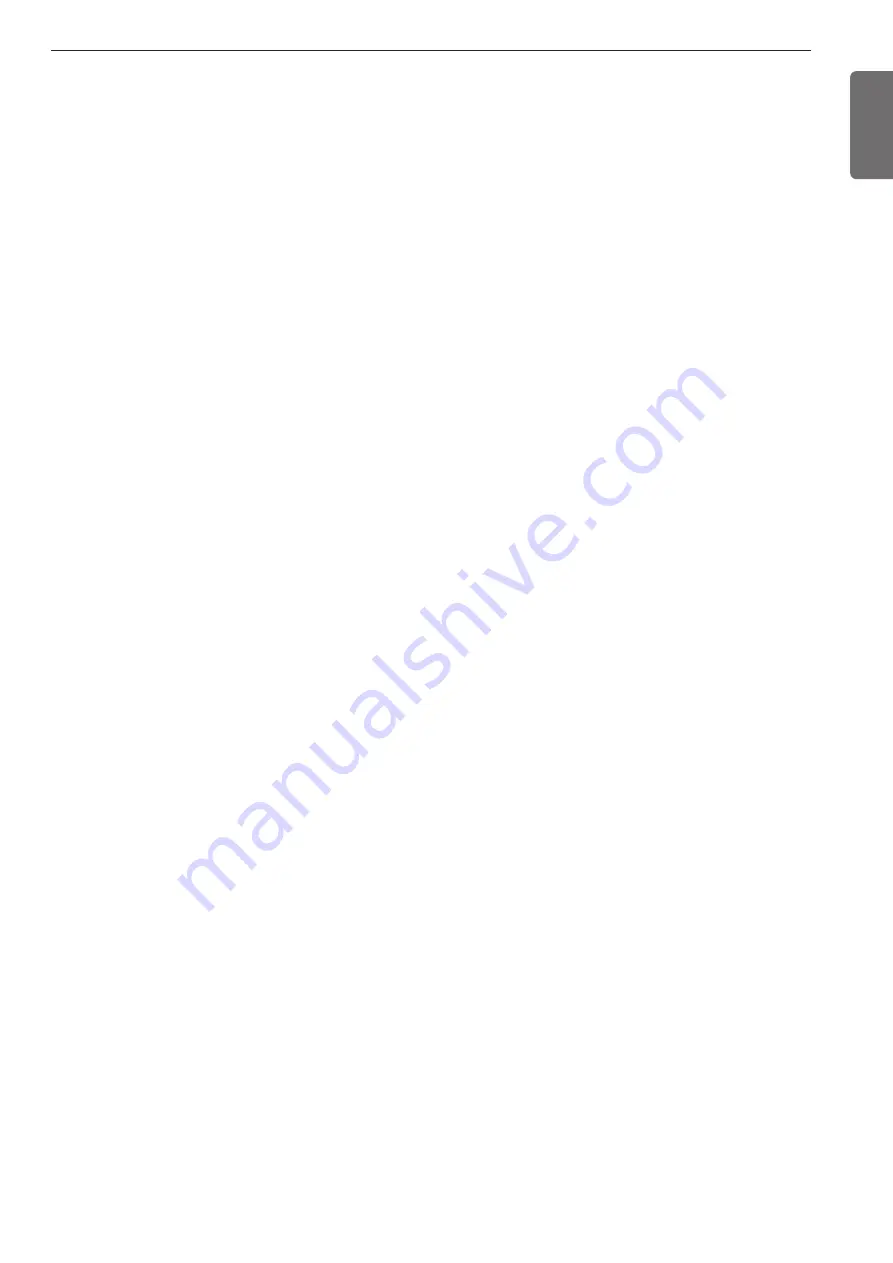
5
ENGLISH
• Do not change the settings.
- Do not change the settings of the control device or safety device.
Operating the product with improper settings may cause product damage.
Consult with the experts in the proper field when changing the control settings.
• Be cautious about fire, earthquake, and lightning.
- Stop operating the product immediately in case natural disasters such as fire, earthquake, or lightning occur or if
under the danger of thunderstroke. Operating the product continuously may cause a fire or electric shock.
• Observe the safety rules.
- Observe the precautions listed on the manuals, tags, stickers, and labels when operating the Chiller.
• Do not use a refrigerant that is not specified.
- Do not use a refrigerant or brine that is not specified. It may cause serious defects to the compressor and parts.
• Shut off the power during the installation and service process.
- Electric shock may cause injury and death.
Check all switches to ensure the electricity is not restored until the work is completed.
• Wear protective equipment.
- Wear protective glasses and gloves.
Be cautious when installing and handling the Chiller and handling electrical parts.
• Make sure that water always flows in the heat exchanger when filling or removing the refrigerant.
- This prevents the potential damage of the tube in the heat exchanger.
Adequately use cold water or brine in the water circulation loop to prevent the heat exchanger from freezing and
bursting when the Chiller is exposed to a temperature below 0°C
• Do not discharge the refrigerant through the refrigerant discharge valve inside of a building.
- The outlet of the discharge valve should be outside of a building. Leakage of the refrigerant in a closed area may
remove the oxygen and cause suffocation. Closed or low-ceiling areas need proper ventilation.
Inhaling the refrigerant is harmful to human health and may cause an irregular heartbeat, unconsciousness, and
death. Misuse can be fatal. As the refrigerant gas is heavier than the air, it reduces oxygen.
It can cause eye and skin irritation.
• Be cautious about leakage.
- Stop operation immediately when a leak is detected in the joints such as pumps and piping.
It may cause electric shock, short circuit or product failure.
• Be cautious about electric shock.
- Make sure to ground when installing the Chiller. It may cause electric shock.
• Do not leave the refrigerant system in the atmosphere for more than the required time.
- When a repair cannot be completed, shut the cycle and refill the dry nitrogen to prevent contamination and rust in
the machine.
1-2. CAUTION
• Make sure to check leakage of the refrigerant gas after installation and repair of the product.
- This may cause product failure.
• Do not install in a place with leakage of the combustible
- Installing in a place with leakage of the combustible may cause property damages.
• Keep the product at level when installing the product.
- Otherwise, the refrigerant level becomes unstable, and this may cause product failure.
• Do not use the product in spaces for special applications such as preservation of animal/plant, precision system, or
art works.
- This may cause property damages.
• Use the exclusive power cable of the enough allowable current capacity exclusively for the Chiller.
- This may cause fire and electric shock.
Summary of Contents for RCWFL Series
Page 40: ...40 ENGLISH 3 Control panel wiring diagram ...
Page 41: ...41 ENGLISH 3 Control panel wiring diagram ...
Page 42: ......