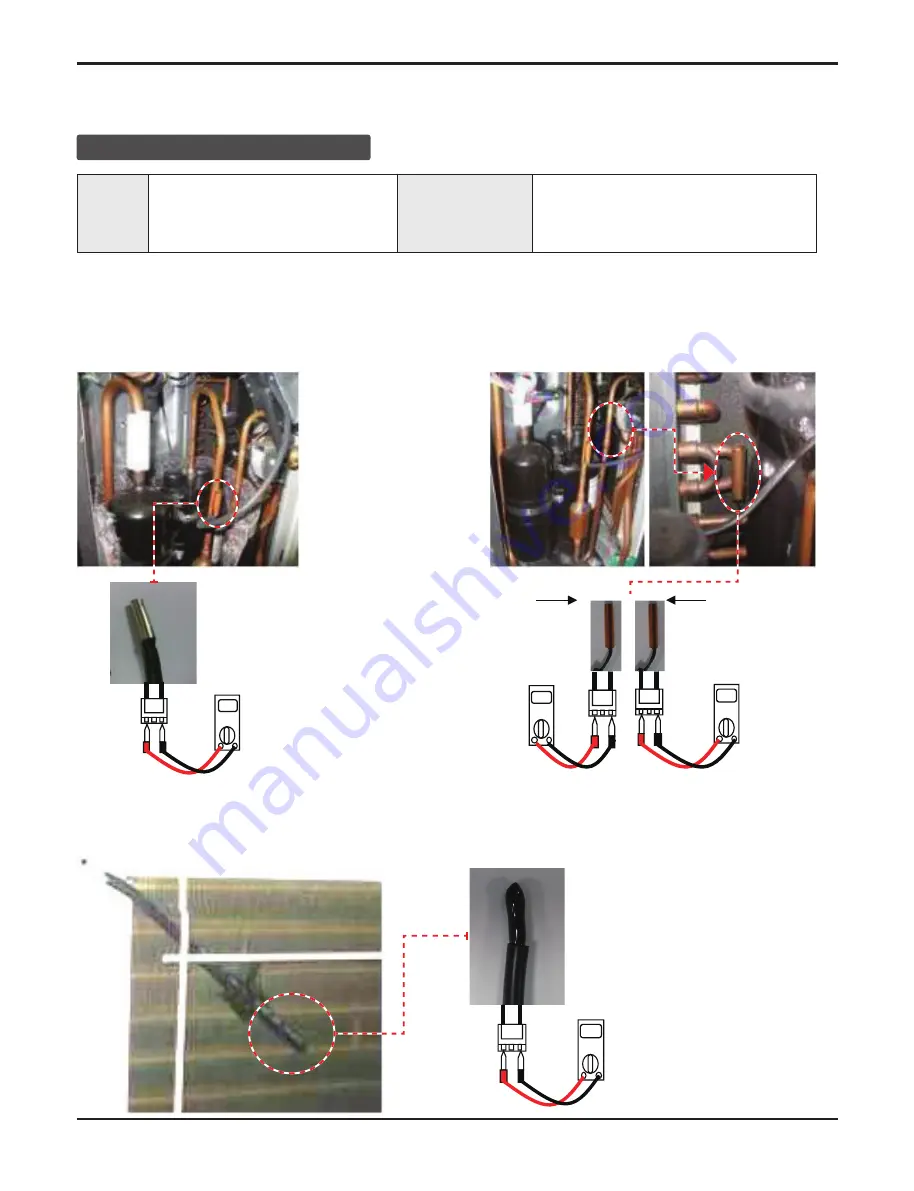
Part 4 Trouble Shooting
- 125 -
Copyright © 2019 - 2020 LG Electronics Inc.
All rights reserved. Only training and service purposes.
Purpose
Checking single units of sensors
for fault
Items for checking
Measurement of the unique resistance by
sensor temperature.
- Position : Outlet of compressor
- Sensor value : 200 kΩ ± 10 %
(Based on 25 ℃)
- Position : Rear part of outdoor device
- Sensor value : 10 kΩ ± 10 %
(Based on 25 ℃)
- Position : Compressor inlet and pipe
- Sensor value : 5 kΩ ± 10 %
(Based on 25 ℃)
ڸ
Compressor discharge sensor
ں
Outdoor temperature sensor
ڹ
Pipe sensor
200
Ω
5
Ω
5
Ω
Compressor
inlet sensor
Pipe sensor
10
Ω
Sensor Checking Methods
6.7 Troubleshooting Outdoor Error