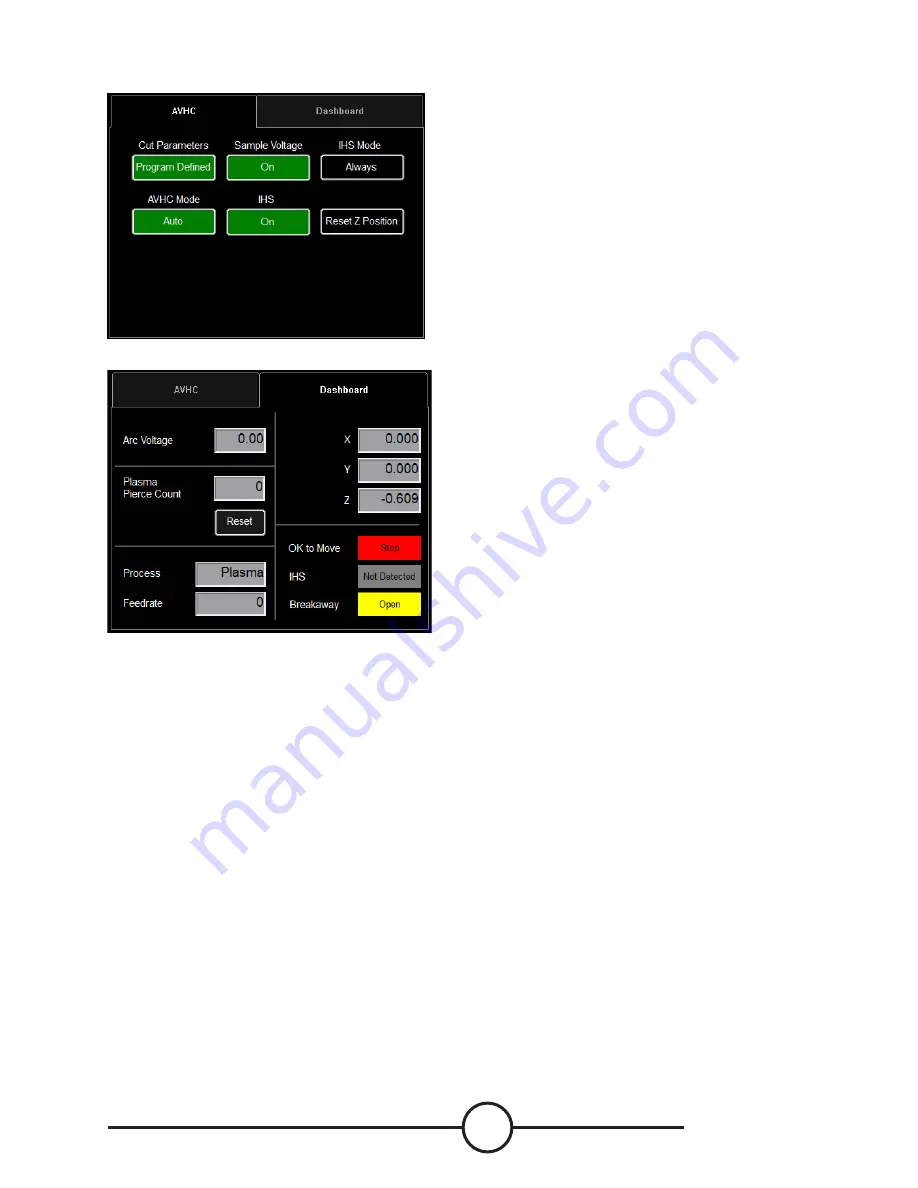
35
User Guide
IHS (Initial Height Sense): This setting turns OHMIC
DETECTION on or off.
•
ON -
The head will detect material when the ohmic
cap comes into contact with the grounded, conductive
material on the table. Once detected the head will retract
to the TRANSFER HEIGHT setting.
•
OFF -
The head will move to TOP OF MATERIAL setting
(Plate Setup) and retract to TRANSFER HEIGHT.
RESET Z POSITION:
Resets the Z lifter to its Zero Position
by moving the head to it's upper most position and resets
Z-Axis zero point.
Dashboard:
The dashboard displays the host indicators and tools for
the operator.
•
Arc Voltage -
Displays the Arc Voltage feedback from the
plasma during cutting.
•
Plasma Pierce Count -
Counts the ARC ON commands
as they take place. Reset clears the count back to zero.
Recommend to reset with changing of the consumables.
•
Process -
Displays the current cutting process.
•
Feedrate -
Displays the real-time feedrate.
•
X, Y, Z -
Shows the torch coordinates relative to the
machine space.
•
OK to Move -
Indicates when the plasma has pierced
through the material and is ready to start the program.
•
IHS -
Indicates when the material is detected via OHMIC.
•
Breakaway -
Indicates if the breakaway circuit is open/
closed.
AVHC & Dashboard:
Summary of Contents for Torchmate 5100 Series
Page 1: ...March 31 2021 Copyright 2021 Lincoln Electric Cutting Systems USERGUIDE ...
Page 84: ......
Page 85: ......
Page 86: ......