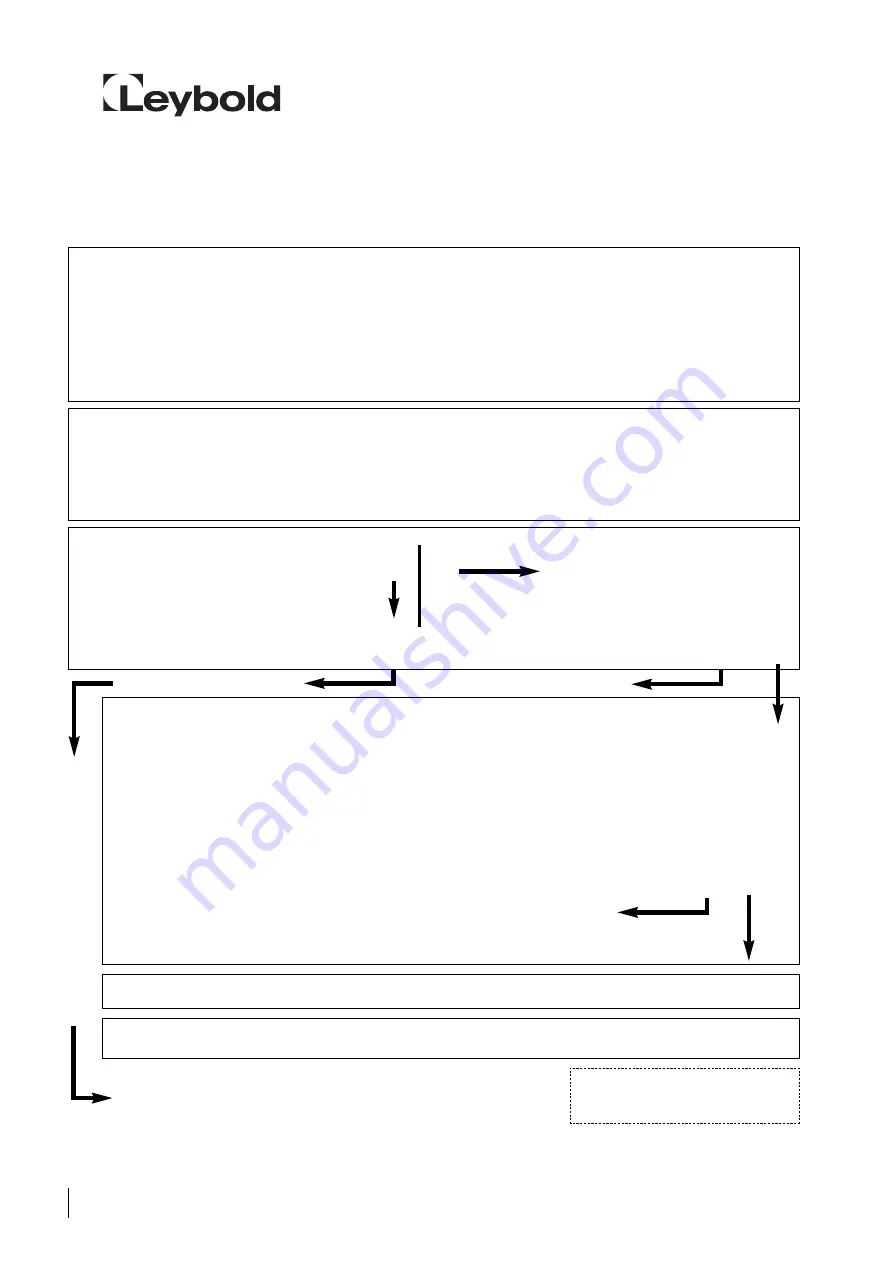
GA05141_0702 - 09/2004
108
vacuum
Declaration of Contamination of Compressors, Vacuum Pumps and Components
The repair and / or servicing of compressors, vacuum pumps and components will be carried out only if a correctly completed declaration has been sub-
mitted.
Non-completion will result in delay
. The manufacturer can refuse to accept any equipment without a declaration.
A separate declaration has to be copleted for every single component.
This declaration may be completed and signed only by authorised and qualified staff.
Customer/Dep./Institute:
________________________________
___________________________________________________
Address
___________________________________________
___________________________________________
Person to contact:
___________________________________
Phone:
__________________ Fax: __________________
Order number of customer:
______________________________
Reason for returning
"
applicable please mark
#
repair
#
chargeable
#
warranty
#
Austausch
#
chargeable
#
warranty
#
DKD-calibration
#
Factory calibration
restoring goods because of following reason:
#
rent/loan
#
for credit
#
against exchange
#
exchange already received/arranged
A. Description of the equipment (machine or component)
Ancillary equipment
Type:
_______________________________________
__________________________________________________
Part number:
_______________________________________
__________________________________________________
Serial number:
_______________________________________
__________________________________________________
Type of oil used:
_______________________________________
__________________________________________________
B. Condition of the equipment
No
Yes
No
Contamination:
No
Yes
1. Has the equipment been used
#
#
toxic
#
#
2. Drained (Product/service fluid)
#
#
corrosive
#
#
3. All openings sealed airtight
#
mmicrobiological
#
#
4. Purged
#
#
explosive
#
#
If yes which cleaning agent:
_______________________________________
radioactive
#
#
and which method of cleaning:
_______________________________________
other harmful substances
#
#
C. Description of processed substances (Please fill in absolutely)
1. What substances have come into contact with the equipment:
Trade name and / or chemical term of service fluids and substances processed, properties of the substances; According to safety data sheet
(e.g. toxic, inflammable, corrosive, radioactive)
Tradename:
Chemical name:
Residues:
a) ____________________________________________________________________________________
#
Yes
#
No
b) ____________________________________________________________________________________
#
Yes
#
No
c) ____________________________________________________________________________________
#
Yes
#
No
d) ____________________________________________________________________________________
#
Yes
#
No
Yes
No
2. Are these substances harmful?
#
#
3. Dangerous decomposition products when thermally loaded
#
#
Which:
Components contaminated by microbiological, explosive or radioactive products will not be accepted
without written evidence of decontamination.
D. Legally binding declaration
I / we hereby declare that the information supplied on this form is accurate and sufficient to judge any contamination level.
Name of authorised person (block letters):
____________________________
date _____________
signatur of authorised person ___________________________
firm stamp
© Leybold Vacuum Köln
Summary of Contents for MAG 1500 CT
Page 107: ...GA05141_0702 09 2004 107 Notes...