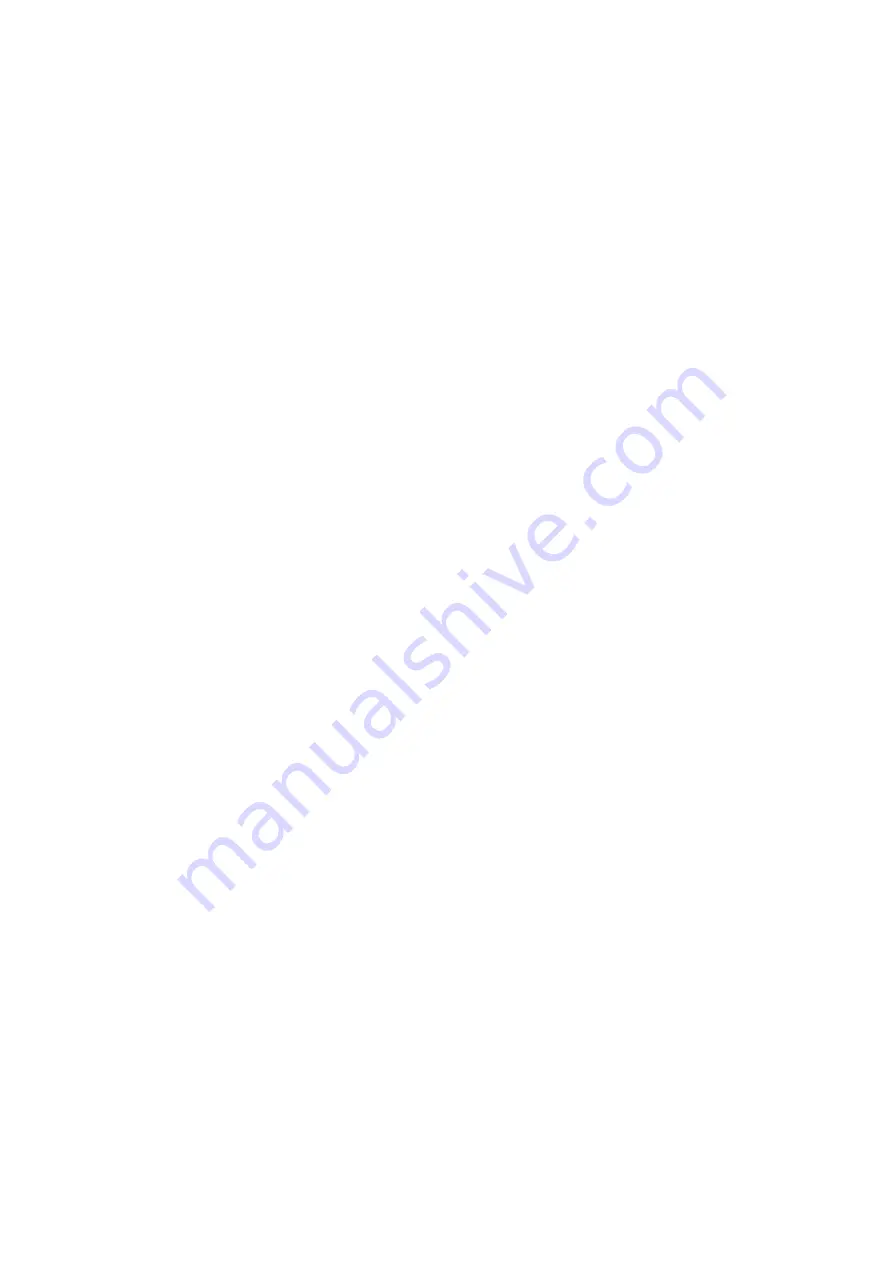
General contents
Typographic and iconographic conventions
1.1 Safety..................................................................................................................................................................................9
1.2 Electrical safety..............................................................................................................................................................9
1.3 Mechanical safety.......................................................................................................................................................10
2 Identification....................................................................................................................................... 11
3 Mechanical installation..................................................................................................................... 12
4 Electrical connections........................................................................................................................ 16
4.1 Ground connection (Figure 5)...............................................................................................................................16
4.2 Connectors (Figure 4 and Figure 5).....................................................................................................................17
4.2.1 Power supply connector.................................................................................................................................17
4.2.2 Modbus interface connectors (BUS IN and BUS OUT).......................................................................18
4.3 Diagnostic LEDs (Figure 4 and Figure 6)...........................................................................................................19
4.4 DIP switches (Figure 4 and Figure 6)..................................................................................................................21
4.4.1 Setting the node address: Node ID (Figure 7).......................................................................................22
4.4.2 Setting the Baud rate and Parity bit (Figure 7)....................................................................................23
4.4.3 RT bus termination (Figure 7)......................................................................................................................24
5.1 Configuring the device using Lika's setting up software..........................................................................25
5.2 “Serial configuration” page....................................................................................................................................26
5.3 “Operative mode” page............................................................................................................................................28
5.4 “Parameter” page........................................................................................................................................................34
5.5 “Message monitor” page.........................................................................................................................................35
5.6 “Test Lika” page............................................................................................................................................................36
5.7 “Upgrade Firmware” page.......................................................................................................................................37
6.1 Working principle.......................................................................................................................................................42
6.2 Movements: jog and positioning.........................................................................................................................43
Jog: speed control........................................................................................................................................................43
Positioning: position and speed control.............................................................................................................44
6.3 Distance per revolution [0x00], Jog speed [0x0D], Work speed [0x0E], Preset [0x12-0x13],
7.1 Modbus Master / Slaves protocol principle.....................................................................................................49
7.2 Modbus frame description......................................................................................................................................50
7.3 Transmission modes...................................................................................................................................................51