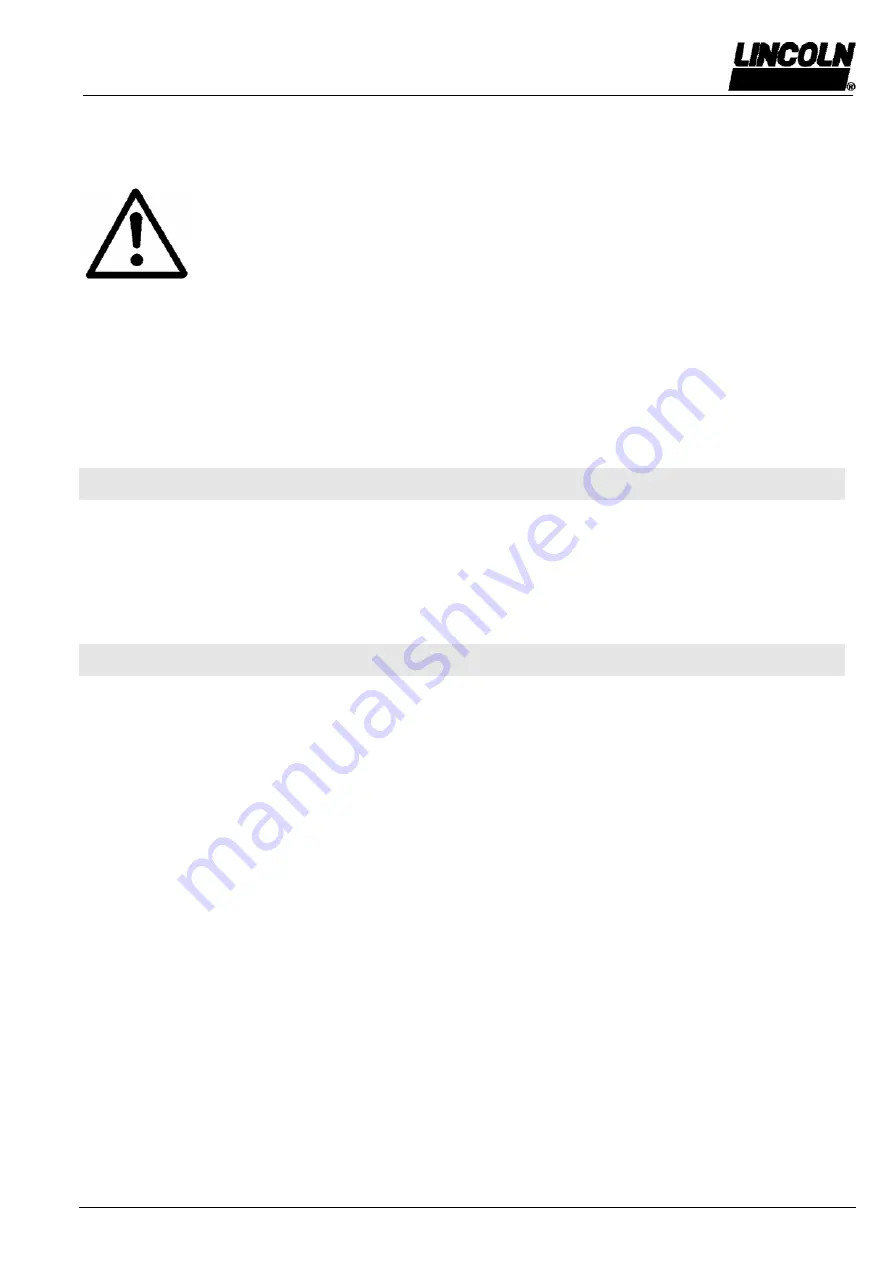
Owner’s Manual
Hydraulic pump 609-29232-1 Single-line with 165-l container
4.1EN-68607-G09
Subject to changes
Page 7 of 15
LINCOLN GmbH Postfach 1263 D-69183 Walldorf Tel +49 (6227) 33-0 Fax +49 (6227) 33-259
Maintenance and repairs
•
Do not disassemble the pump while the hydraulic cylinder,
the pump tube and the supply system are under pressure.
•
Do not rinse or clean the pump/pump tube with flammable
fluids.
•
Hands off the lower part (suction inlet) of the pump during
starting, trial run and operation of the pump.
Before disassembling the pump, stop it and relieve the
pressure from the drive (hydraulic cylinder), pump tube and
supply system.
Drain the supplied medium by opening an outlet valve
(shut-off valve, gun) of the supply line and collect it into a
basin.
Warning. The supplied medium is still under pressure. Once
the line is pressureless and the medium no longer issues,
close the shut-off valve located nearest to the supply line.
Only then, carefully loosen the connection with the supply line
at the outlet of the pump tube and unscrew the line (hose).
Maintenance, inspection and repair work may be carried out
only by qualified personnel.
Troubleshooting
••••
Fault: Pump does not deliver
••••
Cause:
••••
Remedy:
•
Hydraulic pressure supply insufficient
•
Check hydraulic pressure.
Setting of pressure reducing valve
(fig. 3) too low.
Increase setting.
•
No input signal (voltage) at the solenoid valve
see figure 2
•
Check electric connections and solenoid valve
••••
Fault : No pressure build-up in the system
••••
Cause:
••••
Remedy:
•
Grease container empty
•
Refill grease container
•
Air pockets in pump tube
•
Vent pump:
Loosen knurled thumb screw (item 10, fig 5). As soon as
the grease issues without air pockets, retighten screw.
•
Lubricant lines leaky
•
Check the line system for loosened fittings, broken lines
and detached hoses. Retighten the fittings, replace the
defective tubing. Replace the hose or connect it anew.
•
Inlet valve in pump tube damaged or worn
•
Disassemble, check and replace it if necessary.
•
Precision piston (item 26, fig. 5) damaged or worn
•
Disassemble, check and replace it if necessary.
•
The supplied medium cannot be sucked properly
because it is too viscous and the stroke frequency is too
high.
•
Reduce the stroke frequency by throttling the output flow
(pressure reducing valve
,fig. 3).