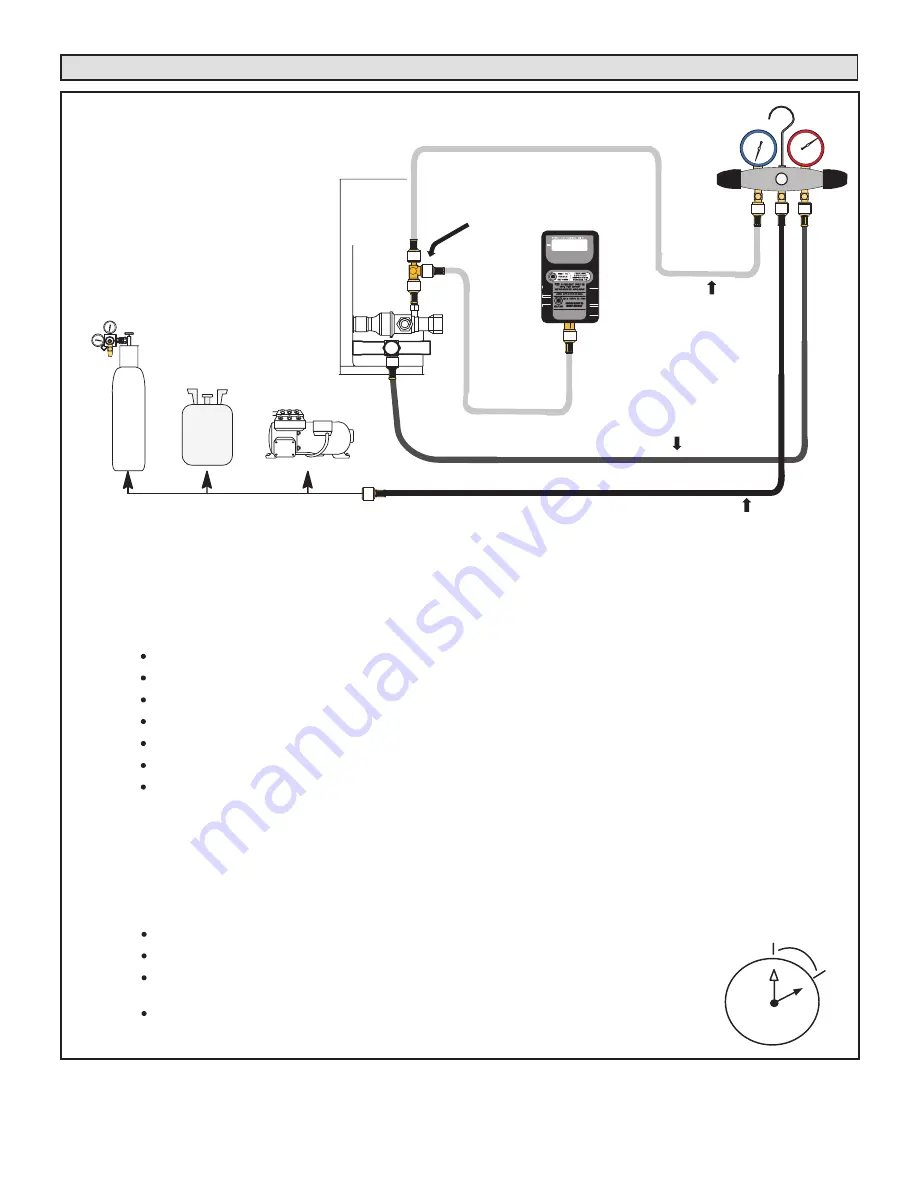
Page 17
Evacuating Line Set and Indoor Coil
A
Open both manifold valves and start the vacuum pump.
B
Evacuate the line set and indoor unit to an
absolute pressure
of 23,000 microns (29.01 inches of mercury).
NOTE — During the early stages of evacuation, it is desirable to close the manifold gauge valve at least once. A rapid rise in pressure
indicates a relatively large leak. If this occurs,
repeat the leak testing procedure.
NOTE — The term absolute pressure means the total actual pressure within a given volume or system, above the absolute zero of
pressure. Absolute pressure in a vacuum is equal to atmospheric pressure minus vacuum pressure.
C
When the absolute pressure reaches 23,000 microns (29.01 inches of mercury), perform the following:
Close manifold gauge valves
Close valve on vacuum pump
Turn off vacuum pump
Disconnect manifold gauge center port hose from vacuum pump
Attach manifold center port hose to a dry nitrogen cylinder with pressure regulator set to 150 psig (1034 kPa) and purge the hose.
Open manifold gauge valves to break the vacuum in the line set and indoor unit.
Close manifold gauge valves.
D
Shut off the dry nitrogen cylinder and remove the manifold gauge hose from the cylinder. Open the manifold gauge valves to release the
dry nitrogen from the line set and indoor unit.
E
Reconnect the manifold gauge to the vacuum pump, turn the pump on, and continue to evacuate the line set and indoor unit until the
absolute pressure does not rise above 500 microns (29.9 inches of mercury) within a 20-minute period after shutting off the vacuum pump
and closing the manifold gauge valves.
F
When the absolute pressure requirement above has been met, disconnect the manifold hose from the vacuum pump and connect it to an
upright cylinder of HFC-410A refrigerant. Open the manifold gauge valve 1 to 2 psig in order to release the vacuum in the line set and
indoor unit.
G
Perform the following:
OUTDOOR
UNIT
TO VAPOR
SERVICE VALVE
TO LIQUID LINE
SERVICE VALVE
MICRON
GAUGE
VACUUM PUMP
A34000 1/4 SAE TEE WITH
SWIVEL COUPLER
500
MANIFOLD
GAUGE SET
HFC-410A
RECOMMEND
MINIMUM 3/8” HOSE
A
Connect low side of manifold gauge set
with 1/4 SAE in-line tee to
vapor
line
service valve
B
Connect high side of manifold gauge
set to
liquid
line service valve
C
Connect micron gauge available
connector on the 1/4 SAE in-line tee.
D
Connect the vacuum pump (with
vacuum gauge) to the center port of the
manifold gauge set. The center port
line will be used later for both the
HFC-410A and nitrogen containers.
HIGH
LOW
1
2
3
4
5
6
7
8
9
10
11 12
1/6 TURN
NITROGEN
1
CONNECT GAUGE SET
A
B
C
D
2
EVACUATE THE SYSTEM
NOTE
— Remove cores from service valves (if not already done).
Close manifold gauge valves.
Shut off HFC-410A cylinder.
Reinstall service valve cores by removing manifold hose from service valve. Quickly install cores with core
tool while maintaining a positive system pressure.
Replace stem caps and secure finger tight, then tighten an additional one-sixth (1/6) of a turn as illustrated.
FIGURE 10. Evacuating the System