11 22...
Page 176: ...0454 APP 118 Rev A 12 6...
Page 194: ...13 2...