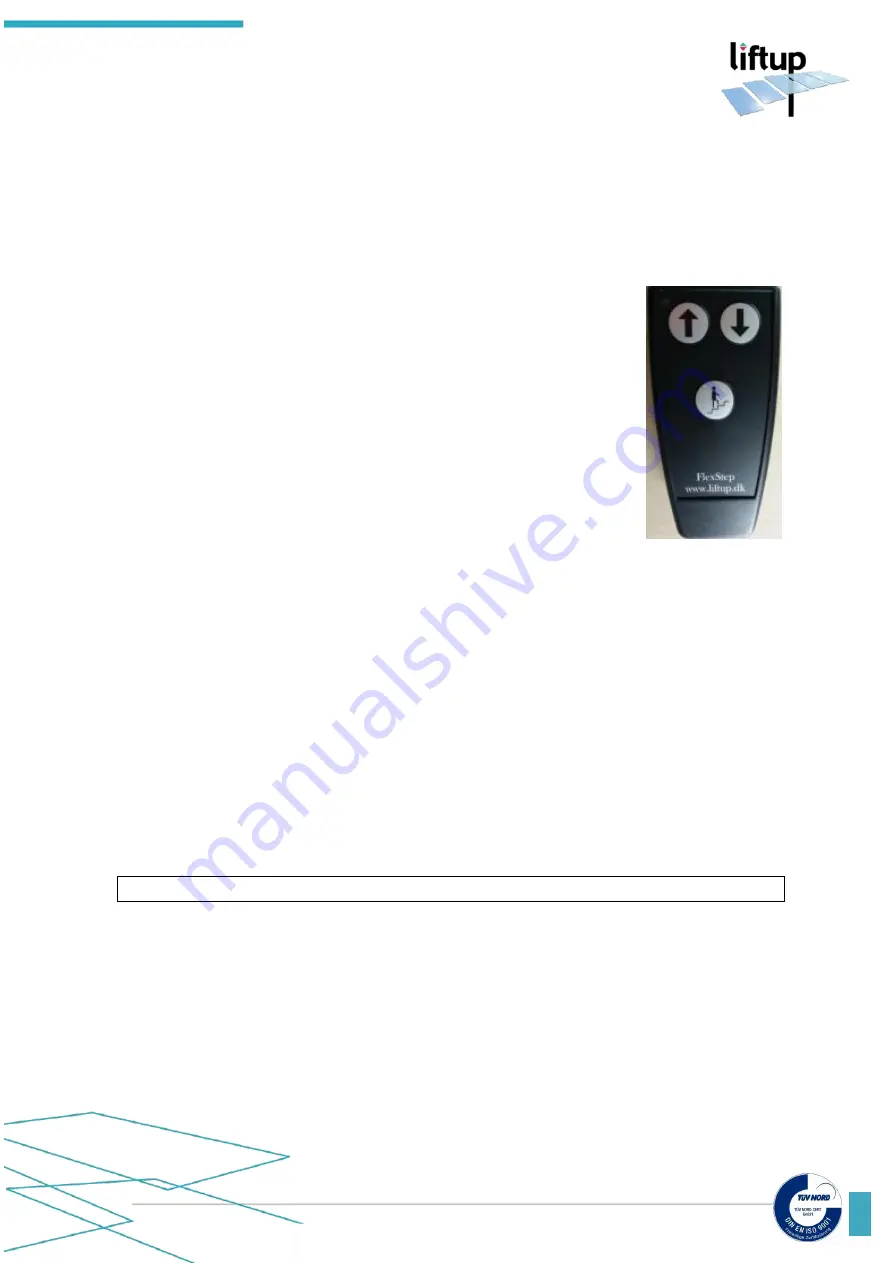
INSTALLATION & SERVICE MANUAL – FLEXSTEP V2– UK VERSION
1.7
Liftup A/S
Hagensvej 21| DK-9530 Støvring | Denmark |
T:
+45 96 86 30 20 |
M:
[email protected] | www.liftup.dk | CVR DK-1015 3964
38
4.4.2
Handheld Remote control and receiver
The transmitter and receiver must always be paired in order to work.
The receiver will not react to a transmitter which is not paired with it.
A receiver can be paired with up to 20 transmitters.
A transmitter can be paired with several receivers if required.
When a receiver is powered on (please see section 3.6) the RF-Status in the connection box will
flash for 2 minutes. Or until it is paired with a transmitter.
How to reset the transmitter and receiver
To reset a remote control so it is no longer paired, do as follows:
Press the UP (
↑
) and DOWN (
↓
) buttons at the same time and hold them down for approx. 5
seconds until the control LED on the remote control begins to flash slowly.
The remote control is now in installation mode for 2 minutes.
Perform the following within the 2 minutes:
Press: UP(
↑
), UP(
↑
), DOWN(
↓
), DOWN(
↓
), UP(
↑
), DOWN(
↓
), UP(
↑
), DOWN(
↓
)
How to reset the receiver
Switch the receiver on.
Short-circuit JP1-1on the connection box board.
When the control LED begins to flash rapidly, the receiver has been reset.
Should the control LED not flash rapidly, this means that no receiver has been paired.
1.
Ensure that there is power to the system. Press the
emergency stop and switch off the on/off switch on the
side of the lift (please see item 10.6).
2.
Press the UP (
↑
) and DOWN (
↓
) buttons on the remote
control at the same time and hold them down for approx.
5 seconds until the control LED on the remote control
begins to flash slowly. The remote control is now in
installation mode for 2 minutes.
3.
Within these 2 minutes, release the red emergency stop
on the lift by turning it clockwise.
4.
When the control LED on the remote control stops
flashing it is paired with the lift.
5.
Test the system so as to ensure the pairing has been
performed correctly; if not, repeat 1-5 above.
If you need to pair several remote controls to the
receiver, repeat item 2 above.
6.
Switch on the on/off switch on the side of the lift.