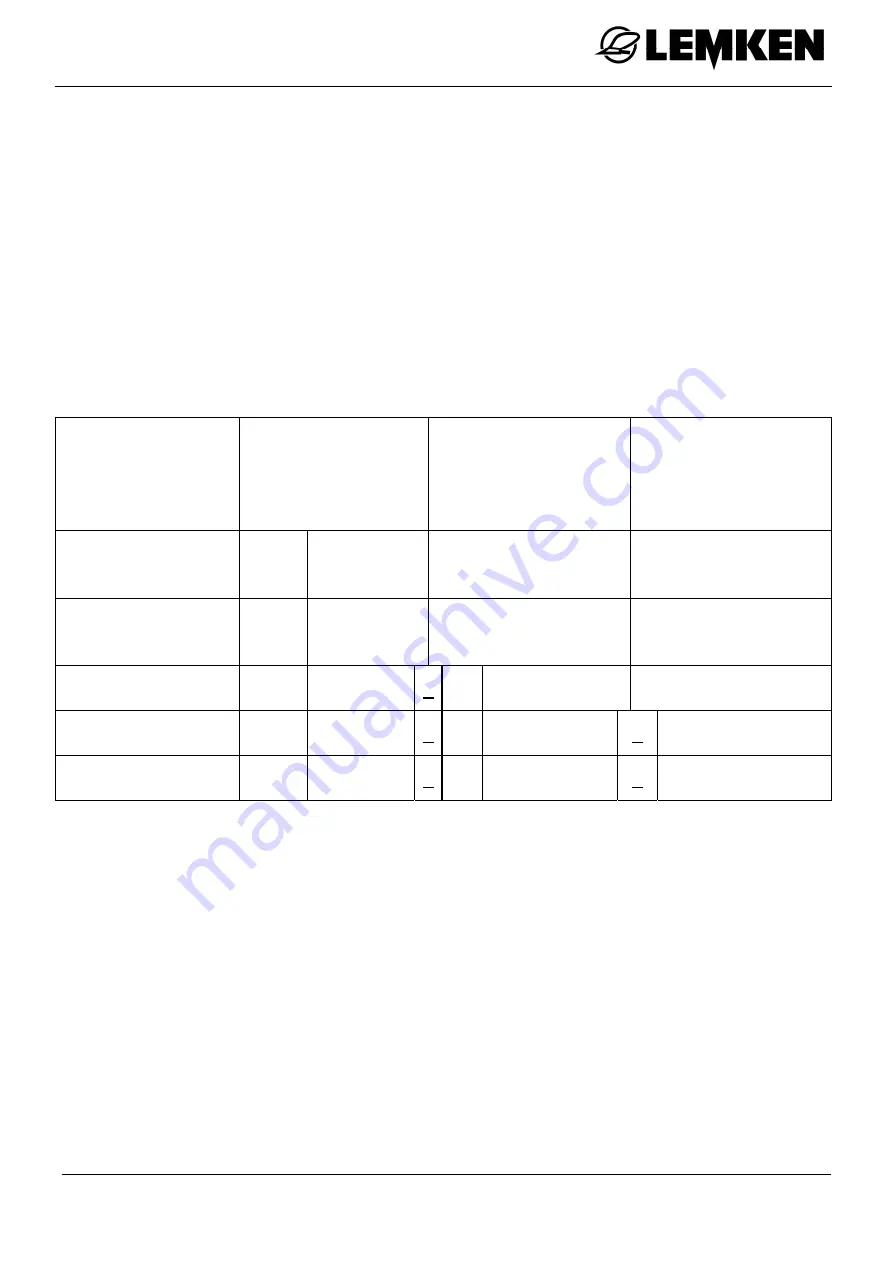
Safety measures and precautions
25
Calculation of actual rear axle load T
H tat
Enter the value for the calculated actual rear axle load and the permissible rear
axle load as given in the tractor's operating instructions into the table.
Tyre load-carrying capacity
Enter double the value (for two tyres) for the permissible tyre load-carrying ca-
pacity (see, e.g. tyre manufacturer's documentation) into the table.
Table
Actual value ac-
cording to calcula-
tion
Permissible value
according to tractor
operating instructions
Double permissible
tyre load-carrying
capacity
[two tyres]
Minimum ballas-
ting, front
G
V min
kg
- -
Minimum ballas-
ting, rear
G
H min
kg
- -
Gross weight
G
tat
kg <
T
L
kg -
Front axle load
T
V tat
kg <
T
V
kg
<
kg
Rear axle load
T
H tat
kg <
T
H
kg
<
kg
3.9.4 Check before departure
Before driving with the implement raised, lock the control lever of the control
unit; otherwise it may drop and the implement may be unintentionally lowered.
Mount and check the transport equipment such as the lighting system, warning
signs and protective devices.
The actuating cables for the quick-release couplings of the tractor must hang
loose and must not actuate themselves in any position.
Before starting up and operating the implement, check the immediate vicinity
around it. No-one must be standing in this area!
Ensure that visibility is adequate.
Observe permitted axle loads, total weights and transportation dimensions.
T
H tat
= G
tat
- T
V tat