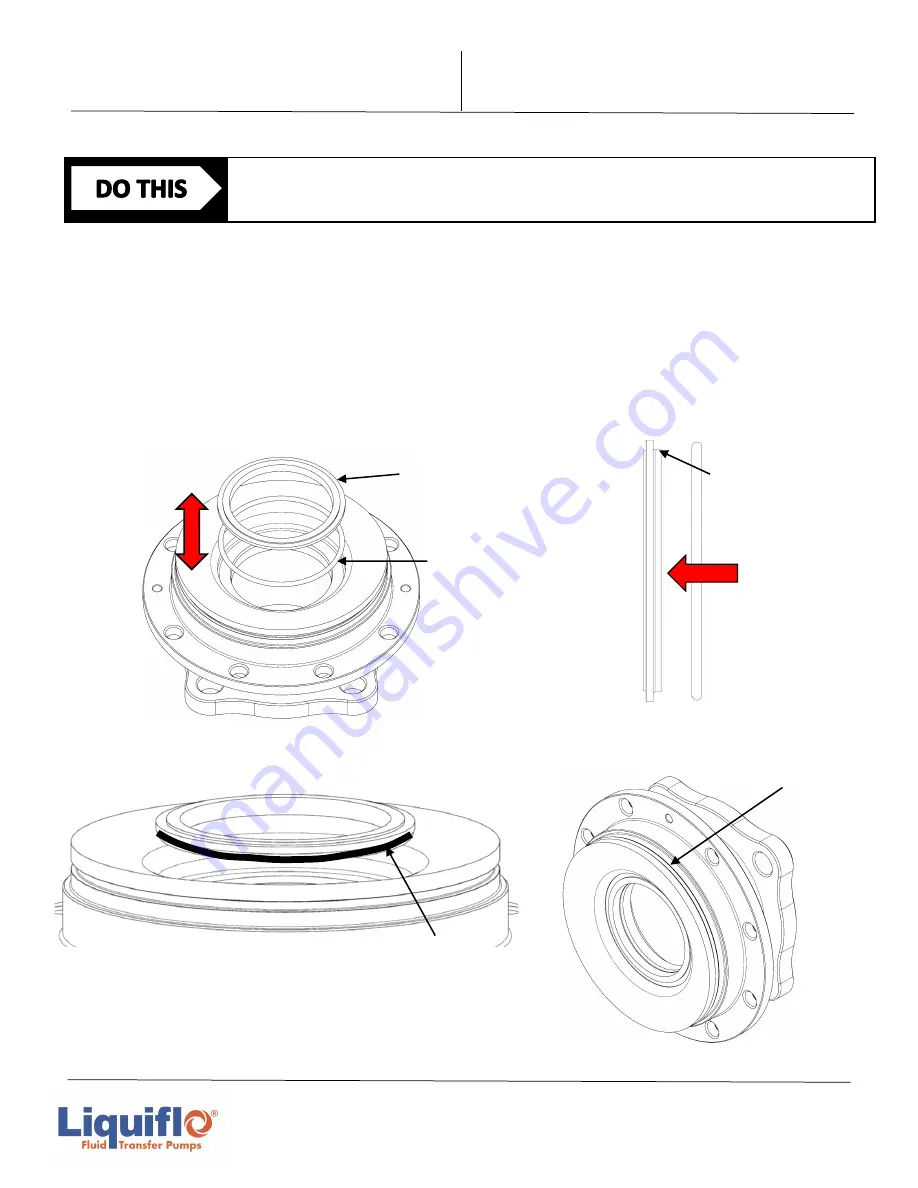
4
Maintenance and service
Liquiflo FTS Transfer Pump User Manual
Series No. FTS300
34
Replacing inlet seal wear ring, inlet seal O-ring, and inlet cover housing O-ring
1.
Orient the inlet cover with the flange side down, identify the inlet seal wear ring, and extract it from the inlet cover,
Figure 1.
2.
If the inlet seal O-ring did not come out with the inlet seal wear ring, locate the inlet seal O-ring and extract it from
the inlet cover.
3.
Install the new inlet seal O-ring (size 2-246) onto the inlet seal wear ring, Figure 2.
4.
Install the inlet seal wear ring with the O-ring facing inward, Figure 3. Be sure that the orientation of the wear ring is
correct.
5.
Using an O-ring pick, gently pry the inlet cover housing O-ring out of its groove, and discard, Figure 4.
6.
Carefully loop the new inlet cover housing O-ring (size 2-265) around the inlet cover, and ensure the entire O-ring
is fully seated in the groove.
Lubricate O-rings with Dow Corning Molykote
®
111 lubricant.
Figure 1
Figure 4
Housing O-ring
O-ring
Inlet seal
wear ring
NOTE:
O-ring goes on deeper
groove of wear ring
Figure 2
Figure 3
O-ring
Inlet seal wear ring
O-ring