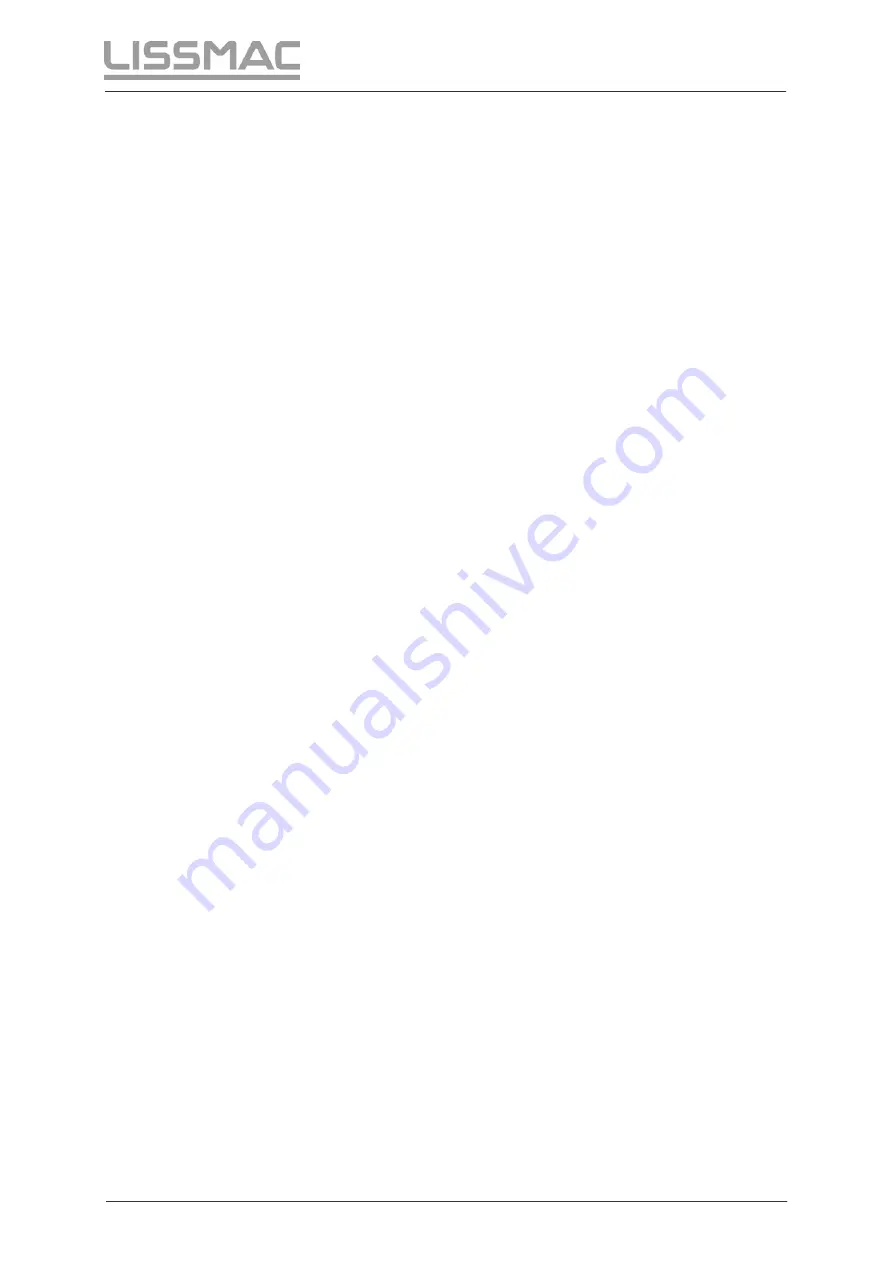
Safety
10
Steel Brush Machine SBM-M 1000/1500 B2
2.6
Maintenance, Service and Troubleshooting
Adjustment, maintenance and service work may only be carried out by
authorized technical personnel.
Perform adjustment, maintenance and service work according to
instructions in the operating manual. Keep the specified intervals for
service work.
Inform operating personnel before beginning adjustment, repair, or
maintenance work. Name a supervisor.
Always disconnect the machine from electrical power during maintenance
and repair work (main switch in the 0 position).
When the machine is being cleaned of material residues, always
disconnect the machine from the mains supply
(set main switch to 0).
Before cleaning with cleaning agents, close all openings with suitable
materials in which no water or cleaning agent can penetrate, for safety or
functional reasons. Electric motors and switches are especially at risk.
Do not perform any cleaning with high pressure cleaners.
Openings which were sealed before cleaning, must be completely
opened after cleaning.
Always tighten loosened screw connections with the specified tightening
torques during maintenance and service work.
If safety equipment is dismantled during changeover, maintenance,
service and repair, remount and check the safety equipment immediately
after the work is completed.
Dispose of operating and auxiliary materials and replacement parts safely
and in accordance with country-specific regulations.
Summary of Contents for SBM-M 1000 B2
Page 2: ...About this manual 2 Steel Brush Machine SBM M 1000 1500 B2...
Page 54: ......