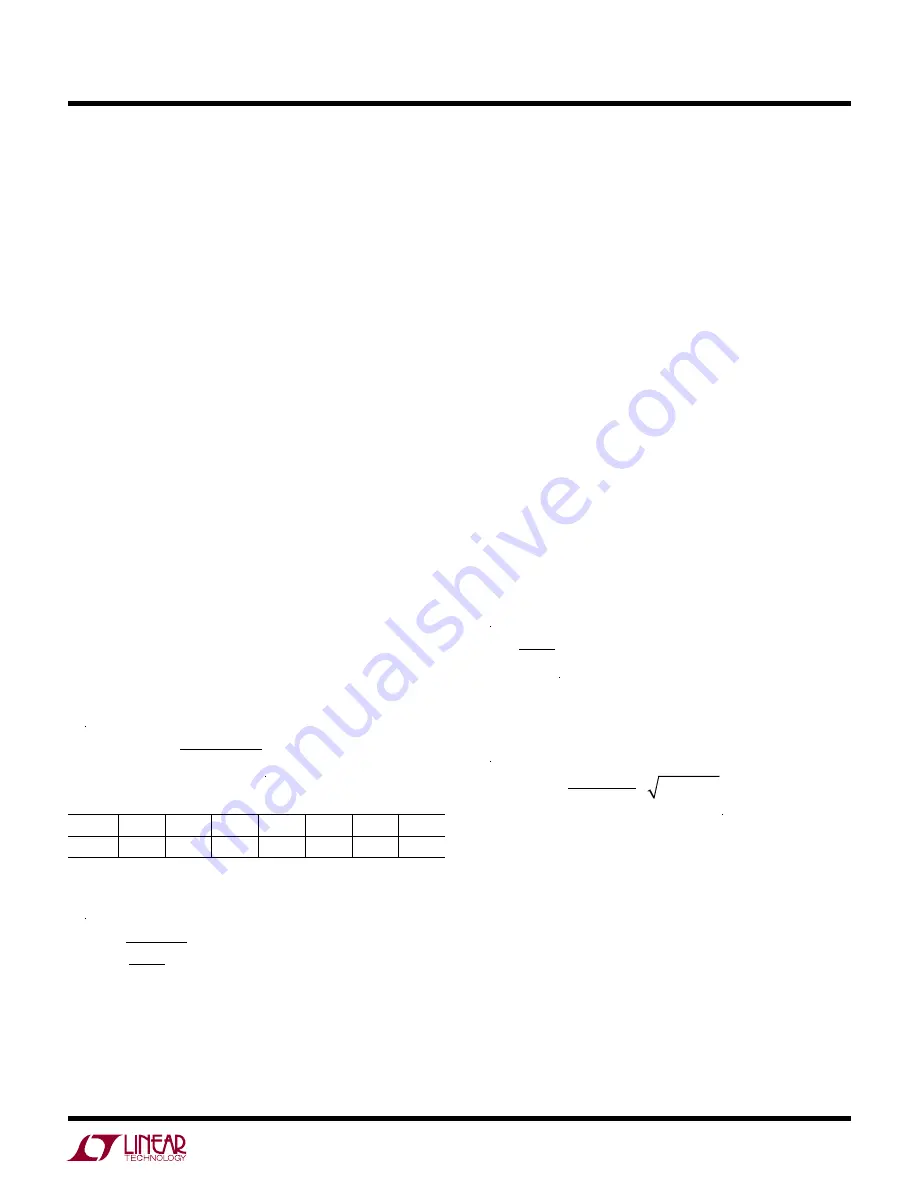
LTM4636
11
4636f
applicaTions inForMaTion
The typical LTM4636 application circuit is shown in
Figure 20. External component selection is primarily
determined by the maximum load current and output
voltage. Refer to Table 5 for specific external capacitor
requirements for particular applications.
V
IN
to V
OUT
Step-Down Ratios
There are restrictions in the V
IN
to V
OUT
step-down ratio that
can be achieved for a given input voltage. The maximum
duty cycle is 94% typical at 500kHz operation. The V
IN
to
V
OUT
minimum dropout is a function of load current and
operation at very low input voltage and high duty cycle
applications. At very low duty cycles the minimum 100ns
on-time must be maintained. See the Frequency Adjust-
ment section and temperature derating curves.
Output Voltage Programming
The PWM controller has an internal 0.6V ±1% reference
voltage. As shown in the Block Diagram, a 4.99k internal
feedback resistor connects the V
OUTS1
+
and V
FB
pins to-
gether. When the remote sensing is used, then V
OUTS1
+
and V
OUTS1
–
are connected to the remote V
OUT
and GND
points. If no remote sense the V
OUTS1
+
connects to V
OUT
.
The output voltage will default to 0.6V with no feedback
resistor. Adding a resistor R
FB
from V
FB
to ground pro-
grams the output voltage:
V
OUT
=
0.6V
•
4.99k
+
R
FB
R
FB
Table 1. V
FB
Resistor Table vs Various Output Voltages
V
OUT
(V)
0.6
1.0
1.2
1.5
1.8
2.5
3.3
R
FB
(k)
Open
7.5
4.99
3.32
2.49
1.58
1.1
For parallel operation of N LTM4636s, the following
equation can be used to solve for R
FB
:
R
FB
=
4.99k /N
V
OUT
0.6V
–1
Or use V
OUTS1
on one channel and connect all feedback
pins together utilizing a single feedback resistor.
Tie the V
FB
pins together for each parallel output. The COMP
pins must be tied together also. See Typical Application
section examples.
Input Capacitors
The LTM4636 module should be connected to a low AC-
impedance DC source. Additional input capacitors are
needed for the RMS input ripple current rating. The I
CIN(RMS)
equation which follows can be used to calculate the input
capacitor requirement. Typically 22µF X7R ceramics are a
good choice with RMS ripple current ratings of ~4A each.
A 47µF to 100µF surface mount aluminum electrolytic bulk
capacitor can be used for more input bulk capacitance.
This bulk input capacitor is only needed if the input source
impedance is compromised by long inductive leads, traces
or not enough source capacitance. If low impedance power
planes are used, then this bulk capacitor is not needed.
For a buck converter, the switching duty cycle can be
estimated as:
D
=
V
OUT
V
IN
Without considering the inductor ripple current, for each
output the RMS current of the input capacitor can be
estimated as:
I
CIN(RMS)
=
I
OUT(MAX)
η
%
•
D
•
(1–D)
where
η
% is the estimated efficiency of the power mod-
ule. The bulk capacitor can be a switcher-rated aluminum
electrolytic capacitor or a Polymer capacitor.