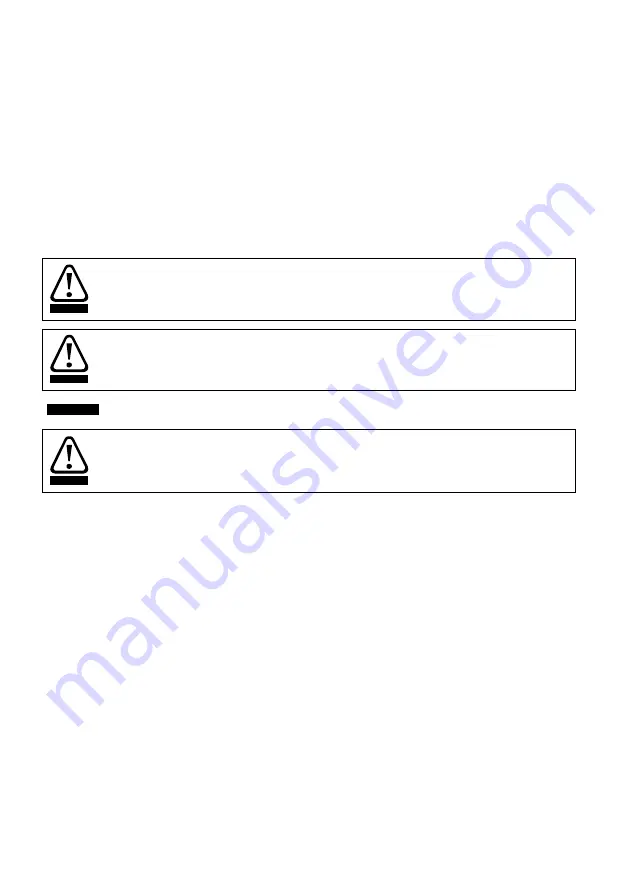
Original Instructions
For the purposes of compliance with the EU Machinery Directive 2006/42/EC
This guide is intended to provide basic information required in order to set-up a drive to run a motor.
For more detailed installation information, please refer to the relevant drive documentation which is
available to download from:
www.drive-setup.com
Warnings, Cautions and Notes
Copyright
© March 2017
Issue Number: 7
A Warning contains information which is essential for avoiding a safety hazard.
A Caution contains information which is necessary for avoiding a risk of damage to the
product or other equipment.
A
Note
contains information, which helps to ensure correct operation of the product.
This guide does not include safety information. Incorrect installation or operation of the
drive, could cause personnel injury or equipment damage. For essential safety
information, please refer to the relevant drive documentation or the safety booklet supplied
with the drive.
WARNING
CAUTION
NOTE
WARNING