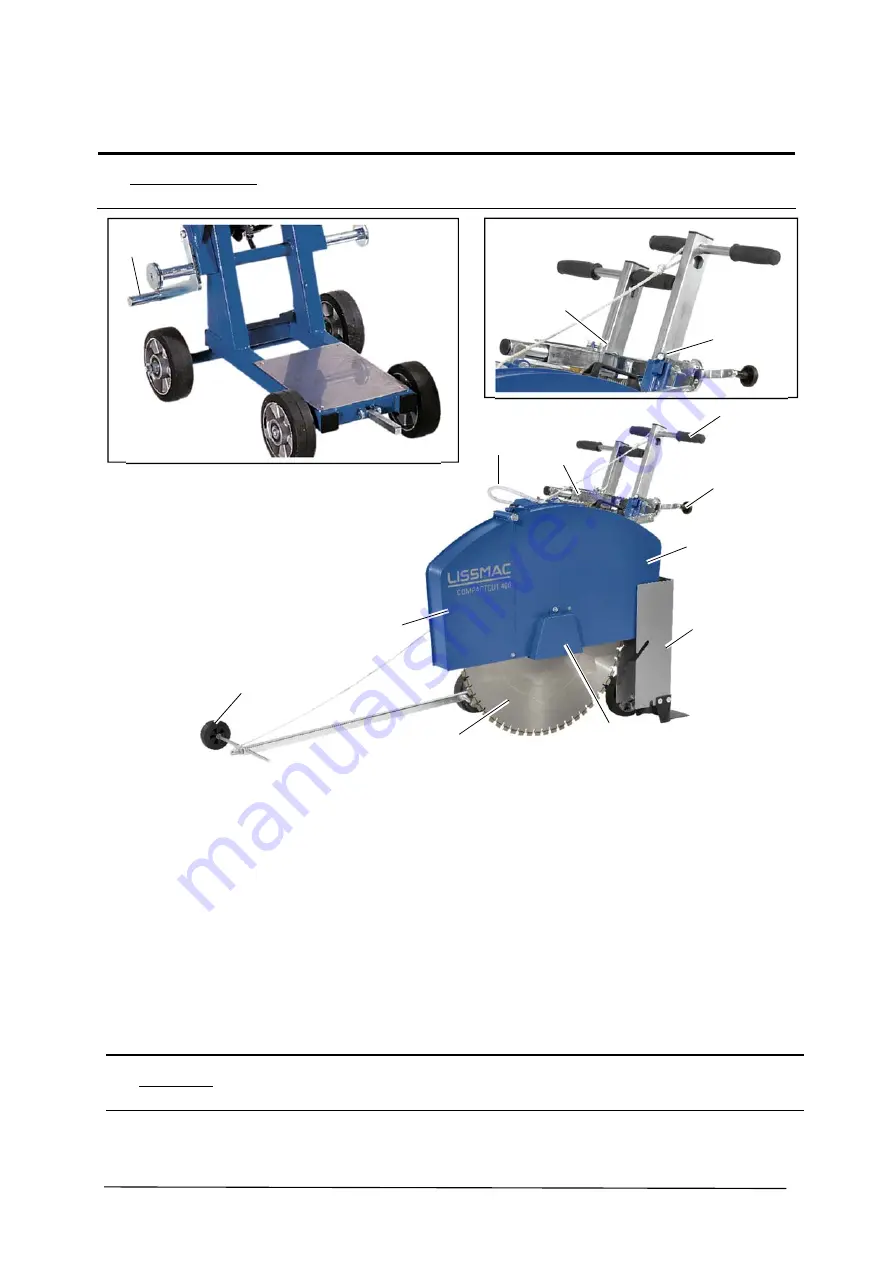
16/45
2.
DESCRIPTION OF THE DEVICE
2.1.
Name of machine parts
Pos. 1
Water hose
Pos. 8
Saw blade
Pos. 2
Saw arm
Pos. 9
Steering rod
Pos. 3
Handle
Pos. 10
Fold up part of the saw blade protective hood
Pos. 4
Handle (height adjustment)
Pos. 11
Parking brake
Pos. 5
Saw blade protective hood
Pos. 12
Thumb screw for table foot adjustment
Pos. 6
Spray protection
Pos. 13
Thumb screw for the handle
Pos. 7
Flange cover of the saw blade protective hood
2.2.
Safety guards
Pos. 5
Pos. 6
Spray protection
3
6
5
10
1
7
8
9
4
2
13
12
11