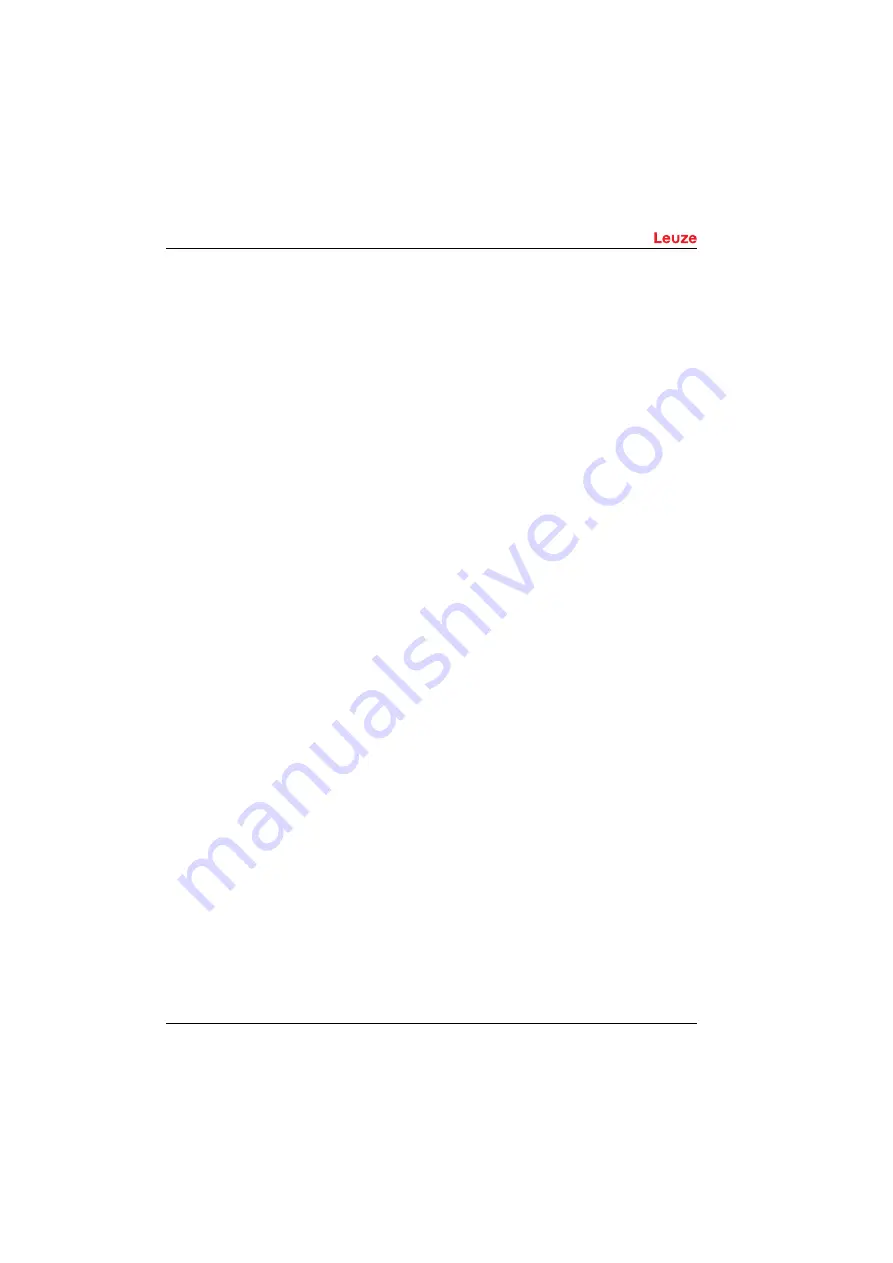
PROFINET interface
64
AMS 348
i
SSI
Leuze electronic GmbH + Co. KG
File name structure
The file name of the GSD file is constructed according to the following rule:
GSDML-[GSDML schema version]-Leuze-AMS348i-[date].xml
Explanation:
• GSDML schema version:
Version identifier of the GSDML schema version used, e.g., V2.3
• Date:
Release date of the GSD file in the format yyyymmdd.
This date also stands for the version identifier of the file.
Example:
GSDML-V2.3x-Leuze-AMS348i-20090503.xml
The GSD file can be found at www.leuze.com.
All data in modules required for operating the AMS 348
i
is described in this file. These are
input and output data and device parameters for the functioning of the AMS 348
i
and the defi
-
nition of the control and status bits.
If parameters are changed, e.g., in the project tool, these changes are stored on the PLC
side in the project, not in the GSD file. The GSD file is a certified and integral part of the device
and must not be changed manually. The file is not changed by the system either.
The functionality of the AMS 348
i
is defined via GSD parameter sets. The parameters and
their functions are structured in the GSD file using modules. A user-specific configuration
tool is used during PLC program creation to integrate the required modules and configure
them appropriately for their respective use. During operation of the AMS 348
i
on the
PROFINET, all parameters are set to default values. If these parameters are not changed
by the user, the device functions with the default settings delivered by Leuze.
For the default settings of the AMS 348
i
, please refer to the following module descriptions.