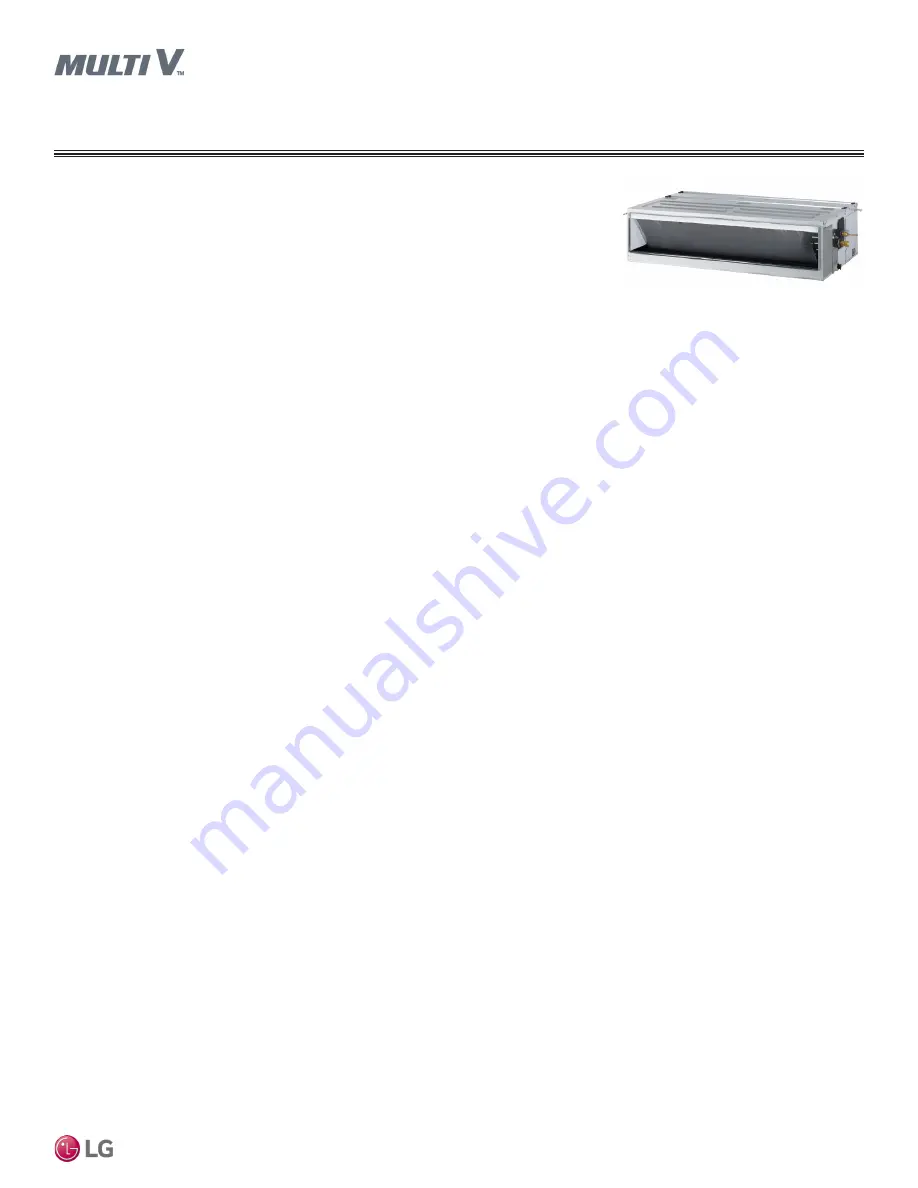
HIGH STATIC | 11
Ducted High Static
Due to our policy of continuous product innovation, some specifications may change without notification.
©
LG Electronics U.S.A., Inc., Englewood Cliffs, NJ. All rights reserved. “LG” is a registered trademark of LG Corp.
DUCTED HIGH STATIC
Mechanical Specifications
Casing
The case is designed to mount concealed above a finished ceiling.
Fan supply air is front horizontal with a dedicated rear horizontal
return. The unit is manufactured with coated metal. Cold surfaces
are covered with a coated polystyrene insulating material. The cold
surface areas of the case are covered externally with sheet insula-
tion made of Ethylene Propylene Diene Monomer (M-Class) (EPDM)
conforming to ASTM Standard D-1418. The case is provided with
hanger brackets designed to support the unit weight on four corners.
Hanger brackets have pre-punched holes designed to accept field
supplied, all-thread rod hangers.
Fan Assembly and Control
The unit has Sirocco fans made of high strength ABS GP-2200
polymeric resin. Fans are directly driven and mounted on a common
shaft. The fan motor is a Brushless Digitally Controlled (BLDC)
design with permanently lubricated and sealed ball bearings. The
fan motor includes thermal, overcurrent and low RPM protection.
The fan / motor assembly is mounted on vibration attenuating rubber
grommets. The fan impeller is statically and dynamically balanced.
The fan speed is controlled using a microprocessor based, direct
digital control algorithm that provides a high fan speed in cooling
thermal ON and low fan speed in cooling thermal OFF, high fan
speed in heating thermal ON and fan off in heating thermal OFF. The
fan speeds can be field adjusted between low, medium, and high
speeds and DIP switch settings will allow the fan to run constantly
during defrost or oil return modes. Each setting can be field adjusted
from the factory setting (RPM / ESP) to compensate for additional
resistance to airflow caused by field connected ductwork or other
airflow restricting devices.
Air Filter
Return air is filtered with a removable, washable filter with antifungal
treatment. MERV 13 filter modules with plenums available.
Microprocessor Controls
The unit is provided with an integrated microprocessor-based con-
troller. The controller is capable of performing functions necessary
to operate the system without the use of a wall-mounted controller.
A temperature thermistor is factory-mounted in the return air stream.
All unit operation parameters, excluding the unit operating schedule,
are stored in non-volatile memory resident on the unit microproces-
sor. Operating schedules are stored in select models of the optional,
wall-mounted, local, or central controller. The field supplied commu-
nication cable between the indoor unit(s) and outdoor unit is to be
a minimum of 18 AWG, 2-conductor, stranded, and shielded cable
(RS-485), terminated via screw terminals on the control boards.
The microprocessor control provides the following functions: auto
addressing, self-diagnostics, auto restart following power restoration,
test run, and will operate the indoor unit using one of five operating
modes:
1. Auto Changeover (Heat Recovery only)
2. Heating
3. Cooling
4. Dry
5. Fan Only
For Heat Recovery systems the Auto Changeover setting automati-
cally switches control of the indoor unit between cooling and heating
modes based on space temperature conditions.
For Heat Pump systems, heated or cooled air delivery is dependent
upon outdoor unit operating mode.
In Heating mode, the
microprocessor control
will activate the indoor unit
when indoor room
temperature falls below
setpoint temperature and
signals the outdoor unit to begin heating cycle. The indoor unit fan
operation is delayed until coil pipe temperature reaches 76ºF. Signif-
icant airflow is generated when pipe temperature reaches 80°F. In
lieu of factory return air thermistor, screw terminals on the micropro-
cessor circuit board accommodate various models of wall-mounted
local controllers and/or a wall-mounted remote temperature sensor.
The unit microprocessor is capable of accepting space temperature
readings concurrently or individually from either:
1. Wall-mounted wired controller(s)
2. Factory mounted return air thermistor or the optional wall-
mounted wired remote temperature sensor
A single indoor unit has the capability of being controlled by up to
two local wired controllers. The microprocessor controls space
temperature using the value provided by the temperature sensor
sensing a space temperature that is farthest away from the tem-
perature set-point. The microprocessor control provides a cooling or
heating mode test cycle that operates the unit for 18 minutes without
regard to the space temperature. If the system is provided with an
optional wall-mounted local or central controller, displayed diagnostic
codes are specific, alpha numeric, and provide the service technician
with a reason for the code displayed.
Condensate Lift/Pump
The indoor unit is provided with a factory installed and wired conden-
sate lift/pump capable of providing a minimum 27.5 inch lift from the
bottom exterior surface of the unit casing. The unit drain pan is pro-
vided with a secondary drain port/plug allowing the pan to be drained
for service. The lift pump comes with a safety switch that will shut off
indoor unit if condensate rises too high in the drain pan.
Condensate Drain Pan
The condensate drain pan is constructed of high impact polystyrene
resin (HIPS).
Coil
The indoor unit coil is constructed with grooved design copper tubes
with slit coil fins, two (2) to three (3) rows, nineteen (19) to
twenty-one (21) fins per inch.
Controls Features
• Auto changeover
(Heat Recovery only)
• Auto operation
• Auto restart
• External on/off control
• Dual thermistor control
• Dual setpoint control*
• Filter life display*
• Multiple auxiliary heater
applications*
• Group control
• External static pressure control
• Hot start
• Self diagnostics
• Timer (on / off)
• Weekly schedule
• Fan speed control
• Ventilation (outside air)
• Wi-Fi compatible
• Auto fan
• Leak detection
*To enable Generation 4 features, out-
door unit DIP Switch No. 3 must be set
to ON. Please refer to the Multi V IV,
Multi V Water IV, Multi V S Engineering
Manual for additional information.