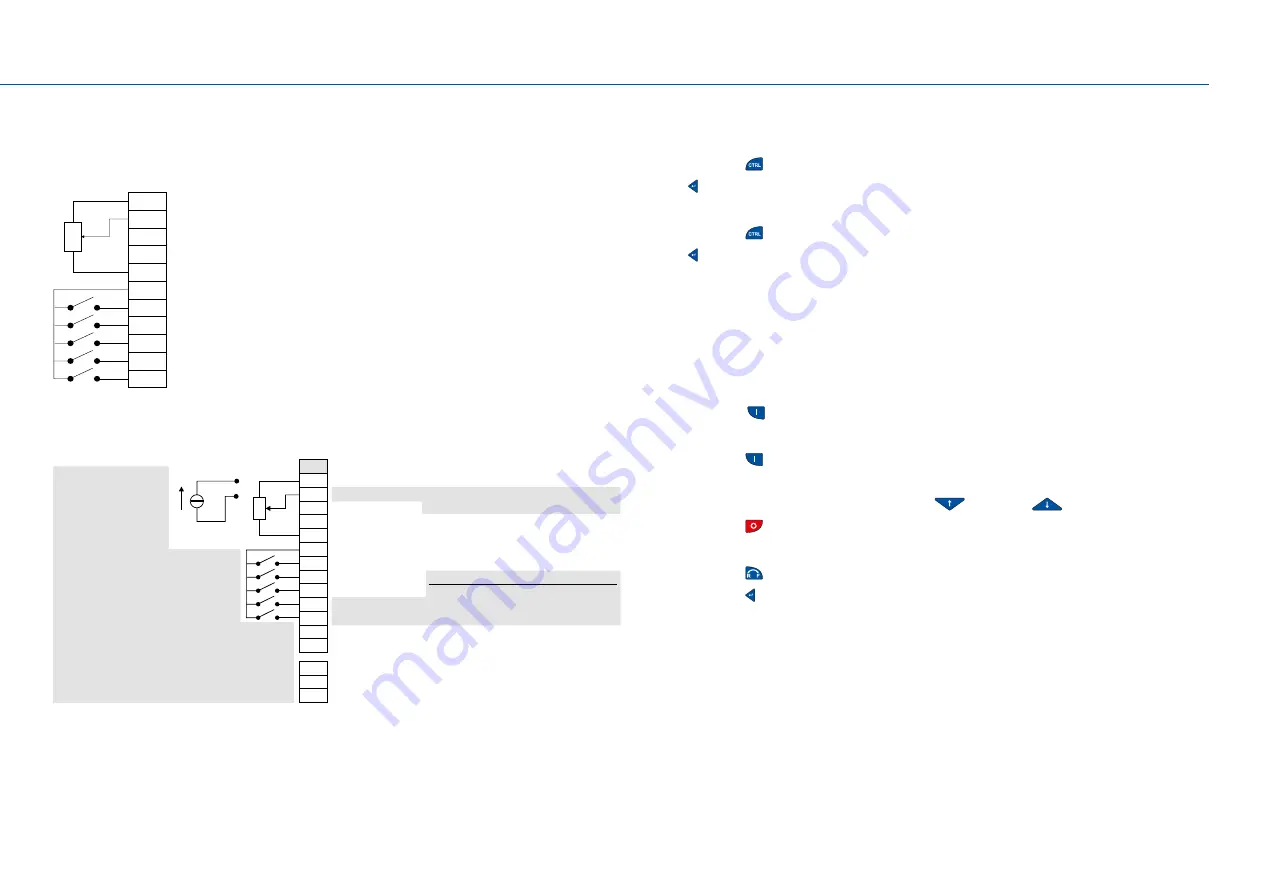
17
Commissioning
Operating instructions I510-Cabinet
With the wiring shown below, the inverter can be operated using the control terminals (X3).
• Preset 1 is activated if DI4 = HIGH.
• Preset 2 is activated if DI5 = HIGH.
• Preset 3 is activated if DI4 and DI = HIGH.
GND
AI1
AI2
AO1
10V
24V
DI1
DI2
DI3
DI4
DI5
Setpoint frequency
10 VDC supply
24 VDC, 100 mA supply
Start
Reset error (optional)
Change direction of rotation (optional)
Activate preset (Bit 0) (optional)
Activate preset (Bit 1) (optional)
GND
Input range [Hz]:
*P430.02 - *P430.03
7.1.4
Extended terminal control
The following illustration shows a more extensive wiring of the control terminals (X3) linked
with the respective parameters.
GND
AI1
AI2
AO1
10V
24V
DI1
DI2
DI3
DI4
DI5
GND
DO1
NO
COM
NC
U/I
*P400.02
Preset 01 (*P450.01)
*P400.04
*P400.13
bit 1 bit 0
0
0
1
1
1
1
Preset 02 (*P450.02)
Preset 03 (*P450.03)
*P400.18
*P400.19
*P420.02
*P420.01
24E
*P201.01
(congured AI1 as
standard setpoint)
Default setting
Start
Reset error
Mark direction of rotation
Activate preset (bit 0)
Activate preset (bit 1)
DO1 activated at
Release brake
Relay activated at
Ready for operation
Analog input 1
Analog input 2
Analog output 1
10 VDC supply for potentiometer
24 VDC, 100 mA supply, reference for digital inputs
Digital input 1
Digital input 2
Digital input 3
Digital input 4
Digital input 5
Digital output 1
GND for analog and digital signals
Relay NO contact
Relay common contact
Relay NC contact
Preset frequency values
*P430.01
(0 ... 10 VDC signal)
*P430.02 — *P430.03
GND for analog and digital signals
range [Hz]:
cong.:
Optional external 24-V-supply (i550 only)
7.2 Keypad control
Activate temporary keypad control
1. Press the key to activate keypad control.
2. Key for confirming keypad control.
Deactivate temporary keypad control
1. Press the key to activate keypad control.
2. Key for confirming keypad control.
Activate permanent keypad control
If the keypad does not have any keys, motor control is activated via the following parameters:
►
Set parameter P200.00 to 1.
►
Set parameter P201.01 to 1.
►
Set parameter P400.01 to 1.
►
Set parameter P400.02 to 1.
Then use the key to start the motor.
Start/control/stop motor with keypad
1. Press the key to start the motor.
• The keypad shows the motor speed.
2. Change the frequency setpoint using the key
or the key
.
3. Press the key to stop the motor.
Change rotating direction
1. Press the key .
2. Press the key to confirm the reversal of rotating direction.
7.3 Commissioning with the EASY Starter
Commissioning and diagnostics can be carried out with the EASY starter engineering tool.
http://www.Lenze.com