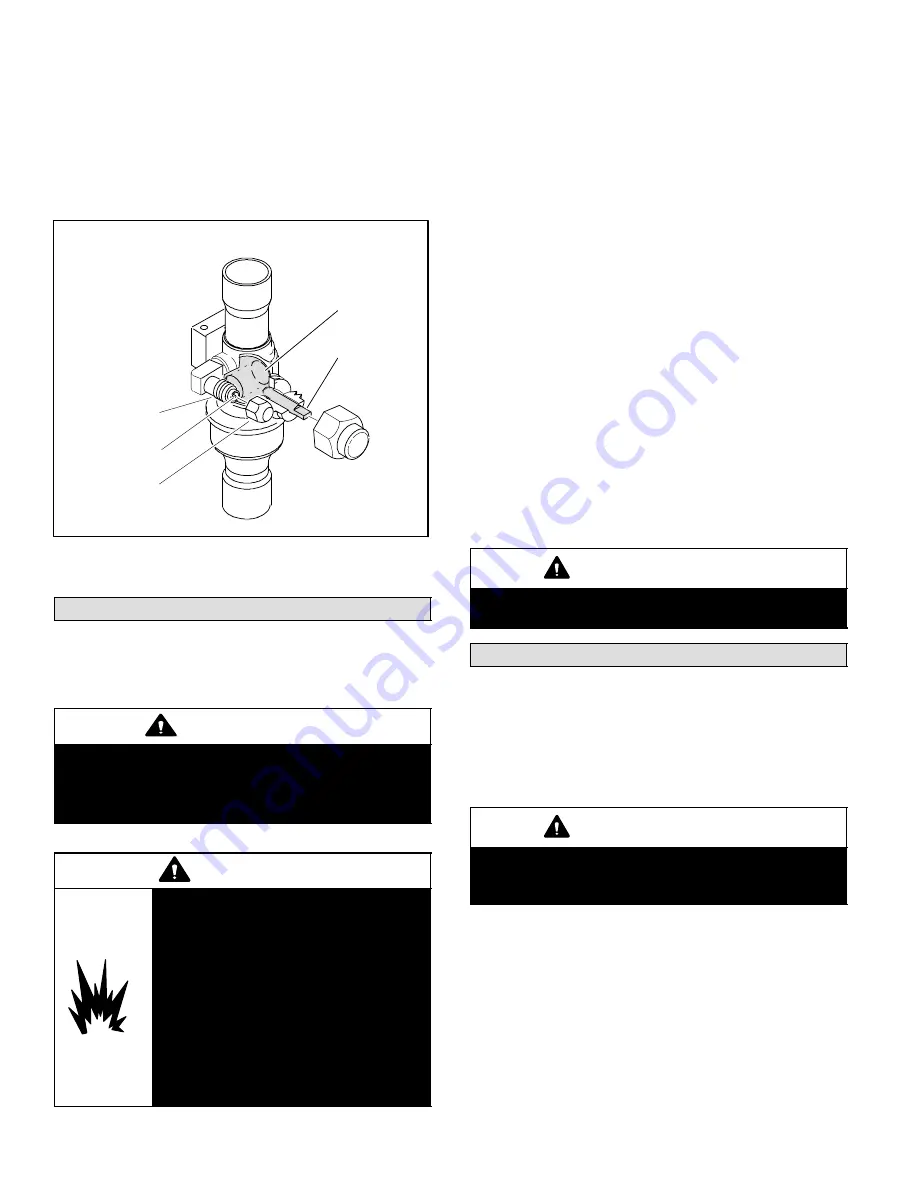
Page 12
505095M 1/3/06
Vapor Line (Ball Type) Service Valve
Vapor line service valves function the same way as the oth-
er valves; the difference is in the construction. These
valves are not rebuildable. If a valve fails, replace it. The
ball valve (shown in figure 16) is equipped with a service
port with a factory−installed Schrader valve. A service port
cap protects the Schrader valve from contamination and
assures a leak−free seal.
Ball−Type Vapor Line Valve (Valve Closed)
Figure 16
BALL
(Shown
closed)
STEM
STEM
CAP
SERVICE
PORT
SCHRADER
VALVE
SERVICE
PORT CAP
To indoor coil
To outdoor coil
Use Adjustable Wrench
To close: rotate Stem
Counter-clockwise 90°.
To open: rotate Stem
Clockwise 90°.
Leak Testing
After the line set has been connected to the indoor and out-
door units, check the line set connections and indoor unit
for leaks.
WARNING
Refrigerant can be harmful if it is inhaled. Refriger-
ant must be used and recovered responsibly.
Failure to follow this warning may result in personal
injury or death.
WARNING
Danger of explosion: Can cause inju-
ry or death, or equipment damage.
Never use oxygen to pressurize a re-
frigeration or air conditioning system.
Oxygen will explode on contact with
oil and could cause personal injury.
When using a high pressure gas such
as dry nitrogen to pressurize a refrig-
eration or air conditioning system,
use a regulator that can control the
pressure down to 1 or 2 psig (6.9 to
13.8 kPa).
Leak Test with Electronic Leak Detector
1. Connect an R−410A manifold gauge set high pressure
hose to the vapor valve service port.
(Normally, the
high pressure hose is connected to the liquid line port;
however, connecting it to the vapor port better protects
the manifold gauge set from high pressure damage.)
2. With both manifold valves closed, connect the cylinder
of R−410A refrigerant to the center port of the manifold
gauge set. Open the valve on the R−410A cylinder (va-
por only).
3. Open the high pressure side of the manifold to allow
R−410A into the line set and indoor unit. Weigh in a
trace amount of R−410A.
[A trace amount is a maxi-
mum of 2 ounces (57 g) refrigerant or 3 pounds (31
kPa) pressure].
Close the valve on the R−410A cylin-
der and the valve on the high pressure side of the man-
ifold gauge set. Disconnect the R−410A cylinder.
4. Connect a cylinder of dry nitrogen with a pressure reg-
ulating valve to the center port of the manifold gauge
set.
5. Adjust dry nitrogen pressure to 150 psig (1034 kPa).
Open the valve on the high side of the manifold gauge
set in order to pressurize the line set and the indoor unit.
6. After a few minutes, open a refrigerant port to ensure
the refrigerant you added is adequate to be detected.
(Amounts of refrigerant will vary with line lengths.)
Check all joints for leaks. Purge dry nitrogen and
R−410A mixture. Correct any leaks and recheck.
IMPORTANT
Leak detector must be capable of sensing HFC re-
frigerant.
Evacuation
Evacuating the system of noncondensables is critical for
proper operation of the unit. Noncondensables are defined
as any gas that will not condense under temperatures and
pressures present during operation of an air conditioning
system. Noncondensables and water vapor combine with
refrigerant to produce substances that corrode copper pip-
ing and compressor parts.
IMPORTANT
Use a thermocouple or thermistor electronic vacuum
gauge that is calibrated in microns. Use an instrument
that reads from 50 microns to at least 23,000 microns.
1. Connect manifold gauge set to the service valve ports
as follows:
D
low pressure gauge to
vapor
line service valve
D
high pressure gauge to
liquid
line service valve
2. Connect micron gauge.
3. Connect the vacuum pump (with vacuum gauge) to
the center port of the manifold gauge set.
4. Open both manifold valves and start the vacuum
pump.
5. Evacuate the line set and indoor unit to an
absolute
pressure
of 23,000 microns (29.01 inches of mercu-