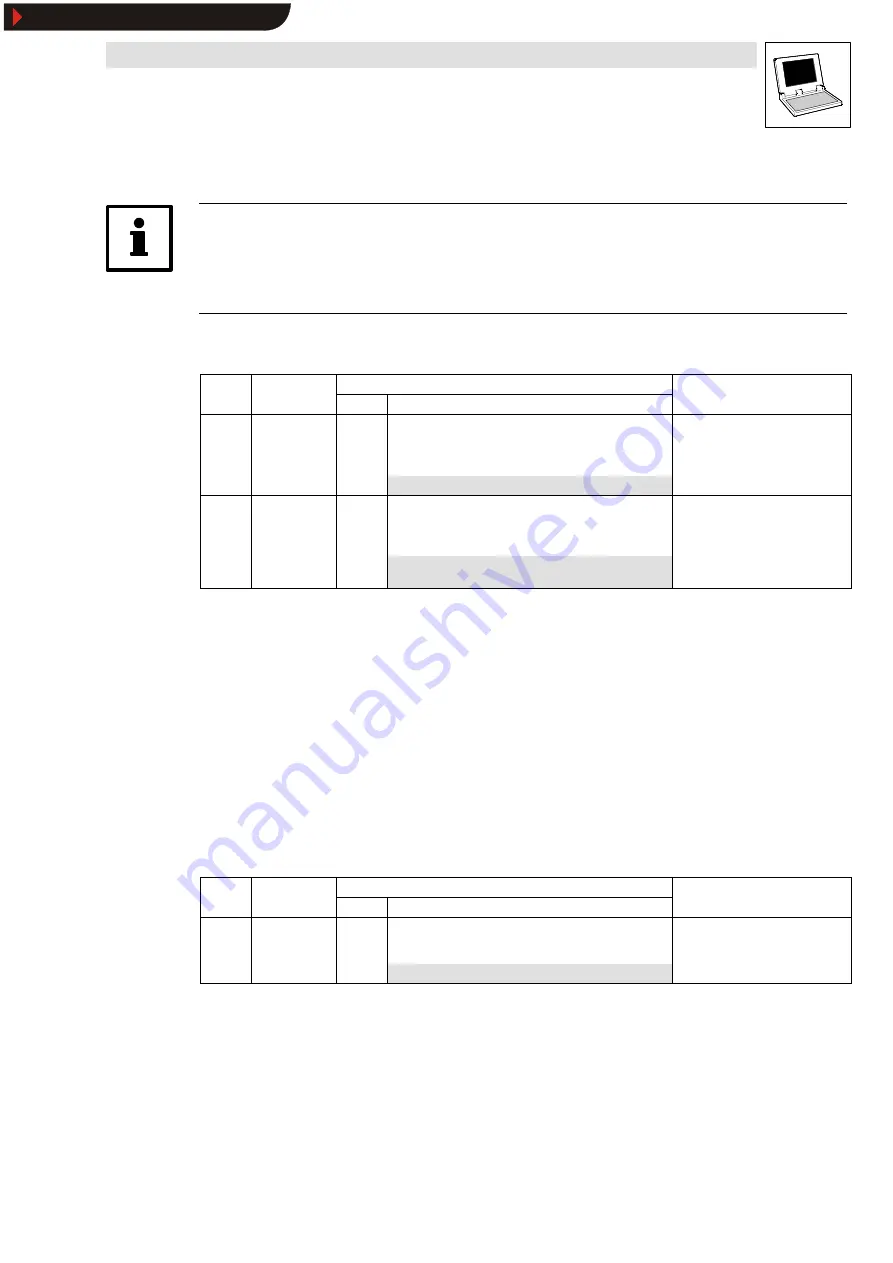
9300 Servo PLC
System blocks
2.12
MCTRL_MotorControl
2-43
L
ServoPLC EN 2.0
2.12.3
Current controller
Tip!
Select a matching motor under C0086 from the “Motor selection list”. This automatically sets the
correct parameters for the current controller.
•
The “Motor selection list” can be found in the 9300 Servo Mounting Instructions.
•
The proportional gain for the controller is set under C0075 and the readjustment time to adapt
it to the connected machine is set under C0076:
Code
LCD
Possible settings
Info
o
Lenze
Selection
o
C0075 Vp curr CTRL
à
V
pi
Current controller
à
depending on C0086
•
Change of C0086 resets value to
the assigned default setting
0.00
{0.01}
15.99
C0076 Tn curr CTRL
à
T
ni
Current controller
à
depending on C0086
•
Change of C0086 resets value to
the assigned default setting
0.5
{0.1 ms}
2000.0
2000 ms = switched off
2.12.4
Additional torque setpoint
MCTRL_nMAdd_a
- depending on the settings of
MCTRL_bNMSwt_b
- as a torque setpoint or an
additional torque setpoint.
Torque setpoint
With
MCTRL_bNMSwt_b
= TRUE, the torque control is active.
•
MCTRL_nMAdd_a
acts as a torque setpoint.
•
The n-controllers have a monitoring function.
•
The torque setpoint is selected as percentage [% ] of the max. possible torque.
– Negative values mean a torque with CCW rotation of the motor.
– Positive values mean a torque with CW rotation of the motor.
•
The max. possible torque is set under C0057:
Code
LCD
Possible settings
Info
o
Lenze
Selection
o
C0057 Max Torque
g
Maximum possible torque of the drive
configuration
•
depending on C0022, C0086
0.0
{0.1 Nm}
500.0
Additional torque setpoint
With
MCTRL_bNMSwt_b
= FALSE, the speed control is active.
•
MCTRL_nMAdd_a
is added to the output of the n-controller.
•
The limits given by the torque limiting
MCTRL_nLoMLim_a
and
MCTRL_nHiMLim_a
cannot be
exceeded.
•
The additional torque setpoint can be used, for example for friction compensation or to add
acceleration (dv/dt).
efesotomasyon.com - Lenze
Show/Hide Bookmarks