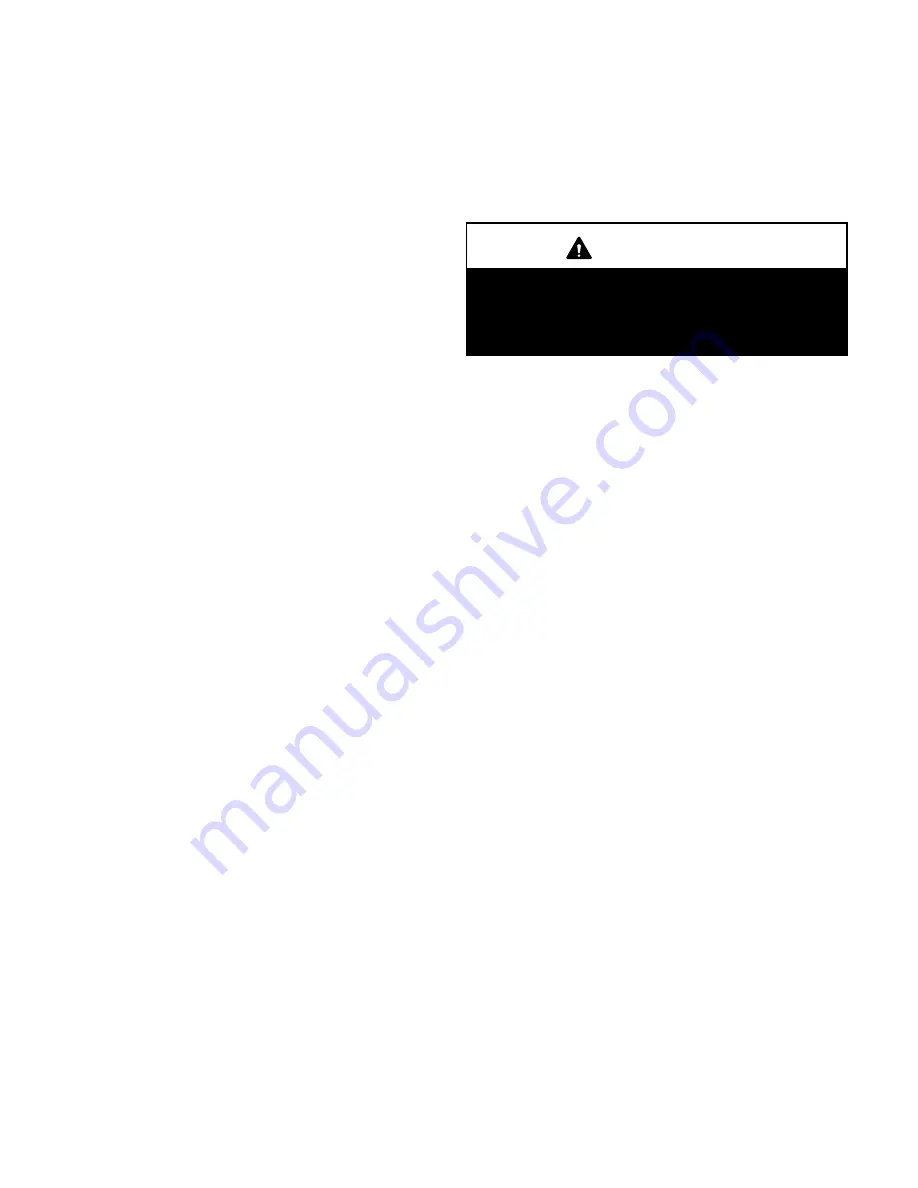
Page 14
VI − MAINTENANCE
In order to maintain the warranty on this equipment, the
XP13 system must be serviced annually and a record of
service maintained. The following should be checked be-
tween annual maintenance:
A − Outdoor Unit
1 − Clean and inspect the outdoor coil. The coil may be
flushed with a water hose. Ensure the power is turned
off before you clean the coil.
2 − Condenser fan motor is prelubricated and sealed. No
further lubrication is needed.
3 − Visually inspect connecting lines and coils for evidence
of oil leaks.
4 − Check wiring for loose connections.
5 − Check for correct voltage at unit (unit operating).
6 − Check amp−draw condenser fan motor.
Unit nameplate _________ Actual ____________ .
NOTE − If owner complains of insufficient cooling, the unit
should be gauged and refrigerant charge checked. Refer
to section on refrigerant charging in this instruction.
1 − Clean and inspect condenser coil. (Coil may be flushed
with a water hose after disconnecting power).
2 − Visually inspect all connecting lines, joints and coils for
evidence of oil leaks.
B − Indoor Coil
1 − Clean coil, if necessary.
2 − Check connecting lines and coils for evidence of oil
leaks.
3 − Check the condensate line and clean it if necessary.
C − Indoor Unit
1 − Clean or change filters.
2 − Adjust blower speed for cooling. Measure the pressure
drop over the coil to determine the correct blower CFM.
Refer to the unit information service manual for pressure
drop tables and procedure.
3 −
Belt Drive Blowers −
Check belt for wear and proper ten-
sion.
4 − Check all wiring for loose connections
5 − Check for correct voltage at unit (blower operating).
6 − Check amp−draw on blower motor
Unit nameplate_________ Actual ____________.
VII − BRAZING
Before brazing remove access panels and any piping pan-
els to avoid burning off paint. Be aware of any components
ie, service valves, reversing valve, pressure switches that
may be damaged due to brazing heat.
When making line set connections, use 1 to 2 psig dry nitro-
gen to purge the refrigerant piping. This will help to prevent
oxidation into the system.
WARNING
Danger of explosion: Can cause equipment damage,
injury or death. When using a high pressure gas such
as dry nitrogen to pressurize a refrigeration or air
conditioning system, use a regulator that can control
the pressure down to 1 or 2 psig (6.9 to 13.8 kPa).
1 − .Cut ends of copper square (free from nicks or dents).
Debur the ends. The pipe must remain round, do not
pinch end of line.
2 − Wrap wet rag around any components that may be da-
maged.
3 − Use silver alloy brazing rods (5 or 6 percent minimum
silver alloy for copper to copper brazing or 45 percent
silver alloy for copper to brass or copper to steel braz-
ing) which are rated for use with R−22 and R−410A re-
frigerant.
4 − After brazing quench the joints with a wet rag to prevent
possible heat damage to any components.