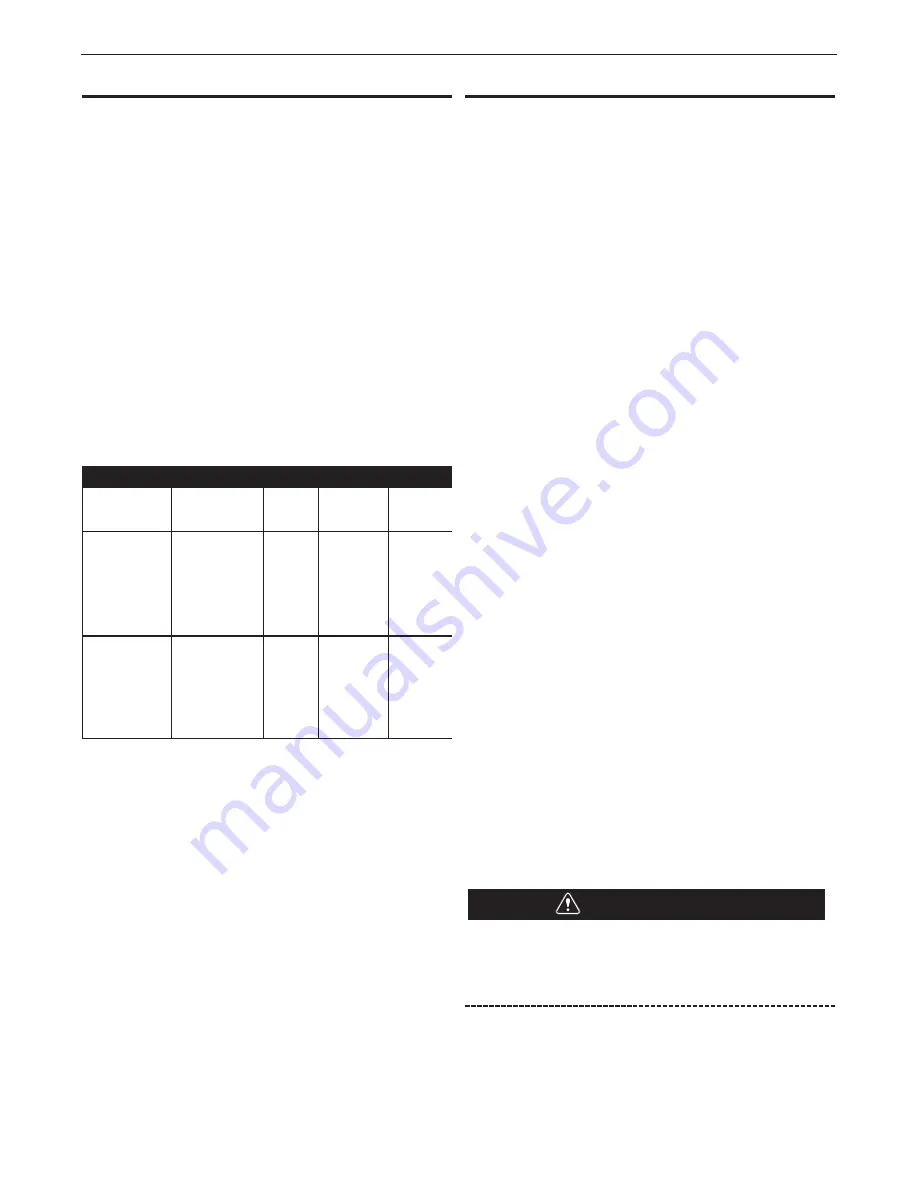
D-2
MAINTENANCE
PERIODIC MAINTENANCE
The product has been designed to function without problems for
many hours with minimal maintenance. In order to ensure this,
some simple regular maintenance and cleaning activities are
required which are described in this section. If you observe the
necessary caution and carry out the maintenance at regular
intervals, any problems that occur will be detected and corrected
before they lead to a total breakdown.
The indicated maintenance intervals can vary depending on the
specific working and ambient conditions. Therefore it is
recommended to thoroughly inspect the complete product once
every year other that the indicated periodic maintenance.
Follow OSHA protocols and your company's JHA safety
procedures when servicing this equipment. Keep personnel from
entering work area under unit and tether tools and anything else
that could fall to the floor.
The maintenance activities in Table D.1 indicated by [*] can be
carried out by the user; other activities are strictly reserved for
well trained and authorized service engineers.
The maintenance activities in Table D.1 indicated by [*] can be
carried out by the user; other activities are strictly reserved for
well trained and authorized service engineers.
* Frequency depends on welding or cutting process.
MAINTENANCE SCHEDULE
NOTE: * REQUIRES Lincoln Electric factory authorized service
technician.
AS NEEDED
• Replace filters (see filter replacement instructions).
• Inspect and test functionality of the filter media cleaning
system. *
• Program and verify system performance. *
• Follow governing local building codes for inspection
requirements following any significant event. Significant events
include but are not limited to seismic and other impacts to the
unit or structural mounts.
MONTHLY
• Check particulate collection drum and dispose of particulate if
necessary.
• Check and log filter pressure.
• Check fan speed.
• (Hanging mount): Visually inspect secondary support cables
are not taut. Taut cables can be an indication of primary support
failure.
EVERY 3 MONTHS
• Inspect and clean or replace pre-filters installed on the sides of
the unit.
EVERY 6 MONTHS
• Ensure that the Cubic Feet per Minute (CFM) is operating to the
engineered specifications based on the individual system *
• Clean inlet dampers as specified under the INLET DAMPERS
maintenance section.
YEARLY
• Inspect unit for proper operation and function, address any
issues found.
• Fan motor temperature is within normal ranges, a hand held IR
temp meter is a good tool for this. High motor temps indicate
bearing or winding issues and predict a failure. This can also
apply to the electrical power connections to the unit- elevated
temps on junction boxes and wire terminations are precursors to
problems.
• (Hang mount): Verify primary and secondary support brackets
and hardware remain properly in place with no signs of loosening.
• (Wall mount): Verify wall mount brackets, wall anchors and
other hardware remain in place with no signs of loosening.
• Inspect external unit components, including but not limited to
the door hinge, side intake housing and all hardware.
EVERY 5 YEARS
• Inspect condition of unit mounting. This includes but is not
limited to the building structure, brackets, hardware and any
other structural supports. Address any issues found.
MOTOR/FAN HOUSING
Observe safety precautions when working on the inside
of the fan box or control panel. Removing power and
observing LOTO (Lockout-Tagout) procedures as
required.
•
Check the integrity of the fan housing and tighten all
bolts and screws if necessary.
•
Clean housing with a non-aggressive detergent.
WARNING
PRISM® SUSPEND 4000
TABLE D.1 – PERIODIC MAINTENANCE
COMPONENT
ACTION
EVERY
MONTH
EVERY 3
MONTHS
EVERY 6
MONTHS
Control Panel
*Clean inside
using an
industrial
vacuum
cleaner.
X
Drum
*Check levels
of dust and dirt
particulate.
Empty if
necessary.
X
X
X