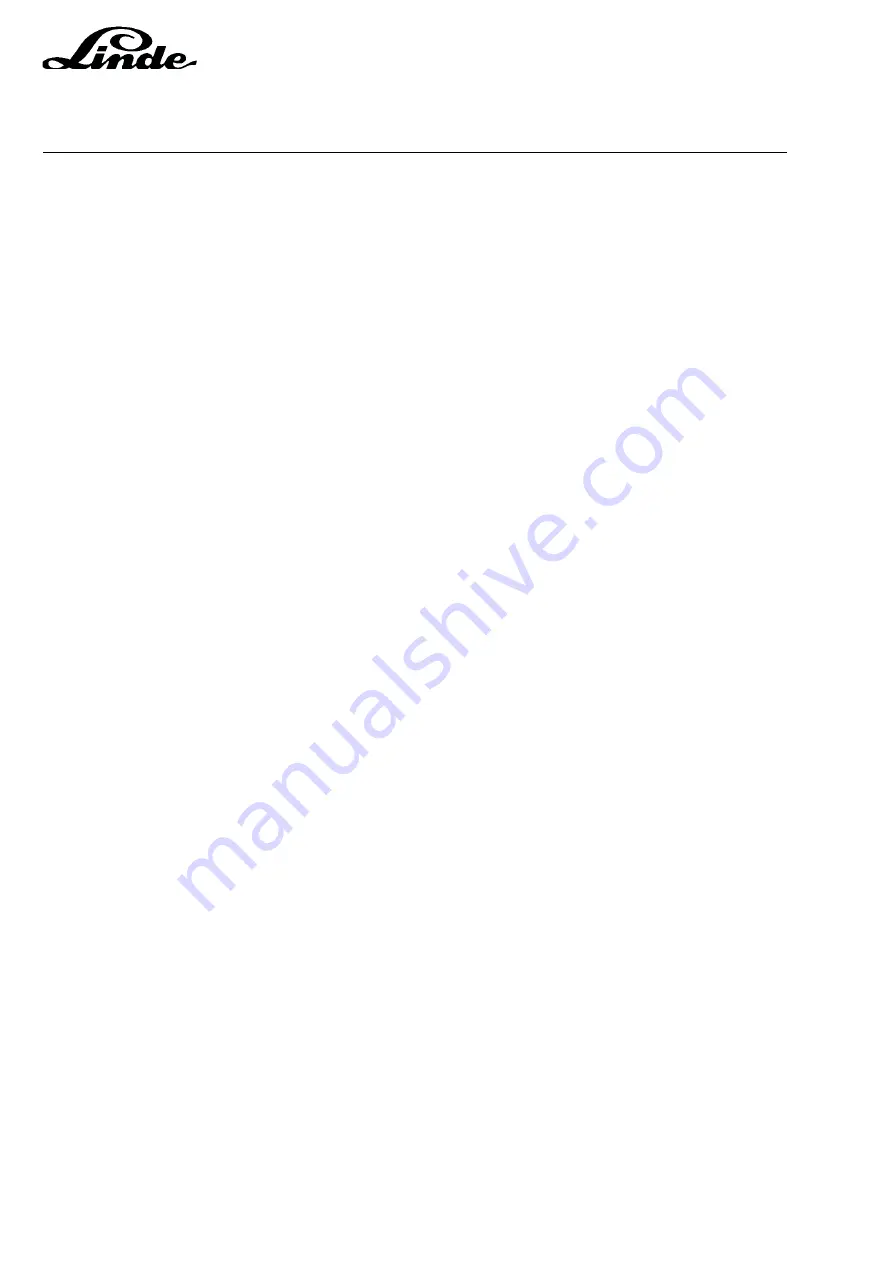
Service Training
Section
2.2
Page
6
2.2.3
PLANETARY HUB REDUCTION GEARBOX (FROM 1/95 TO 5/95)
NOTE:
For design reasons, the planetary hub reduction gearbox on trucks to series 12/94 can only be
exchanged as an assembly.
2.2.3.1
REMOVING THE PLANETARY HUB REDUCTION GEARBOX FROM THE TRACTION
MOTOR
- Jack up and secure the truck.
- Remove the wheel nuts and wheels.
- Place an oil pan underneath the gearbox.
- Remove the oil filler plug (1).
- Remove the oil drain plug (14) and copper sealing ring (15).
- Drain the transmission oil.
- Remove the 14 socket head screws (13).
- Remove the planetary hub reduction gearbox from the bearing plate, taking care not to lose the O-ring (17).
- Clean the sealing areas.
2.2.3.2
DISASSEMBLY OF THE PLANETARY HUB REDUCTION GEARBOX
- Remove the hexagonal head screw (6).
NOTE:
The hexagon head screw (6) is self-locking and can therefore only be used once.
- Remove the two plugs (8).
- Use a puller to extract the flange (10).
- Put the flange (10) aside and secure it against sliding.
- Insert a drift alternately into the two access holes (9) and knock the bearing inner race (12) off the flange.
- Remove and renew the shaft sealing ring (11).
- The O-ring (4) is accessible after pressing out the washer (7) from the flange (10).
- Check and renew, if necessary, O-rings (5) and (4).
NOTE:
There are shims (3) mounted between the flange (10) and washer (7). During assembly all shims
must be installed again with the 0.5 mm shim on the profile side of the flange (10).
2.2.3.3
ASSEMBLY OF THE PLANETARY HUB REDUCTION GEARBOX
- Put the gearbox housing vertical and secure it against sliding.
- Install the bearing inner race (12), making sure that it is seated evenly.
- Half fill the sealing shaft ring (11) with grease and drive it into the housing (2).
- Install the shims (3) in the flange (10).
- Position the O-ring (5) on the washer (7) and secure it with grease.
- Press the washer (7) and O-ring (4) into the flange (10).
- Position the flange (10) and washer (7) on the planetary hub reduction gearbox (18), taking care not to
damage the teeth.
- Install the hexagon head screw (6) through the washer (7) and carefully tighten it to seat the flange (10)
and washer (7) correctly (torque to 810 Nm).
- Install the 2 plugs (8) in the flange (10) (torque to 20 Nm).
Summary of Contents for 336 Series
Page 2: ......
Page 8: ...ServiceTraining ...
Page 12: ...ServiceTraining Section 2 1 Page 4 ...
Page 14: ...ServiceTraining Section 2 1 Page 6 2 1 4 TRACTIONMOTORDISASSEMBLY ...
Page 19: ...ServiceTraining Section 2 2 Page 3 ...
Page 21: ...ServiceTraining Section 2 2 Page 5 ...
Page 27: ...ServiceTraining Section 2 2 Page 11 ...
Page 28: ...ServiceTraining Section 2 2 Page 12 ...
Page 33: ...ServiceTraining Section 2 4 Page 1 2 4 STEERING SYSTEM ...
Page 35: ...ServiceTraining Section 2 4 Page 3 ...
Page 37: ...ServiceTraining Section 2 4 Page 5 ...
Page 39: ...ServiceTraining Section 2 4 Page 7 ...
Page 41: ...ServiceTraining Section 2 4 Page 9 ...
Page 45: ...ServiceTraining Section 2 4 Page 13 ...
Page 47: ...ServiceTraining Section 2 4 Page 15 ...
Page 53: ...ServiceTraining Section 2 5 Page 5 ...
Page 54: ...ServiceTraining Section 2 5 Page 6 ...
Page 69: ...ServiceTraining Section 2 6 Page 15 ...
Page 74: ...ServiceTraining Section 2 6 Page 20 2 6 2 3 CIRCUIT BREAKER CONTACTOR 1K6 Circuit diagram ...
Page 94: ...ServiceTraining Section 2 6 Page 40 ...
Page 111: ...ServiceTraining Section 2 6 Page 57 Connector 1X6 1 15 V 2 Output signal 3 ...
Page 126: ...ServiceTraining Section 2 6 Page 72 2 6 9 2 LOCATION OF CONNECTORS FROM SERIES 7 95 ...
Page 128: ...ServiceTraining Section 2 6 Page 74 ...
Page 145: ...Section 2 6 Page 91 ...
Page 146: ......
Page 147: ......
Page 149: ...Section 2 6 Page 93 ...
Page 150: ......
Page 153: ...ServiceTraining Section 2 7 Page 3 ...
Page 157: ...ServiceTraining Section 2 7 Page 7 ...
Page 158: ...ServiceTraining Section 2 7 Page 8 ...
Page 163: ...Section 2 9 Page 5 ...
Page 164: ......
Page 166: ...ServiceTraining Section 2 10 Page 2 ...
Page 167: ......